Top 10 Benefits of Integrated Business Planning
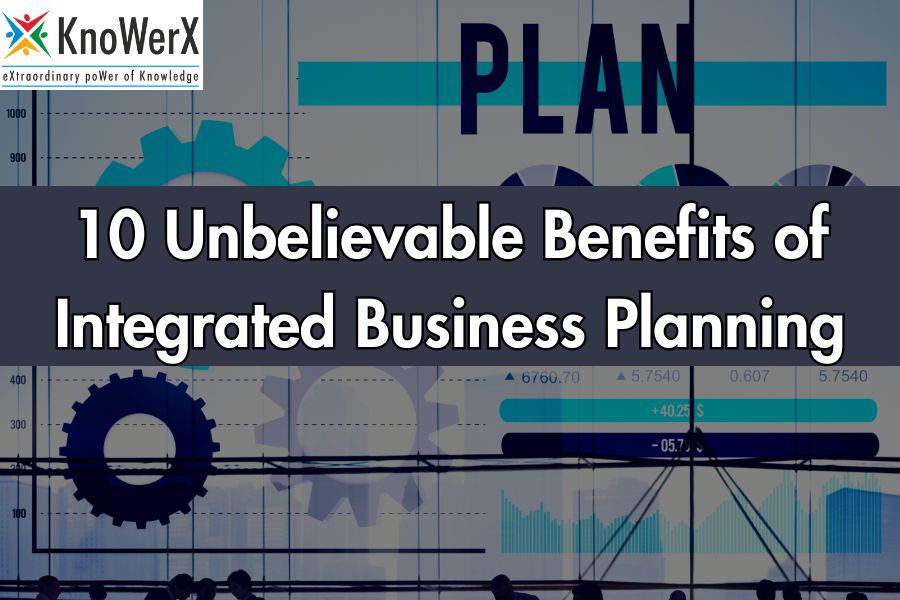
10 Unbelievable Benefits of Integrated Business Planning Integrated Business Planning (IBP) is a strategic approach that connects various business processes to ensure seamless communication and collaboration across departments. From enhancing efficiency to driving profitability, the benefits of Integrated Business Planning are transformative for any organization aiming for sustainable growth. In this article, we’ll explore the key benefits of Integrated Business Planning and how it can help businesses achieve their goals. Additionally, we’ll introduce KnoWerX, a leading institute offering supply chain courses, including the highly acclaimed CIBP (Certified Integrated Business Planning) program. What is Integrated Business Planning? Integrated Business Planning (IBP) is a sophisticated planning methodology that extends beyond the traditional Sales and Operations Planning (S&OP). While S&OP primarily focuses on balancing supply and demand, IBP takes a more holistic approach by integrating financial data, market insights, and strategic goals into the planning process. It provides businesses with a 360-degree view of their operations, enabling better decision-making and long-term growth. By combining data from sales, finance, marketing, supply chain, and operations, IBP ensures that all departments work collaboratively. This alignment allows organizations to operate efficiently, reduce redundancies, and capitalize on market opportunities. Why is Integrated Business Planning Important? Traditional business planning often suffers from fragmented processes and lack of coordination among departments. This can lead to inefficiencies, misaligned goals, and missed opportunities. Integrated Business Planning addresses these challenges by unifying all planning processes under a single framework. Key reasons why IBP is essential include: Cross-Departmental Visibility: It provides a single source of truth, allowing decision-makers to view the organization’s performance holistically. Improved Coordination: It ensures that all departments work in tandem toward shared objectives. Informed Decision-Making: By integrating real-time data, IBP enables businesses to make strategic and operational decisions with greater accuracy. Benefits of Integrated Business Planning The benefits of Integrated Business Planning span across every facet of a business. Let’s explore these advantages in detail: 1. Enhanced Cross-Functional Collaboration One of the most significant barriers to organizational success is the siloed nature of departments. IBP eliminates these silos, fostering collaboration between teams. Sales, marketing, finance, and supply chain teams share data and insights, ensuring alignment across the board. Collaboration leads to better resource allocation, improved problem-solving, and faster decision-making. This connected approach helps organizations achieve their goals more efficiently. 2. Accurate Forecasting and Planning Integrated Business Planning leverages advanced analytics and historical data to improve forecasting accuracy. By integrating information from various departments, businesses can predict demand, manage inventory, and plan production more effectively. Accurate forecasts reduce the risk of stockouts or overproduction, ensuring optimal resource utilization and customer satisfaction. 3. Financial and Operational Alignment Integrated Business Planning bridges the gap between financial and operational planning. It ensures that financial goals are directly linked to operational activities. For instance, budgets, revenue targets, and cost controls are aligned with production schedules, supply chain operations, and marketing campaigns. This alignment ensures that all resources are utilized effectively, maximizing profitability while minimizing waste. 