Logistics Strategy & Performance: Essential Tips for Success
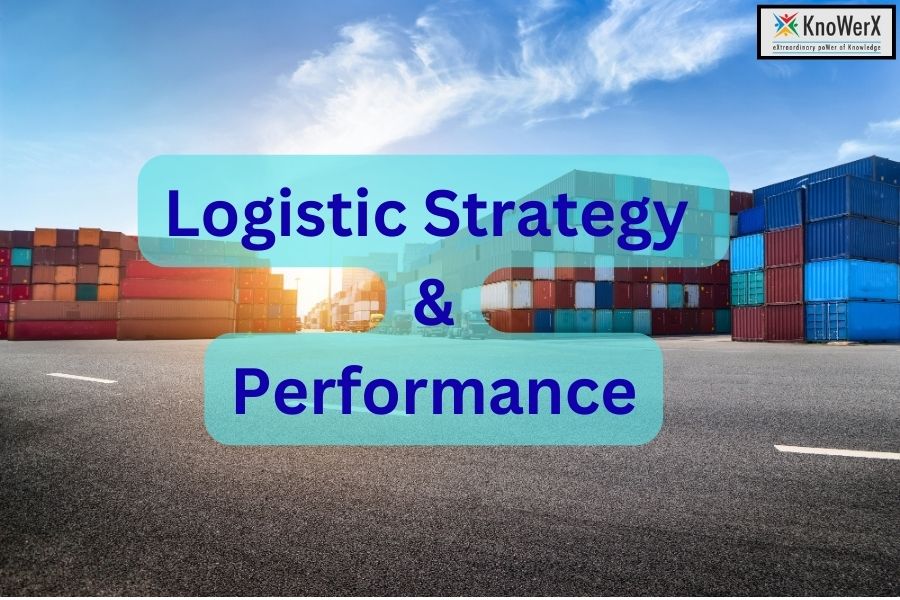
Logistics Strategy & Performance: Essential Tips for Success Logistics forms the backbone of a bigger supply chain, driving efficiency and great value to businesses’ operational activities. It ensures enhanced performance in operations, decreased cost, and, hence, better customer satisfaction. Below are some important guidelines on how to help understand logistics and implement efficient strategies in your organization. 1. Understand the Economic Drivers of Logistics The primary drivers of logistics are economics, including transportation costs, inventory management, and the ups and downs of demand. A well-optimized logistics strategy addresses these drivers through cost-effective transportation routes, reduced excess inventory, and timely delivery. Understanding these economic principles will help logistics managers make better decisions in their efforts to enhance operational efficiency and reduce overall costs. 2. Acknowledge how logistics fits into supply chain management Logistics is the aspect of a supply chain that is involved in the movement and storage of goods. Logistics is an integrated function of the procurement, production, and distribution functions within a supply chain. In synchronizing logistics operations with other supply chain elements, businesses ensure smooth operation, faster delivery times, and greater customer satisfaction. Logistics cannot be seen in isolation but rather as part of a broader supply chain strategy. 3. Run Your Logistics Strategy on a Strong Value Proposition A good logistics strategy should align with the business goals. A clear definition of the logistics value proposition will allow businesses to focus on fast delivery times, cost reduction, and increased product availability. The value proposition becomes a competitive advantage for businesses and enables them to differentiate themselves from competitors. Reviewing the value proposition regularly will ensure that logistics operations are continuously improving and contributing to overall business success. 4. Design Agile Logistics Frameworks and Partnerships Flexibility is the order of the day in this dynamic business environment to ensure proper logistics management. The agility of the logistics frameworks provides an edge to respond swiftly to variations in demand and supply chain disruptions. Collaborative partnerships with suppliers, distributors, and third-party logistics firms will help enhance the logistics operation process, decrease delays, and improve service levels. 5. Study Strategic Level Risk Management in Logistics Logistics management also entails understanding and managing risks. Risks could vary from transportation delays and failures of suppliers to unmet demand. A strategic-level approach to risk management in logistics helps identify potential risks, assess their impact, and develop mitigation strategies. Thus, preparing for contingencies can ensure business continuity as well as protect the company’s reputation. 6. Employ Basic Performance Measurements and Benchmarking To ensure that logistics operations are meeting business goals, it’s essential to monitor key performance indicators (KPIs). These KPIs could include transportation costs, delivery lead times, order accuracy, and customer satisfaction. Benchmarking these metrics against industry standards or competitors helps identify areas for improvement. Regular performance assessments enable logistics managers to make data-driven decisions that enhance efficiency. 7. Implement Re-engineering and Continuous Improvement Philosophies Logistics operations can’t be static. Continuous improvement philosophies such as lean management or Six Sigma would ensure processes are streamlined, waste reduced, and service levels improved. Regular re-engineering of logistics processes will ensure the organization is ahead of market trends and scales efficiently. Investment in technology and training programs can also look to contribute to continued improvement in logistics management. 8. Use Technology to Optimize Logistics The major role of technology is that it acts as a pivotal element to shift logistics strategies. Technologies like warehouse management systems, transportation management systems, and predictive analytics can help a company bring in more efficiency, minimize operational costs, and upgrade the decision-making process. Companies can automate regular tasks and reduce routes by leveraging technology and can track their inventory and predict demand accurately. Such agility and responsiveness make the logistics operation sensitive to change in the market. 9. Sustainability in Logistics Sustainability is fast becoming a factor in the strategy of logistics. Consumers and businesses are increasingly focusing on environmentally friendly practices. Incorporating sustainability into logistics includes optimizing transportation routes to minimize carbon footprints, using eco-friendly packaging, and investing in energy-efficient warehouse solutions. A sustainable logistics strategy reduces environmental impact but can also attract environmentally conscious customers and enhance brand reputation. Frequently Asked Questions Ending Notes At KnoWerX, we ensure that our Demand Driven Leader Professional course equips professionals with the knowledge of integrating sustainable practices into logistics strategies. As a leader in Supply Chain Management training, we are dedicated to preparing you for the challenges of tomorrow’s logistics landscape while fostering sustainable and efficient practices. Join KnoWerX and stay ahead of the curve! Image Reference : Freepik Disclaimer: All trademarks, logos, and brand names are the property of their respective owners. All company, product, and service names used in this website are for identification purposes only. Use of these names, trademarks, and brands does not imply endorsement.
How Order and Material Delays Ruin Your Supply Chain!
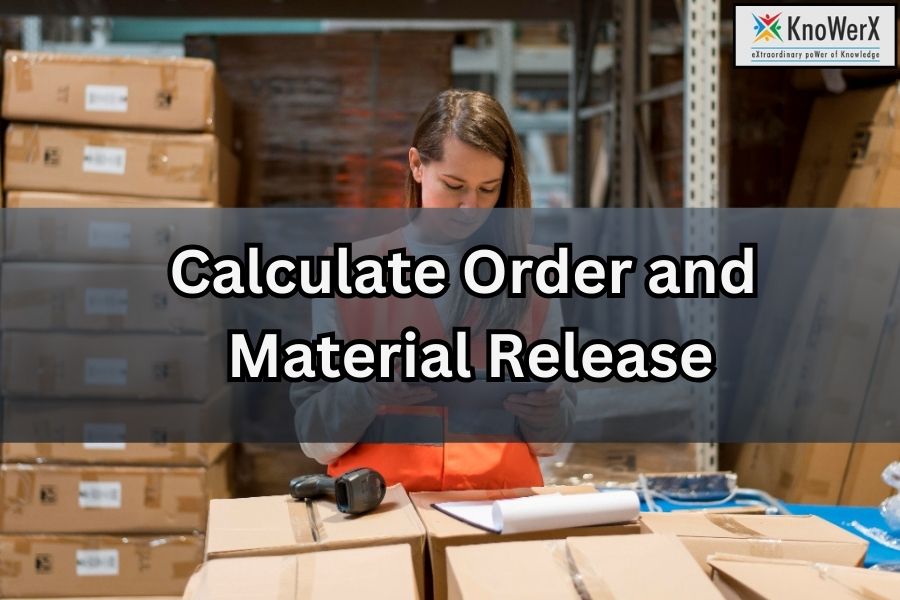
How Order and Material Delays Ruin Your Supply Chain! One of the most important processes directly affecting the efficiency and cost-effectiveness of the supply chain is the calculation of order and material release within the world of Supply Chain Management (SCM). This process helps avoid stockouts, reduce excess inventories, and maintain a seamless production flow by ordering materials at the right time. However, this assignment calls for an in-depth knowledge of demand forecasting, lead times, economic order quantities, and supplier cooperation. In this guide, KnoWerX provides tips on how to determine accurate order and material releases in order to enhance your SCM processes and increase operational success. Understand the process of demand forecasting The basis of order and material release calculation is accurate forecasting. Analyzing historical data and market trends, you can better predict future demand. Tools like moving averages, regression analysis, or machine learning algorithms will be used for better demand projections to ensure that the right amount of materials is always available at the right time. Lead Times Calculation Lead time is the total time between the order being placed and the material arriving. This is done by adding supplier lead time, production time, transportation delays, and any other factors that could affect the supply chain. Lead times need to be updated regularly based on the changes in supplier performance or external factors to maintain the accuracy of material release schedules. Apply Economic Order Quantity (EOQ) for Optimal Order Sizes The EOQ formula helps determine the most cost-effective quantity to order, balancing the ordering and holding costs. By calculating EOQ, businesses can avoid excess inventory while ensuring they meet demand efficiently. This method, when used alongside just-in-time (JIT) principles, can significantly enhance your material release strategy. Use Safety Stock to Mitigate Supply Chain Uncertainty Safety stock is an additional buffer of inventory designed to protect against unexpected demand spikes or supply delays. Calculating safety stock levels is done by considering demand variability and the reliability of your suppliers. It is crucial to regularly adjust your safety stock based on market conditions or internal process changes in order to maintain supply chain stability. Monitor and adjust order timing using reorder points Reorder points are the levels of stock at which new orders should be placed to avoid stockouts or overstocking. You can use real-time data to monitor inventory levels and set appropriate reorder points that align with fluctuations in demand. The adjustment of reorder points ensures that material release is optimally timed and thus avoids unnecessary costs or delays. Integrate Technology for Real-Time Monitoring SCM software and Enterprise Resource Planning (ERP) systems are great tools for the automation of the order and material release process, hence reducing the risk of human error. The technologies provide real-time data and analytics, hence allowing you to make decisions in your Supply Chain Management processes. Additionally, integrating IoT and RFID technologies helps in tracking materials and inventory in real time, hence ensuring timely material releases and enhanced visibility throughout the supply chain. Foster Supplier Collaboration for Timely Material Releases Create Efficient Material Releases by Engaging Supplier Collaboration Communication and collaboration with the supplier are crucial aspects of releasing orders in timely manner. This can be done through sharing forecasts, schedules, and order details with suppliers so that you are on the same page about the availability of material at production time. Ensuring a proper delivery schedule and performance metrics with the supplier would ensure an efficient release process without delays in order processing within the Supply Chain Management system. Frequently Asked Questions Closing Insights Mastery in the calculation of orders and material release goes to maintain an efficient supply chain with responsive management of material flows. Understanding Demand forecasting, Lead time computation, application of EOQ, use of safety stock and appropriate application of technology can give assurances to material delivery by desired times with cost cut-through. Training programs led by expert KnoWerX educate professionals with the techniques needed for optimalizing processes and therefore SCMs. Let’s help you take your Supply Chain Management skills to the next level! Image Reference: Freepik Disclaimer: All trademarks, logos, and brand names are the property of their respective owners. All company, product, and service names used in this website are for identification purposes only. Use of these names, trademarks, and brands does not imply endorsement.
Top 10 Benefits of Integrated Business Planning
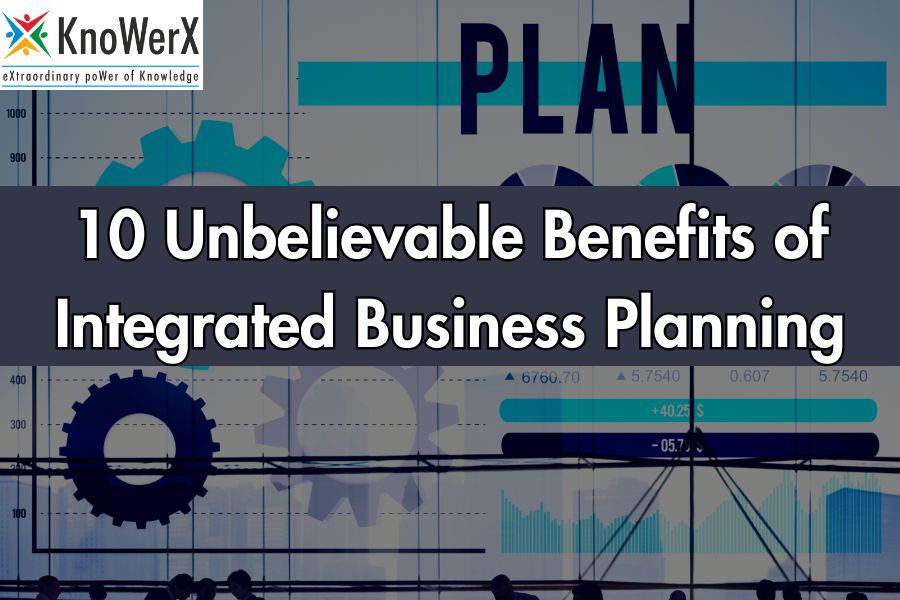
10 Unbelievable Benefits of Integrated Business Planning Integrated Business Planning (IBP) is a strategic approach that connects various business processes to ensure seamless communication and collaboration across departments. From enhancing efficiency to driving profitability, the benefits of Integrated Business Planning are transformative for any organization aiming for sustainable growth. In this article, we’ll explore the key benefits of Integrated Business Planning and how it can help businesses achieve their goals. Additionally, we’ll introduce KnoWerX, a leading institute offering supply chain courses, including the highly acclaimed CIBP (Certified Integrated Business Planning) program. What is Integrated Business Planning? Integrated Business Planning (IBP) is a sophisticated planning methodology that extends beyond the traditional Sales and Operations Planning (S&OP). While S&OP primarily focuses on balancing supply and demand, IBP takes a more holistic approach by integrating financial data, market insights, and strategic goals into the planning process. It provides businesses with a 360-degree view of their operations, enabling better decision-making and long-term growth. By combining data from sales, finance, marketing, supply chain, and operations, IBP ensures that all departments work collaboratively. This alignment allows organizations to operate efficiently, reduce redundancies, and capitalize on market opportunities. Why is Integrated Business Planning Important? Traditional business planning often suffers from fragmented processes and lack of coordination among departments. This can lead to inefficiencies, misaligned goals, and missed opportunities. Integrated Business Planning addresses these challenges by unifying all planning processes under a single framework. Key reasons why IBP is essential include: Cross-Departmental Visibility: It provides a single source of truth, allowing decision-makers to view the organization’s performance holistically. Improved Coordination: It ensures that all departments work in tandem toward shared objectives. Informed Decision-Making: By integrating real-time data, IBP enables businesses to make strategic and operational decisions with greater accuracy. Benefits of Integrated Business Planning The benefits of Integrated Business Planning span across every facet of a business. Let’s explore these advantages in detail: 1. Enhanced Cross-Functional Collaboration One of the most significant barriers to organizational success is the siloed nature of departments. IBP eliminates these silos, fostering collaboration between teams. Sales, marketing, finance, and supply chain teams share data and insights, ensuring alignment across the board. Collaboration leads to better resource allocation, improved problem-solving, and faster decision-making. This connected approach helps organizations achieve their goals more efficiently. 2. Accurate Forecasting and Planning Integrated Business Planning leverages advanced analytics and historical data to improve forecasting accuracy. By integrating information from various departments, businesses can predict demand, manage inventory, and plan production more effectively. Accurate forecasts reduce the risk of stockouts or overproduction, ensuring optimal resource utilization and customer satisfaction. 3. Financial and Operational Alignment Integrated Business Planning bridges the gap between financial and operational planning. It ensures that financial goals are directly linked to operational activities. For instance, budgets, revenue targets, and cost controls are aligned with production schedules, supply chain operations, and marketing campaigns. This alignment ensures that all resources are utilized effectively, maximizing profitability while minimizing waste. 