4. Greater Agility and Flexibility In today’s rapidly changing market, businesses must be agile. IBP enables organizations to respond swiftly to changes in customer demand, supply chain disruptions, or market trends. This adaptability ensures that businesses remain competitive and resilient. For example, a sudden increase in demand can be addressed by quickly adjusting production schedules and reallocating resources, thanks to the visibility provided by IBP. 5. Enhanced Customer Satisfaction Meeting customer expectations is critical for business success. IBP helps businesses deliver products and services on time by improving demand planning and inventory management. This leads to higher customer satisfaction and loyalty. Satisfied customers are more likely to return and recommend your business to others, driving long-term growth. 6. Cost Optimization One of the most tangible benefits of Integrated Business Planning is cost reduction. By identifying inefficiencies and streamlining processes, IBP helps organizations minimize unnecessary expenses. Examples include: Reducing excess inventory. Lowering production costs through optimized schedules. Decreasing transportation expenses by aligning logistics with demand forecasts. 7. Data-Driven Decision-Making IBP consolidates data from various sources, providing a single platform for analysis. Decision-makers can access real-time insights, enabling them to make informed choices. Data-driven decisions are more accurate, reducing the risk of costly errors caused by assumptions or outdated information. 8. Risk Mitigation Market volatility, geopolitical instability, and supply chain disruptions pose significant risks to businesses. IBP helps organizations identify these risks early and develop contingency plans. For instance, if a supplier faces a delay, IBP can help businesses adjust procurement and production schedules to mitigate the impact. 9. Optimized Supply Chain Management Supply chain efficiency is critical for organizational success. IBP ensures that supply chain activities are aligned with overall business goals. From procurement to distribution, every aspect of the supply chain benefits from the visibility and coordination provided by Integrated Business Planning. This leads to reduced lead times, better vendor management, and improved overall performance. 10. Long-Term Strategic Growth While many planning methods focus on short-term goals, IBP emphasizes long-term growth. By aligning operational activities with the company’s strategic vision, it ensures that immediate objectives contribute to broader success. This holistic approach enables businesses to achieve sustainable growth while remaining competitive. The Role of Technology in Integrated Business Planning Technology plays a crucial role in the successful implementation of IBP. Advanced tools like Enterprise Resource Planning (ERP) systems, predictive analytics, and Artificial Intelligence (AI) enhance IBP processes. These technologies provide real-time data, automate repetitive tasks, and offer actionable insights. Businesses that invest in the right technology can unlock the full potential of IBP, achieving efficiency and accuracy at every level. KnoWerX: Mastering Integrated Business Planning For professionals looking to harness the benefits of Integrated Business Planning, specialized training is essential. KnoWerX, a leading supply chain management institute, offers the Certified Integrated Business Planning (CIBP) course designed to equip individuals with the knowledge and skills needed to implement IBP effectively. Why Choose KnoWerX? Expert Faculty: Learn from industry veterans with decades of experience in supply chain and business planning. Comprehensive Curriculum: The CIBP course covers all aspects of IBP, from
Key Insights from Demand and Forecasting Analysis You Need
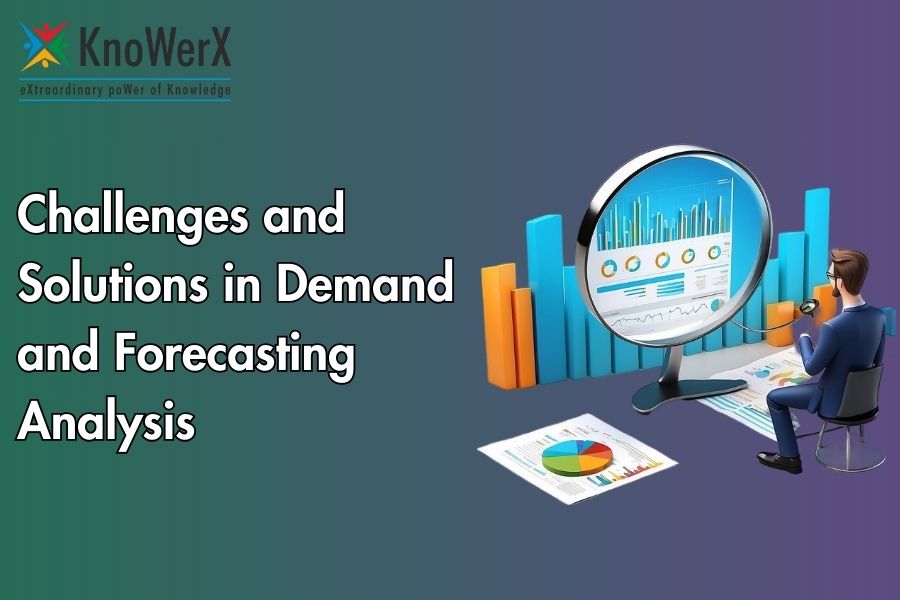
Addressing Key Challenges and Solutions in Demand and Forecasting Analysis Demand and forecasting analysis plays a crucial role in modern supply chain management, helping businesses anticipate customer needs, optimize inventory levels, and enhance overall operational efficiency. Accurate demand forecasts are essential for making informed decisions that directly impact profitability and customer satisfaction. However, the process of demand and forecasting analysis is fraught with challenges, ranging from data quality issues to adapting to market volatility. This article delves into the common challenges associated with demand and forecasting analysis and