4. Greater Agility and Flexibility In today’s rapidly changing market, businesses must be agile. IBP enables organizations to respond swiftly to changes in customer demand, supply chain disruptions, or market trends. This adaptability ensures that businesses remain competitive and resilient. For example, a sudden increase in demand can be addressed by quickly adjusting production schedules and reallocating resources, thanks to the visibility provided by IBP. 5. Enhanced Customer Satisfaction Meeting customer expectations is critical for business success. IBP helps businesses deliver products and services on time by improving demand planning and inventory management. This leads to higher customer satisfaction and loyalty. Satisfied customers are more likely to return and recommend your business to others, driving long-term growth. 6. Cost Optimization One of the most tangible benefits of Integrated Business Planning is cost reduction. By identifying inefficiencies and streamlining processes, IBP helps organizations minimize unnecessary expenses. Examples include: Reducing excess inventory. Lowering production costs through optimized schedules. Decreasing transportation expenses by aligning logistics with demand forecasts. 7. Data-Driven Decision-Making IBP consolidates data from various sources, providing a single platform for analysis. Decision-makers can access real-time insights, enabling them to make informed choices. Data-driven decisions are more accurate, reducing the risk of costly errors caused by assumptions or outdated information. 8. Risk Mitigation Market volatility, geopolitical instability, and supply chain disruptions pose significant risks to businesses. IBP helps organizations identify these risks early and develop contingency plans. For instance, if a supplier faces a delay, IBP can help businesses adjust procurement and production schedules to mitigate the impact. 9. Optimized Supply Chain Management Supply chain efficiency is critical for organizational success. IBP ensures that supply chain activities are aligned with overall business goals. From procurement to distribution, every aspect of the supply chain benefits from the visibility and coordination provided by Integrated Business Planning. This leads to reduced lead times, better vendor management, and improved overall performance. 10. Long-Term Strategic Growth While many planning methods focus on short-term goals, IBP emphasizes long-term growth. By aligning operational activities with the company’s strategic vision, it ensures that immediate objectives contribute to broader success. This holistic approach enables businesses to achieve sustainable growth while remaining competitive. The Role of Technology in Integrated Business Planning Technology plays a crucial role in the successful implementation of IBP. Advanced tools like Enterprise Resource Planning (ERP) systems, predictive analytics, and Artificial Intelligence (AI) enhance IBP processes. These technologies provide real-time data, automate repetitive tasks, and offer actionable insights. Businesses that invest in the right technology can unlock the full potential of IBP, achieving efficiency and accuracy at every level. KnoWerX: Mastering Integrated Business Planning For professionals looking to harness the benefits of Integrated Business Planning, specialized training is essential. KnoWerX, a leading supply chain management institute, offers the Certified Integrated Business Planning (CIBP) course designed to equip individuals with the knowledge and skills needed to implement IBP effectively. Why Choose KnoWerX? Expert Faculty: Learn from industry veterans with decades of experience in supply chain and business planning. Comprehensive Curriculum: The CIBP course covers all aspects of IBP, from
Supply Chain Management in 2025: Avoid These Buffer Errors
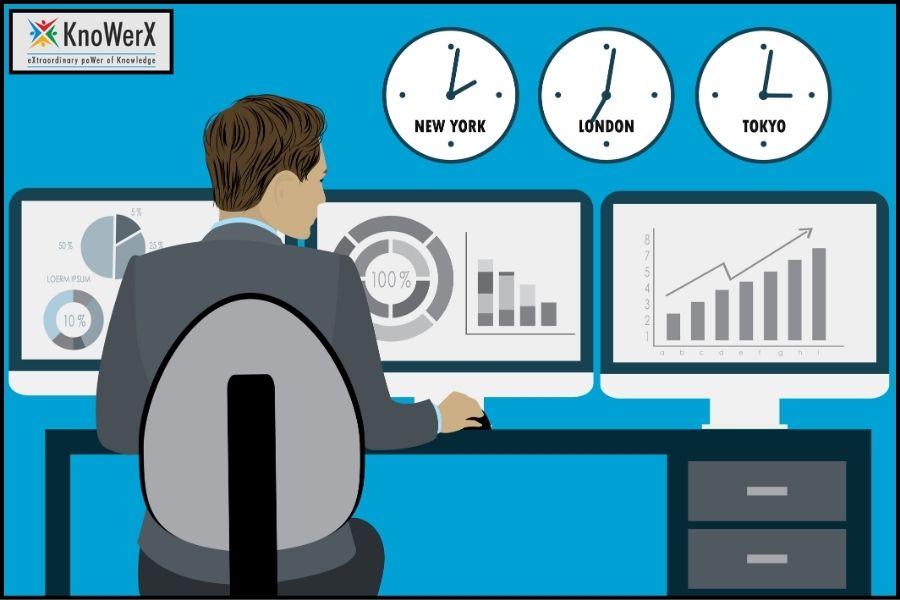
Monitoring Time Buffers in Supply Chain Management: Best Practices In supply chain management, time buffers play a critical role in mitigating uncertainties and ensuring smooth operations. A time buffer is the extra time strategically added to critical processes to account for potential delays caused by disruptions, inefficiencies, or fluctuating demand. By acting as a safeguard against unpredictability, time buffers help maintain service levels and optimize lead times across the supply chain. This requires monitoring and adjustment so the buffers are effective, especially during uncertain times. A poorly designed buffer may lead to situations like excessive inventory buildup or even higher costs associated with this move because the delivery target cannot be reached within that period. Monitoring the effectiveness of the buffers, therefore, acts as an essential practice since through them, businesses would gain adequate balance between resilience and efficiency to remain competitive. Time Buffers in Mitigating Supply Chain Risks Definition: Time buffers are extra time allocated to critical processes in the supply chain to handle uncertainties and disruptions. These act as safeguards to ensure operations remain uninterrupted despite unforeseen delays. Importance: Highlights their significance in mitigating risks, managing uncertainties, and maintaining smooth supply chain operations. Without time buffers, supply chains are vulnerable to cascading delays that can disrupt production and deliveries. Overview of Monitoring Benefits: Briefly states how monitoring time buffers improves overall efficiency and reliability by identifying and addressing inefficiencies. Consistent monitoring helps optimise resource utilisation and reduce wastage caused by over- or underestimation. The Role of Time Buffers in Supply Chain Management Definition and Purpose: Explains what time buffers are: a planned allocation of extra time within various supply chain processes to account for potential delays or disruptions. This ensures that operations can adapt to unexpected events without compromising deadlines. By acting as a contingency measure, time buffers allow supply chains to absorb shocks and maintain a steady flow of goods and services to meet customer demands. Applications: Describes specific areas where time buffers are implemented: Production schedules: To account for machine downtimes, production defects, or resource shortages, ensuring manufacturing timelines are met. Transportation and logistics: To absorb delays caused by traffic, customs checks, weather conditions, or unforeseen accidents during transit. Inventory management: To manage stock availability despite demand fluctuations, supply chain disruptions, or late deliveries from suppliers. These applications help maintain service levels while reducing the risk of order cancellations or customer dissatisfaction. Benefits: Reducing delays: Time buffers act as a safety net against unexpected disruptions, ensuring minimal impact on end-to-end supply chain performance. Flexibility: Helps manage unpredictable demand or supply shifts effectively, ensuring companies can adapt to dynamic market conditions without sacrificing operational efficiency. This combination of reduced delays and increased flexibility is critical in building a resilient and reliable supply chain. Monitoring Time Buffers: Importance and Best Practices Why Monitor Time Buffers? Avoids the pitfalls of excessive inventory (wasted resources) or prolonged delays (customer dissatisfaction). Unmonitored buffers can either inflate costs or fail to address disruptions effectively. Ensures optimised lead times and operational efficiency. Regular monitoring identifies whether allocated buffers are sufficient or need adjustments to current conditions. Helps identify bottlenecks or inefficiencies that affect overall supply chain performance. Proactive detection of inefficiencies can prevent small issues from becoming major operational challenges. Techniques for Monitoring: Highlights tools and methods for effective monitoring: Supply chain software: Enables real-time tracking and automation, providing instant visibility across the supply chain network. Predictive analytics: Provides insights into potential delays and allows proactive adjustments. Advanced algorithms help forecast disruptions and recommend suitable buffer modifications. Periodic reviews: Ensures time buffers are still appropriate for current operational needs. Regular audits can adapt buffer times to changes in supply chain dynamics, such as seasonality or market shifts. These techniques help businesses stay agile and maintain optimal efficiency levels despite uncertainties. Key Metrics to Track: Identifies measurable indicators for monitoring: Lead time variability: Ensures consistency in process timelines by identifying deviations from