explores effective solutions, future trends, and the importance of education and training in this critical area. Understanding Demand and Forecasting Analysis Demand and forecasting analysis involves predicting future customer demand for products or services based on historical data, market trends, and other relevant factors. This analysis is vital for businesses to align their production, inventory, and supply chain strategies with anticipated demand. Various methods, such as qualitative techniques (e.g., expert opinion) and quantitative techniques (e.g., time series analysis), are used in demand forecasting to estimate future demand accurately. The significance of demand and forecasting analysis cannot be overstated, as it directly influences business decision-making. Effective demand forecasting enables companies to avoid stockouts, minimize excess inventory, reduce costs, and improve customer satisfaction. However, achieving accuracy in demand forecasting is a complex task that requires addressing several challenges inherent in the process. Challenges in Demand and Forecasting Analysis Data Quality Issues: Data quality is a fundamental aspect of demand and forecasting analysis. Inaccurate or incomplete data can lead to inaccurate forecasts, resulting in insignificant decisions. Businesses often struggle with collecting reliable historical data, especially in industries with rapidly changing consumer preferences or where data is fragmented across different sources. Poor data quality can distort demand predictions, leading to overproduction or stockouts, both of which are disastrous to business operations. Volatility and Market Changes: The dynamic nature of markets presents a significant challenge in demand and forecasting analysis. Sudden shifts in market conditions, economic fluctuations, and unpredictable demand patterns can render traditional forecasting models ineffective. For example, unexpected events like a global pandemic can drastically alter consumer behaviour, making it difficult for businesses to forecast demand accurately. Adapting to such volatility requires a flexible approach to demand forecasting that can quickly respond to changes in real-time. Complexity in Demand Patterns: Demand patterns are often influenced by various factors, including seasonality, trends, and cyclical behaviour. Identifying and interpreting these patterns is crucial for accurate demand forecasting. However, the complexity of demand patterns can pose challenges, especially in industries where multiple factors interact simultaneously. Businesses must navigate the intricacies of seasonal variations, long-term trends, and short-term fluctuations to generate reliable forecasts. Technological and Analytical Challenges: The integration of advanced forecasting tools and technologies is essential for enhancing the accuracy of demand forecasts. However, many businesses face challenges in adopting these technologies due to limitations in analytical capabilities and resources. Implementing sophisticated forecasting models, such as those based on machine learning and AI, requires a deep understanding of the underlying algorithms and access to vast amounts of data. Additionally, small and medium-sized enterprises may struggle with the costs and expertise required to deploy advanced forecasting tools effectively. Solutions to Overcome Challenges Improving Data Quality: To address data quality issues in demand and forecasting analysis, businesses should prioritize the collection of accurate and comprehensive data. Implementing robust data cleansing and validation processes can help eliminate errors and inconsistencies in the data. Additionally, businesses can invest in data management systems that consolidate information from various sources, ensuring that forecasting models are built on reliable data. By enhancing data quality, companies can significantly improve the accuracy of their demand forecasts. Adapting to Market Volatility: In an environment characterized by market volatility, businesses must adopt flexible and adaptive forecasting models. Scenario planning, which involves creating multiple demand forecasts based on different potential market conditions, can help businesses prepare for uncertainty. Real-time data integration is also critical for responding to sudden market changes. By continuously monitoring market trends and adjusting forecasts accordingly, businesses can stay agile and better align their operations with actual demand. Enhancing Analytical Tools: The use of advanced analytical methods, such as machine learning and AI, can greatly improve the accuracy of demand forecasts. These technologies can analyse vast datasets, identify patterns, and generate more precise predictions. Businesses should consider investing in big data and predictive analytics tools that allow for deeper insights into customer behaviour and demand trends. Additionally, cloud-based forecasting solutions can provide scalability and flexibility, enabling businesses to leverage cutting-edge technologies without the need for extensive infrastructure. Collaboration and Cross-functional Teams: Effective demand and forecasting analysis often require collaboration across different departments within an organization. Cross-functional teams, composed of members from sales, marketing, finance, and supply chain, can provide diverse perspectives that enhance the accuracy of demand forecasts. By involving various departments in the forecasting process, businesses can ensure that all relevant factors are considered, leading to more comprehensive and reliable forecasts. Future Trends in Demand and Forecasting Analysis Integration of AI and Machine Learning: As AI and machine learning technologies continue to advance, their integration into demand and forecasting analysis is expected to become more widespread. These technologies can automate the forecasting process, enabling businesses to generate accurate predictions with minimal human intervention. Future developments may include self-learning forecasting systems that continuously improve their accuracy by analysing new data and adapting to changing market conditions. Emphasis on Real-time Data: The importance of real-time data in demand and forecasting analysis is growing, driven by the increasing availability of IoT and smart technologies. Real-time data allows businesses to monitor demand patterns as they occur, enabling them to make swift adjustments to their forecasts. In the future, real-time data integration will likely become a standard practice, providing businesses with the ability to respond to market changes in near real-time. Sustainability and Green Supply Chain Forecasting: As sustainability becomes a priority for businesses, demand and forecasting analysis will need to incorporate considerations related to environmental impact. Forecasting for sustainable
Exploring the Various Types of Supply Chain Risks
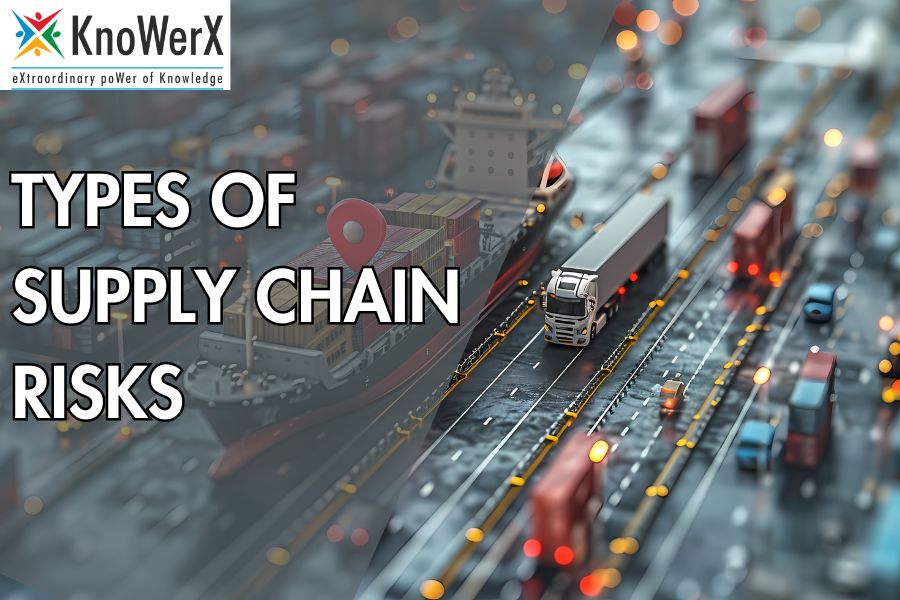
Types of Supply Chain Risks and Effective Mitigation Strategies | KnoWerX In today’s globalized business environment, supply chains are more complex and interconnected than ever before. Managing these supply chains effectively is crucial for business success, and understanding the types of supply chain risks is a fundamental part of this process. Supply chain risks can disrupt operations, increase costs, and damage a company’s reputation. Therefore, identifying and mitigating these risks is essential for maintaining a smooth and resilient supply chain. Operational Risks Operational risks are among the most common types of supply chain risks. These risks arise from day-to-day operations and can significantly impact the efficiency and effectiveness of a supply chain. Definition and Examples of Operational Risks Operational risks include any disruptions in the processes that move products from suppliers to customers. Examples include equipment failures, supply shortages, transportation delays, and quality control issues. For instance, if a key supplier experiences a machinery breakdown, it can halt production and delay deliveries, impacting the entire supply chain. Causes of Operational Risks The causes of operational risks are diverse. They can originate from internal challenges such as poor equipment maintenance, or external factors like labour strikes at supplier locations. Additionally, natural disasters and accidents can trigger these