expected lead times across the supply chain. Cycle time deviations: Tracks deviations from expected production or delivery timelines, ensuring that processes stay within acceptable thresholds. Service level compliance: Measures adherence to customer service goals, such as on-time delivery and product availability. This ensures buffers align with customer expectations and service commitments. Challenges in Monitoring Time Buffers Data Collection and Analysis: Monitoring requires accurate, real-time data, which may be difficult to obtain or interpret. Complex supply chains often rely on multiple data sources, increasing the chances of inaccuracies or inconsistencies. Inconsistent data can lead to poorly informed decisions regarding buffer sizes, causing inefficiencies or disruptions in supply chain operations. Balancing Buffer Sizes: Setting buffer times that are too large leads to inefficiencies, while too small increases risks of disruptions. Striking the right balance is a constant challenge, especially in fast-changing industries. Companies must weigh the cost of maintaining large buffers against the risk of insufficient buffers causing delays or lost sales. External Disruptions: Highlights challenges like global crises, natural disasters, or geopolitical events that can render time buffers insufficient or obsolete. These events are difficult to predict and may overwhelm even the best-planned buffers. Organisations must remain prepared to revise buffer strategies during such extraordinary circumstances to maintain supply chain stability. Solutions to Enhance Buffer Monitoring Advanced Technologies: Using AI (Artificial Intelligence) and IoT (Internet of Things) for predictive insights and real-time monitoring. These technologies enable companies to anticipate disruptions and adjust buffers dynamically. Automated systems reduce manual errors and provide actionable insights, improving decision-making accuracy and response times. Supply Chain Visibility Platforms: Encourages integration of systems that provide a holistic view of the supply chain for better decision-making. Enhanced visibility enables early detection of potential risks and opportunities for optimisation. Visibility platforms facilitate better communication among stakeholders, ensuring faster resolution of issues and improved buffer management. Collaboration with Partners: Suggests maintaining real-time communication and updates with suppliers and logistics partners to reduce uncertainties and improve buffer effectiveness. Collaborative efforts, such as sharing demand forecasts and shipment updates, help align buffer strategies across the supply chain. Frequently Asked Questions Closing Insights Time
Explore Best Rewarding Career in Supply Chain Management
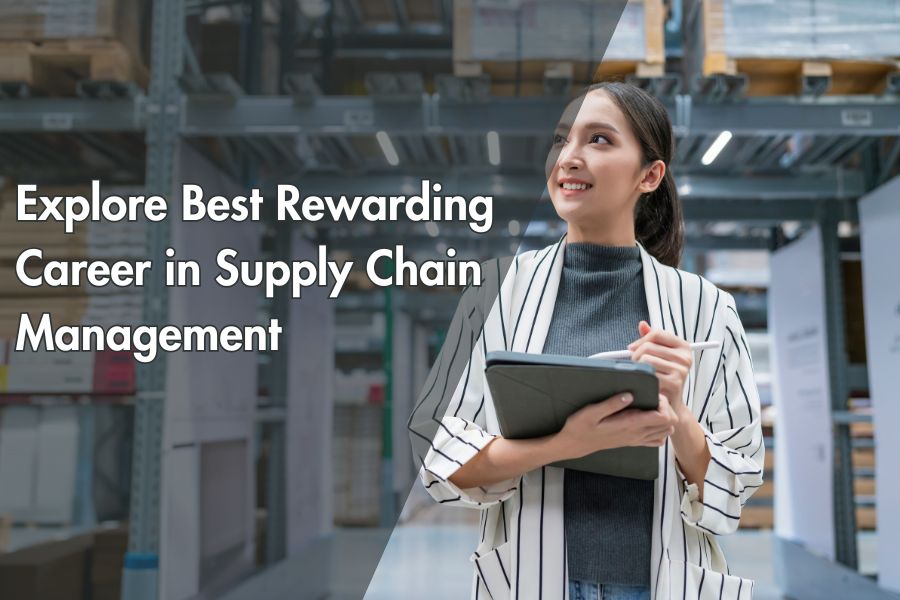
Explore a Rewarding Career in Supply Chain Management Supply chain management is an essential function that drives the efficiency and profitability of any business. It encompasses the planning, execution, and optimization of the movement of goods, services, and information across a company’s supply chain. From sourcing raw materials to delivering finished products to customers, supply chain management ensures that operations run smoothly and efficiently. As the global economy becomes more interconnected, the demand for skilled supply chain professionals continues to grow. If you’re seeking a career that combines strategic thinking, problem-solving, and innovation, a career in supply chain management could be the perfect fit. Let’s delve into the roles, salaries, and career pathways within this dynamic field. Why Pursue a Career in Supply Chain Management? A career in supply chain management offers a wealth of opportunities, including: High demand across industries: Every sector, from e-commerce and manufacturing to healthcare and retail, requires supply chain professionals to manage their operations. Competitive salaries: As you gain experience, your earning potential grows significantly, making this field financially rewarding. Diverse roles: From logistics to inventory control and procurement, there are multiple career paths to explore. Global exposure: Supply chain professionals often work with international vendors and clients, offering the chance to build a global career. Dynamic work environment: The role involves tackling challenges, optimizing processes, and leveraging technology to drive efficiency. Key Roles in Supply Chain Management and Their Salaries Supply Chain Manager Supply chain managers oversee end-to-end supply chain operations, ensuring seamless coordination between procurement, production, and delivery. They play a vital role in cost control and customer satisfaction. Average Salary: ₹3 to ₹30 lakhs per annum (with experience). Logistics Manager Logistics managers focus on the efficient movement of goods, managing transportation, warehousing, and distribution. Their work ensures timely and cost-effective deliveries. Average Salary: ₹2.5 to ₹20 lakhs per annum (with experience). Procurement Manager Procurement managers are responsible for sourcing materials, negotiating supplier contracts, and maintaining cost and quality standards. Average Salary: ₹4 to ₹27 lakhs per annum (with experience). Demand Planning Analyst Demand planning analysts predict consumer demand using data analytics and market trends, helping businesses maintain optimal inventory levels. Average Salary: ₹3 to ₹22 lakhs per annum (with experience). Supply Chain Consultant Consultants offer strategic guidance to improve supply chain processes, implement new technologies, and achieve cost efficiencies. Average Salary: ₹3 to ₹25 lakhs per annum (with experience). Operations Manager Operations managers oversee the daily operations of supply chain processes, ensuring productivity and efficiency. Average Salary: ₹3 to ₹20 lakhs per annum (with experience). Inventory Control Manager This role involves maintaining the right inventory levels, tracking stock movement, and preventing overstock or stockouts. Average Salary: ₹2 to ₹12 lakhs per annum (with experience). Warehouse Operations Manager Warehouse operations managers supervise warehouse staff, optimize storage, and ensure timely dispatch of goods. Average Salary: ₹3 to ₹17 lakhs per annum (with experience). Skills Required for Success in Supply Chain Management To excel in supply chain management, you need to develop a combination of technical and soft skills, including: Analytical thinking: To analyze data and optimize processes. Effective communication: For clear collaboration with internal teams and external vendors. Problem-solving abilities: To address supply chain disruptions efficiently. Technological proficiency: Familiarity with tools like SAP, Oracle, and other supply chain management software. Time management: To ensure that deadlines are met without compromising quality. Adaptability: To respond to market changes and evolving business needs. Educational Requirements and Certifications While a bachelor’s degree in supply chain management, logistics, or business administration is typically required, certifications can further boost your credentials and career prospects. Recommended Certifications: APICS Certified Supply Chain Professional (CSCP) APICS Certified in Planning and Inventory Management (CPIM) Six Sigma Certification Certified Integrated Business Planning (CIBP) These certifications validate your expertise and enhance your ability to secure high-paying roles in the industry. Industries That Rely on Supply Chain Professionals Supply chain management is integral to various industries, including: E-commerce: Managing large-scale distribution networks. Manufacturing: Overseeing production cycles and raw material sourcing. Healthcare: Ensuring the timely availability of essential medical supplies. Retail: Streamlining inventory and logistics operations. Future Trends in Supply Chain Management The field of supply chain management is evolving with advancements in technology. Trends like artificial intelligence, End Notes A career in supply chain management is a gateway to exciting opportunities, lucrative salaries, and global exposure. Whether you’re passionate about logistics, procurement, or demand planning, this field offers a diverse range of roles to explore. Start your journey with the right education and certifications to unlock your potential. Join KnoWerX and take the first step toward building a successful career in supply chain management. Image Reference: Freepik Disclaimer: All trademarks, logos, and brand names are the property of their respective owners. All company, product, and service names used in this website are for identification purposes only. Use of these names, trademarks, and brands does not imply endorsement.
Why Warehouse Management System Essential for Logistics Firm
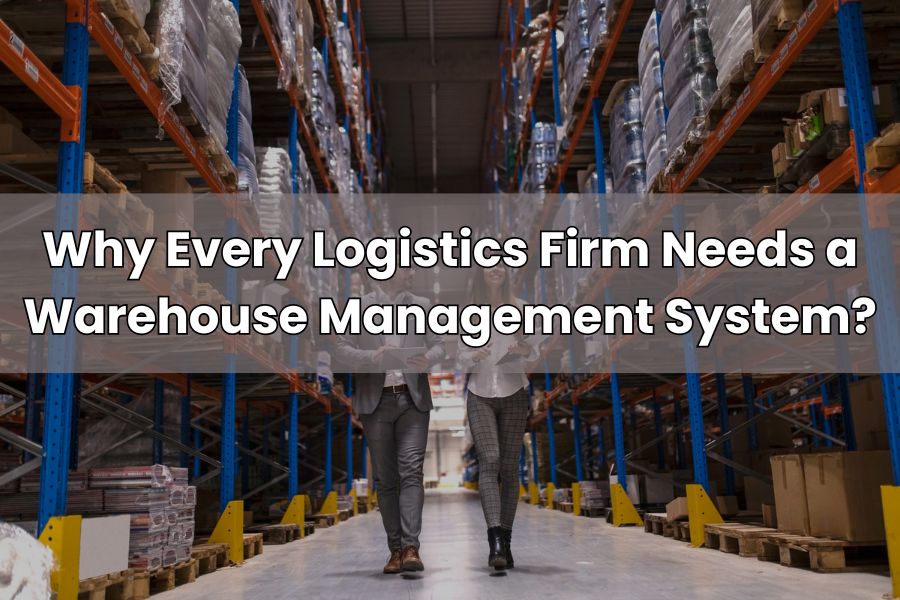
Why Every Logistics Firm Needs a Warehouse Management System? In today’s fast-paced world, logistics companies face numerous challenges in managing their operations efficiently. One of the key components of an effective logistics operation is warehouse management. A Warehouse Management System (WMS) plays a crucial role in streamlining operations, improving efficiency, and ensuring smooth business flow. But why is a Warehouse Management System in logistics essential for firm? Let’s explore the reasons. What is a Warehouse Management System (WMS)? A Warehouse Management System is software that helps manage the day-to-day operations of a warehouse. It ensures that goods are stored, tracked, and moved efficiently, and it integrates with other systems within the logistics supply chain. A WMS helps companies manage inventory, control warehouse operations, and improve overall productivity. Why Do Logistics Firms Need a Warehouse Management System? Improved Inventory Control Managing inventory manually can lead to errors, resulting in lost or misplaced goods. A Warehouse Management System in logistics allows for real-time tracking of inventory, ensuring that stock levels are accurate. This helps logistics companies avoid stockouts or overstocking, both of which can negatively impact their operations. Increased Efficiency A WMS automates many manual tasks, such as tracking products, assigning tasks, and processing orders. This automation leads to faster and more accurate order fulfillment. As a result, logistics firms can deliver goods to their customers more quickly, improving customer satisfaction. Better Space Utilization Warehouse space is often limited, and inefficient use of that space can result in lost productivity. A Warehouse Management System in logistics helps optimize warehouse layout and storage systems. By using advanced algorithms, it ensures that goods are stored in the most efficient way possible, which maximizes space utilization. Enhanced Accuracy and Reduced Errors Manual processes are prone to human error, which can be costly for logistics companies. With a WMS, logistics firms can reduce errors related to order picking, packing, and shipping. The system automatically updates inventory levels and provides real-time information on product availability, leading to more accurate operations. Streamlined Order Fulfillment A key advantage of a Warehouse Management System in logistics is its ability to streamline the entire order fulfillment process. From receiving orders to shipping them out, a WMS helps logistics firms ensure that products are delivered on time and in good condition. It also helps in managing returns and exchanges efficiently, reducing delays and costs. Data-Driven Decision Making A Warehouse Management System in logistics collects valuable data, such as inventory levels, order history, and shipping performance. This data can be analysed to make informed decisions about inventory management, procurement, and overall supply chain strategy. It helps logistics firms improve their forecasting and planning capabilities. Cost Reduction By improving efficiency, reducing errors, and optimizing space, a Warehouse Management System in logistics helps logistics firms lower their operational costs. With better inventory management, fewer resources are wasted, and the overall process becomes more cost-effective. This, in turn, allows companies to pass on the savings to customers or invest in other areas of the business. How Does a Warehouse Management System Improve Customer Satisfaction? The faster and more accurately logistics firms can fulfil orders, the more satisfied their customers will be. With a Warehouse Management System, firms can ensure timely deliveries, reduce errors in shipments, and offer real-time tracking information. All of these factors contribute to higher customer satisfaction and repeat business. FAQs: Frequently Asked Questions End Notes Warehouse Management System in logistics industry is no longer a luxury; it’s a necessity. It streamlines operations, enhances accuracy, and helps logistics firms stay competitive in an increasingly fast-paced market. By implementing a WMS, companies can achieve better inventory control, increase efficiency, optimize space, and reduce costs, all of which directly impact their bottom line. For logistics professionals looking to learn more about optimizing warehouse operations and other aspects of supply chain management, KnoWerX offers a range of courses. As a leading supply chain management institute, KnoWerX helps individuals and businesses develop the skills and knowledge needed to succeed in the ever-evolving logistics industry Image Reference: Freepik Disclaimer: All trademarks, logos, and brand names are the property of their respective owners. All company, product, and service names used in this website are for identification purposes only. Use of these names, trademarks, and brands does not imply endorsement.