types of supply chain risks, resulting in unforeseen delays and interruptions. Strategies to Mitigate Operational Risks Mitigating operational risks requires proactive planning and robust strategies. Companies should implement contingency plans to address potential disruptions. This includes having backup suppliers, maintaining safety stock, and using real-time monitoring systems to track supply chain activities. Diversifying suppliers and sourcing from multiple regions can also help reduce the impact of local disruptions. Financial Risks Financial risks are another critical type of supply chain risk that can affect a company’s profitability and stability. Definition and Examples of Financial Risks Among the types of supply chain risks, financial risks specifically relate to economic factors that can destabilize a supply chain’s financial foundation. Common examples include currency fluctuations, interest rate variations, cost overruns, and supplier bankruptcies. For instance, a sudden currency devaluation can escalate the cost of imported goods, thereby squeezing profit margins. Causes of Financial Risks Several factors can cause financial risks. These include volatile currency markets, fluctuating commodity prices, and changes in trade policies. Economic downturns and financial instability in supplier regions can also pose significant financial risks. Strategies to Mitigate Financial Risks To mitigate financial risks, companies can employ strategies such as hedging against currency fluctuations and locking in prices with long-term contracts. Regular financial monitoring and analysis can help identify potential risks early. Building strong relationships with financial institutions and diversifying investment portfolios can also provide a buffer against financial uncertainties. Strategic Risks Strategic risks are types of supply chain risks that arise from changes in the business environment and strategic decisions. Definition and Examples of Strategic Risks Strategic risks include any factors that can alter the competitive landscape or affect long-term business goals. Examples are market changes, new regulations, and shifts in consumer preferences. For instance, a new regulatory policy might require changes in product formulations, affecting the entire supply chain. Causes of Strategic Risks The causes of strategic risks are often external and beyond a company’s control. These include geopolitical developments, technological advancements, and changing market dynamics. Strategic decisions, such as entering new markets or launching new products, can also introduce risks. Strategies to Mitigate Strategic Risks Mitigating strategic risks involves thorough market research and continuous monitoring of the business environment. Companies should stay informed about regulatory changes and industry trends. Developing flexible business strategies and maintaining agility in operations can help adapt to changes quickly. Engaging in scenario planning and stress testing can also prepare companies for potential strategic risks. Environmental Risks Environmental risks are types of supply chain risks that arise from environmental factors and natural events. Definition and Examples of Environmental Risks Environmental risks encompass any natural or environmental factors that can disrupt supply chains. Examples include natural disasters like earthquakes, floods, hurricanes, and climate change impacts. For instance, a hurricane can damage infrastructure and halt transportation, severely affecting supply chain operations. Causes of Environmental Risks Environmental risks are typically caused by natural events and changes in environmental conditions. Climate change is increasing the frequency and severity of extreme weather events, posing significant risks to supply chains. Environmental regulations and sustainability pressures also contribute to these risks. Strategies to Mitigate Environmental Risks To mitigate environmental risks, companies should adopt sustainability practices and build resilience into their supply chains. This includes conducting environmental impact assessments, investing in disaster recovery plans, and diversifying supply chain routes to avoid high-risk