Developing & Managing Organizational Strategy in SCM
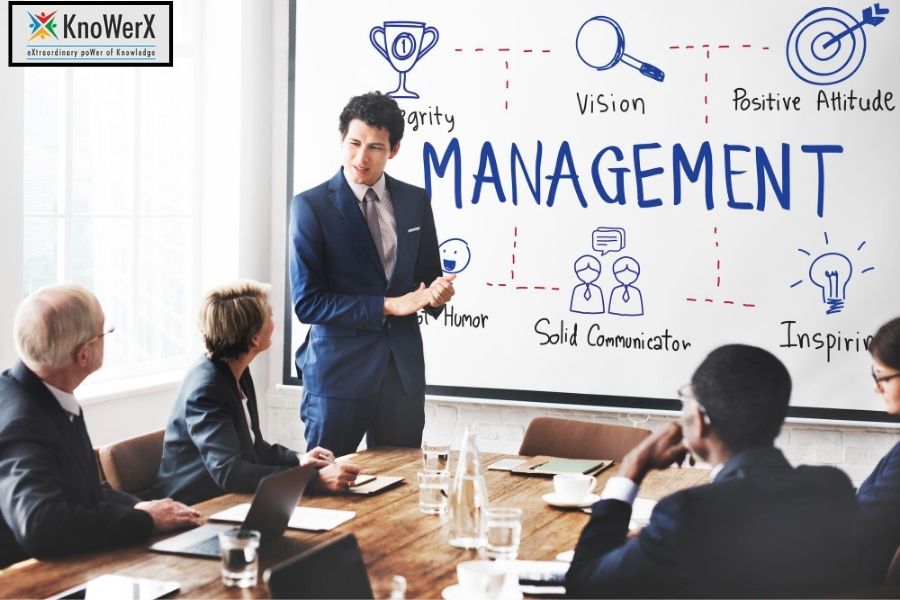
Developing & Managing Organizational Strategy in Supply Chain Management In today’s competitive business environment, it is essential for companies to develop and manage a well-designed organizational strategy in Supply Chain Management (SCM) to be successful. Optimized strategy can increase efficiency, reduce costs, and improve overall operational performance. KnoWerX offers complete Supply Chain Management training, which equips professionals with the knowledge and skills to manage and implement robust strategies. Here are some key tips to help you develop and manage a successful organizational strategy in supply chain management. Align SCM with Business Objectives A successful Supply Chain Management strategy must align with your organization’s overall business goals. When developing your SCM strategy, consider the company’s mission, vision, and financial objectives. A strategy that complements these elements will be more effective in achieving sustainable growth. Collaborate with different departments within your organization to ensure that the Supply Chain Management strategy supports key business functions, such as marketing, finance, and operations. Data and Analytics to Enable Decision Making Data plays a crucial role in decision making in Supply Chain Management. Leverage tools that provide real-time visibility and analytics across your supply chain operations. Big data and predictive analytics help you identify trends, demand forecasting, and inventory management, which in turn helps optimize resources, improve delivery times, and reduce costs. KnoWerX’s Supply Chain Management training programs are focusing on the importance of data analytics and how professionals can use such information for strategic decision-making. Implement Agile Practices An effective Supply Chain Management strategy should be responsive to changing market conditions. Agile practices can help your organization respond rapidly to unexpected disruptions or shifts in demand. This flexibility is essential in a global supply chain environment, where factors like geopolitical events or natural disasters can affect supply chain performance. Encourage continuous improvement and ensure that your SCM processes can quickly adjust to market fluctuations, thereby minimizing risks and maximizing efficiency. Collaborate with Suppliers and Partners A good supply chain management strategy requires an effective partnership with suppliers and partners. The mutual benefit will lie in shared objectives of faster lead times, reducing cost, and improving the quality of the product. Communicate regularly and collaborate with the supplier to identify potential bottlenecks or risks before they become major issues. The essence of supplier relationship management has been taught in KnoWerX as part of its Supply Chain Management curriculum, thus putting the tools in the professional’s hands to build partnerships. Sustainability Sustainability is becoming more significant in Supply Chain Management. Companies that focus on the best sustainable practices in their supply chain do not only reduce their environmental impacts but can also enhance their brand and meet governmental regulation requirements. Implement sustainable sourcing practices, minimize waste, and consider environmental factors when choosing transportation and packaging. KnoWerX includes sustainability concepts in Supply Chain Management training so professionals are ready to meet the challenges of the modern supply chain. Invest in Technology and Automation Technology and automation are changing the landscape of Supply Chain Management. Investments in technologies like AI, robotics, and IoT can streamline the operation process, reduce human errors, and increase efficiency. Automating inventory management, order fulfillment, and transportation will make your supply chain responsive and cost-effective. KnoWerX helps professionals have a good understanding of implementing and using state-of-the-art technology in Supply Chain Management. Set Well Defined KPIs While measuring the success of a supply chain management strategy will entail well-defined and measurable key performance indicators, the whole supply chain can be seen in terms of inventory turn rates, order accuracy, or delivery lead times. Therefore, through the regular monitoring of KPIs, certain areas can be identified for improvement with time. KnoWerX stresses on developing and monitoring KPI in its training programs, which enables the professional to assess and enhance the Supply Chain Management strategies of the organization. Risk Management Improvement Supply chains are susceptible to several risks, such as supplier failure, transportation disruptions, and economic instability. Manage these risks by developing a full-fledged risk management approach that involves contingency plans, diversification of suppliers, and insurance coverage. An effective risk management approach ensures that your Supply Chain Management strategy remains resilient in the face of unforeseen challenges. Encourage Continuous Improvement As it is the world of supply chain management, its dynamic nature makes it vital to be constantly improving. Promote employee, supplier, and customer feedback to see if there are areas of opportunity where your SCM strategy may improve. Evaluate the operations for ways to streamline the flow of activity to reduce waste and improve the satisfaction of customers. KnoWerX’s training programs enhance the culture of continuous improvement and learning in order for professionals to stay ahead of the game with their Supply Chain Management strategies. Frequently Asked Questions Closing Insights Supply Chain Management strategy: an effective organizational strategy, is managed by aligning it with business goals, making decisions based on the data, keeping an emphasis on sustainability, technology, as well as risk management. At KnoWerX, we provide the world’s leading Supply Chain Management training programs to arm you with knowledge and tools required for success in today’s competitive environment. Our programs help ensure that you can formulate strategies to optimize your supply chain for both short-term success and long-term growth. To learn more about professional Supply Chain Management training programs at KnoWerX, take that next step towards career advancement by visiting us! Image Reference: Freepik Disclaimer: All trademarks, logos, and brand names are the property of their respective owners. All company, product, and service names used in this website are for identification purposes only. Use of these names, trademarks, and brands does not imply endorsement.
Discover 7 Types of Demand Forecasting You Must Know
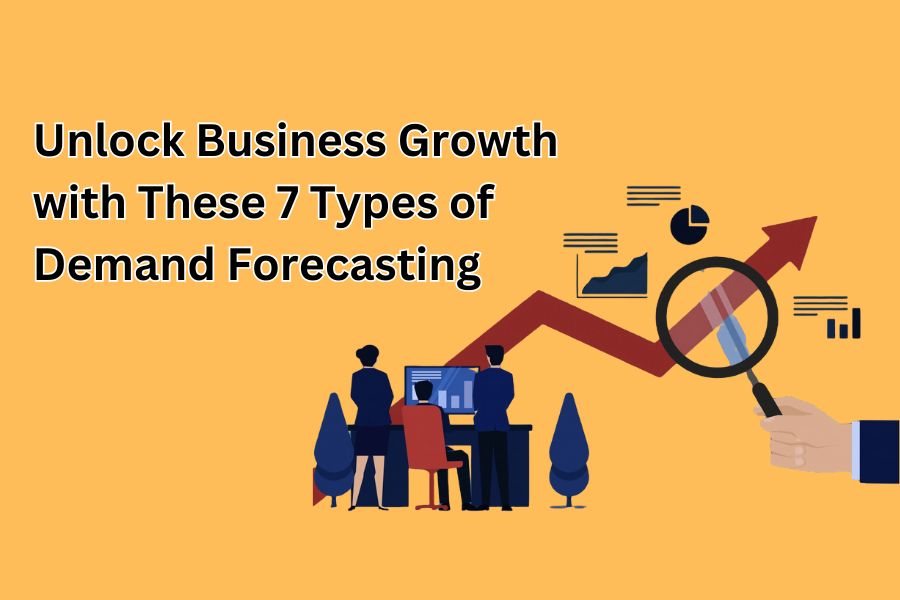
Unlock Business Growth with These 7 Types of Demand Forecasting Demand forecasting is an essential component of supply chain management. It involves predicting future customer demand based on historical data and market trends. Accurate demand forecasting allows businesses to ensure they have the right amount of inventory, minimize costs, and meet customer expectations. In this article, we will explore the different types of demand forecasting that businesses use to stay ahead in the competitive market. 1. Passive Demand Forecasting Passive demand forecasting is a technique that primarily relies on past sales data to predict future demand. This approach assumes that future demand will follow the same patterns as past sales trends, without accounting for external changes in the market. Why to Use: Passive demand forecasting is useful for businesses with a stable market where demand follows a consistent pattern over time. Tools Used: Simple statistical methods, like moving averages, are used to predict demand based on historical data. Examples: This method is commonly applied in industries where demand is predictable, such as staple products and basic consumer goods. 2. Active Demand Forecasting Active demand forecasting goes beyond historical data by considering external factors that may impact demand, such as changes in market conditions, consumer behaviour, and competitor actions. This approach is used to predict future demand by actively analysing external variables that might affect the market. Why to Use: Active demand forecasting is ideal for businesses operating in rapidly changing markets or those introducing new products. Tools Used: Active demand forecasting uses advanced analytics, market research, and trend analysis to predict demand more accurately. Examples: Companies in industries like technology, fashion, and automotive often use active demand forecasting to stay ahead of market shifts and changing consumer preferences. 3. Short-Term Demand Forecasting Short-term demand forecasting focuses on predicting demand for a brief period, such as days, weeks, or months. This type of demand forecasting is especially useful for managing inventory, workforce, and other operational activities that need to respond quickly to changing customer demands. Why to Use: Short-term demand forecasting is crucial for businesses that deal with seasonal demand fluctuations or industries with frequent sales cycles. Tools Used: Real-time data, point-of-sale (POS) systems, and customer feedback are essential tools for short-term demand forecasting. Examples: Retailers often rely on short-term demand forecasting to optimize their stock levels for holiday seasons or special promotions. 4. Long-Term Demand Forecasting Long-term demand forecasting looks at demand over an extended period, usually several months to years. This type of demand forecasting is necessary for businesses that need to make strategic decisions about long-term investments, capacity planning, and workforce allocation. Why to Use: Long-term demand forecasting is essential for businesses that plan for large-scale production or for industries where product development cycles are long. Tools Used: Time-series analysis, econometric modelling, and market research surveys are commonly used for long-term demand forecasting. Examples: Manufacturing companies, especially in the automotive and aerospace industries, rely on long-term forecasting to ensure they are prepared for future demand spikes. 5. Quantitative Demand Forecasting Quantitative demand forecasting uses historical data and numerical analysis to predict future demand. By applying statistical techniques, this method provides highly reliable and data-driven insights into future sales. Why to Use: Quantitative forecasting is ideal for businesses with a wealth of historical data to analyse, making it one of the most accurate type of demand forecasting methods. Tools Used: Tools like regression analysis, time-series forecasting, and machine learning algorithms help identify patterns and forecast future demand. Examples: Large-scale companies in retail, manufacturing, and logistics often use quantitative demand forecasting to improve efficiency and reduce waste. 6. Qualitative Demand Forecasting Qualitative demand forecasting is based on subjective judgment rather than historical data. It is used when there is limited or no historical data available, especially in cases involving new products or untested markets. This approach relies on the insights and opinions of experts, market research, and focus groups. Why to Use: Qualitative forecasting is particularly useful when a business is introducing a new product, entering an unfamiliar market, or facing uncertain conditions. Tools Used: Techniques like the Delphi method, expert panels, and focus groups are often used for qualitative forecasting. Examples: Startups and companies launching innovative products often rely on qualitative forecasting methods to understand potential market demand. 7. Mixed Demand Forecasting Mixed demand forecasting combines both quantitative and qualitative approaches to give a more well-rounded forecast. This method is beneficial when there is a need to incorporate both data-driven insights and expert opinions to enhance the accuracy of the forecast. Why to Use: Mixed demand forecasting is an ideal type of demand forecasting for businesses operating in complex or unpredictable markets where a combination of data and expertise is required for more accurate predictions. Tools Used: Data analytics tools combined with expert consultations help businesses use both hard data and insights from market experts to forecast demand. Examples: Businesses in industries such as pharmaceuticals and consumer electronics often rely on mixed forecasting methods to address both statistical data and expert insights. FAQs: Frequently Asked Questions End Notes Understanding the various types of demand forecasting and applying the right technique can significantly improve a business’s efficiency, inventory management, and overall strategic planning. By choosing the right forecasting method, businesses can make data-driven decisions that enhance customer satisfaction and reduce costs. At KnoWerX, we recognize the importance of mastering demand forecasting as part of a successful supply chain strategy. Our Certified Forecasting Demand Management (CFDM) courses are designed to equip professionals with the skills and tools needed to navigate the complexities of demand forecasting. Whether you’re looking to refine your quantitative analysis skills or learn how to incorporate qualitative insights into your forecasting processes, KnoWerX offers the expertise and resources to help you succeed. Join us and take the first step toward a rewarding career in supply chain management! Image Reference: Freepik Disclaimer: All trademarks, logos, and brand names are the property of their respective owners. All company, product, and service names used in this website are for identification
Tips for Conducting an Effective Crisis Simulation Exercise
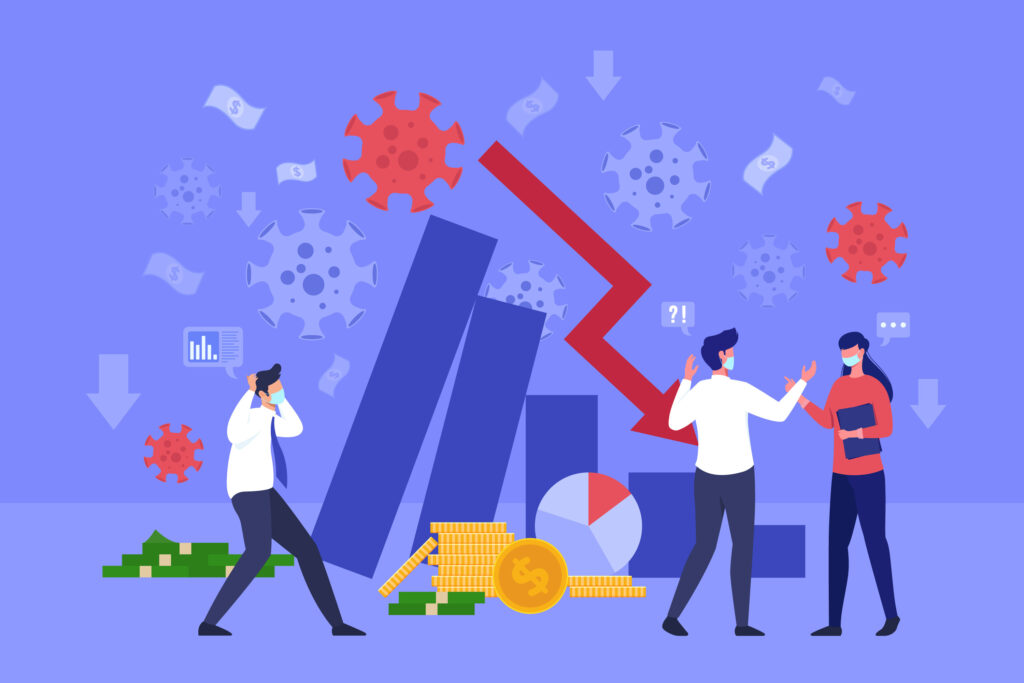
Tips for Conducting an Effective Crisis Simulation Exercise Organizations need to be ready for any kind of crisis that may arise in today’s fast-paced and unpredictable world. Crisis Simulation Exercises are one of the most effective ways of preparing teams for such situations. Such exercises simulate real-world crisis scenarios, enabling teams to practice their response in a controlled yet dynamic environment. They emulate actual crisis conditions, thereby providing invaluable experience and enhancing decision-making, communication, and teamwork skills. Crisis preparedness cannot be overemphasized; it plays an even greater role in some sectors, particularly the supply chain. KnoWerX delivers Crisis Simulation Exercise training designed to equip experts with the techniques and best practices to master difficult situations in the wake of any crisis situation, whether relating to critical decision-making timelines, media-related interactions, or inter-departmental relations. Emulate Real-Life Scenarios The key to a good Crisis Simulation Exercise is in the fact that the scenarios developed are as realistic as they can be. The simulators must emulate actual crisis situations, so that there would be the pressures and challenges of a real situation to face. This scenario creates an environment where critical thinking and swift action must occur. Integrate Time Jumps During a Crisis Simulation Exercise, use time jumps to create a feeling of urgency. Teams will need to adapt to new, evolving challenges as the crisis unfolds just like in real life. These time jumps can simulate a progressive crisis that requires quick thinking and strategic responses. Use Multimedia Injects A dynamic Crisis Simulation Exercise benefits from diverse situation inputs delivered through multimedia injects. These inputs—such as news updates, emergency communications, or social media reactions—help create a more dynamic and unpredictable environment. Teams must respond to these rapidly changing situations, refining their crisis management skills. Strategic Approach A robust strategic approach is the beginning of a crisis response. In a Crisis Simulation Exercise, direct your teams to develop a crisis response strategy at the outset. This will give a structured framework to the crisis, thereby ensuring a coordinated and focused response to every situation that arises. Role-Specific Responses A key element of a Crisis Simulation Exercise is assigning unique roles to participants. Each role player responds to specific, role-tailored scenarios, which provides a more authentic experience. This approach tests the effectiveness of each team member’s decision-making skills, fostering a deeper understanding of their responsibilities during a crisis. Test Team Collaboration Crisis roles are a great way to evaluate the teamwork that happens in times of crisis. A Crisis Simulation Exercise is only as good as the teamwork it inspires. Encourage team members to work together, communicate effectively, and support each other’s efforts. The success of the crisis response often depends on how well the team functions as a unit. Develop Crisis Communication Strategies Clear and concise communication is crucial in a crisis. Prepare participants with crisis communication drafts and media strategies in a Crisis Simulation Exercise. With predefined communication frameworks, teams can control the narrative and ensure that their message is clear and effective during the crisis. Use Live Chat for Remote Collaboration In today’s interconnected world, live chats are a very valuable tool for teams working remotely on a crisis. Live chats in your Crisis Simulation Exercise enable members working from different locations to work together in real time. All teams will be on the same page and informed of everything that is happening in this exercise, simulating a real global crisis response. Frequently Asked Question Closing Insights Preparation for real-world challenges is what KnoWerX understands. Through our Crisis Simulation Exercise trainings, we equip a person and an organization to deal with any crisis effectively. As pioneers in industry-leading Supply Chain Management, our expert-lead program is designed specifically for helping you gain all the latest best practices and domain expertise along with acquiring the desired relevant certifications, enhancing you professionally. With a combined experience of over 32 years, KnoWerX aims to deliver high-quality education and training programs that cater to your needs. Image Reference: Freepik Disclaimer: All trademarks, logos, and brand names are the property of their respective owners. All company, product, and service names used in this website are for identification purposes only. Use of these names, trademarks, and brands does not imply endorsement.
Top10 KnoWerX Rise to Power as Asia’s Premier ASCM Partner
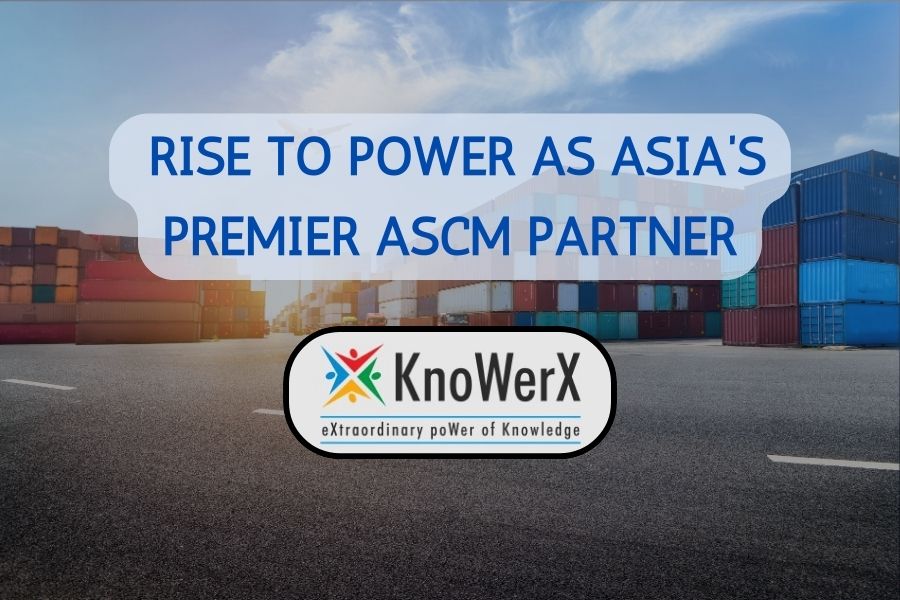
Inside Top 10 KnoWerX’s Rise to Power as Asia’s Premier Association Of Supply Chain Management (ASCM) Partner 1. Passion for Excellence in Education It takes pride in its education commitment that is on international standards, which includes choosing highly experienced faculty, updating curricula on a regular basis, and best practices in training. KnoWerX focuses on high standards, making sure that all students and clients gain actionable knowledge effectively leading to value addition in their careers and businesses. 2. Strong emphasis on Association Of Supply Chain Management (ASCM) Aligned Certifications Association Of Supply Chain Management(ASCM) certifications, which include CPIM, CSCP, and CLTD among others, are recognized at the global level in the management of supply chain and logistics. KnoWerX is dedicated to these certifications, which allow participants to acquire credentials that make them more efficient and employable professionals. This emphasis on Association Of Supply Chain Management(ASCM) has made KnoWerX a leader in Asia in upskilling the workforce in the supply chain industry. 3. Customized Corporate Trainings KnoWerX’s training approach is not on an assembly line basis, for each organization is considered different, and so is created with a customized program built upon specific business objectives to enhance their business performance through certain areas of improvement toward corporations in optimizing supply chain capabilities and competitiveness within various industries. 4. Implementation of Advanced Digital Tools and Technologies With digitization taking over the supply chain industry, KnoWerX employs the latest tools and technologies for its delivery of training. From virtual classrooms to simulations and interactive learning modules, KnoWerX has embraced the new digital wave by making it more accessible and effective in the training of professionals in Asia. 5. Strong Network and Industry Connections KnoWerX has a strong network of supply chain across which it connects the participants with the leaders and mentors. This network provides a window into the valuable insights about industry trends and opportunities. These connections keep KnoWerX informed about the evolving needs so that training given will stay relevant, forward-looking, and at par with growth 6. Distinguished Faculty with Practical Experience KnoWerX has practical experience with professional faculty in diverse areas of the supply chain industry. This broad-based industry experience enables instructors to not only give more than textbook information but also to provide real-world and practical examples of what happens outside the textbook. This ensures that participants are equipped with applicable knowledge that prepares them to tackle real challenges in the supply chain sector. 7. Emphasis on Continuous Learning and Development KnoWerX fosters a learning culture where professionals update their skills and knowledge continuously. KnoWerX brings professionals up to date through its events like webinars, workshops, and advanced courses on supply chain management. This approach of continuous development ensures the up-to-date nature of professionals in the field that is changing rapidly. 8 Strong Emphasis on Global Standards and Best Practices KnoWerX always ensures that the curricula are at par with international standards and best practices. KnoWerX ensures that the trainings conducted are also based on international benchmarks. This has enabled the courses offered by KnoWerX to be worth the cost for professionals looking to venture out into multinational companies or expand their reach into the global arena. Global best practices make KnoWerX’s trainees ready to face diverse work environments. 9. Focus on Case Studies and Real-World Application KnoWerX provides real-life case studies and applications in the training programs so that the trainees can grasp how theory applies in practice. The case studies help participants to learn how major companies operate their supply chains and see, visualize, and absorb proven strategies. This hands-on approach enhances learning and makes KnoWerX’s training programs unique and impactful. 10. Reputation for Consistent Excellence KnoWerX has, over the years, established a track record for consistency and excellence in its training and service offerings, thus being guided by a quality commit that is customer satisfaction and industry relevance. This record thus saw KnoWerX become one of the trusted Association Of Supply Chain Management (ASCM) partners in Asia, attracting high talent and fostering long-term client relationships. Frequently Asked Question Ending Notes Focus on these aspects has not only made KnoWerX Asia’s leading Association Of Supply Chain Management (ASCM) partner but also a trusted guide for supply chain professionals wishing to grow and do well. Sustainability of quality, customized solutions, and industry alignment have made KnoWerX consistently lead the way in training managers across Asia for supply chain management. Image Reference: Freepik Disclaimer: All trademarks, logos, and brand names are the property of their respective owners. All company, product, and service names used in this website are for identification purposes only. Use of these names, trademarks, and brands does not imply endorsement.