areas. Collaborating with suppliers to enhance their environmental resilience is also crucial. Technological Risks Technological risks are types of supply chain risks associated with technology and information systems. Definition and Examples of Technological Risks Technological risks involve threats related to the use of technology in supply chains. Examples include cybersecurity threats, technology failures, and data breaches. For instance, a cyber-attack on a supplier’s system can compromise sensitive information and disrupt supply chain operations. Causes of Technological Risks Technological risks can arise from various sources, including outdated systems, inadequate cybersecurity measures, and rapid technological changes. Human errors and insufficient training on new technologies can also lead to technological risks. Strategies to Mitigate Technological Risks Mitigating technological risks requires robust cybersecurity measures and regular system updates. Companies should invest in secure IT infrastructure and conduct regular security audits. Implementing comprehensive training programs for employees and establishing protocols for technology management can also reduce the risk of technological disruptions. Geopolitical Risks Geopolitical risks are types of supply chain risks that arise from political instability, conflicts, and government actions. Definition and Examples of Geopolitical Risks Geopolitical risks involve disruptions caused by political events or changes in government policies. Examples include trade wars, embargoes, sanctions, and political instability in supplier countries. For instance, a trade war between two countries can lead to increased tariffs, affecting the cost and availability of goods. Causes of Geopolitical Risks The causes of geopolitical
Strategic Risk Management in Global Supply Chains
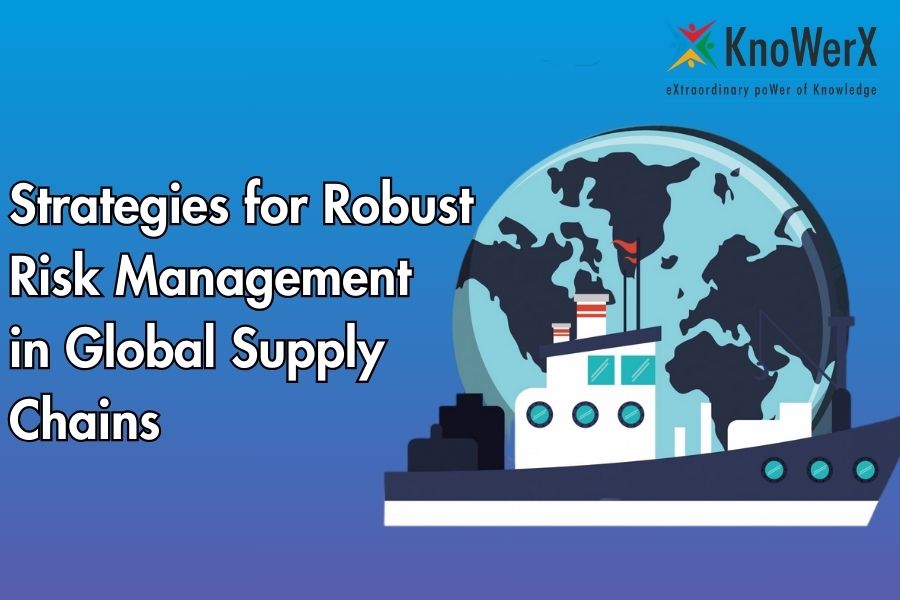
Strategies for Robust Risk Management in Global Supply Chains At KnoWerX, we recognize that in today’s interconnected global economy, businesses rely heavily on complex international networks to source materials, manufacture products, and deliver goods to customers worldwide. These intricate systems, however, are susceptible to a wide array of threats that can disrupt operations, impact financial performance, and damage reputations. Therefore, risk management in global supply chains has become a critical competency for organizations seeking to maintain resilience and continuity amid uncertainty. Risk management in global supply chains refers to the systematic process of identifying, assessing, and mitigating potential threats to supply chain operations. The significance of robust risk management strategies cannot be overstated, as they enable companies to proactively address challenges, minimize disruptions, and maintain a competitive edge in an increasingly volatile business environment. The challenges facing global supply chains are numerous and diverse, ranging from natural disasters and geopolitical tensions to cybersecurity threats and regulatory changes. Developing comprehensive risk management strategies is essential for organizations to successfully navigate the complexities of international trade and logistics. At KnoWerX, we equip supply chain professionals with the knowledge and skills needed to develop and implement these crucial strategies, ensuring their organizations can thrive even in the face of global uncertainties Types of Risks in Global Supply Chains To effectively implement risk management in global supply chains, it’s crucial to understand the various types of threats that can impact operations: Operational risks: These include disruptions to day-to-day activities such as transportation delays, quality control issues, and equipment failures. Effective risk management in global supply chains must address these common but potentially costly disruptions. Financial risks: Currency fluctuations, changes in commodity prices, and supplier bankruptcies fall under this category. Risk management in global supply chains should include strategies to mitigate financial exposure. Geopolitical risks: Trade disputes, sanctions, and political instability can significantly impact supply chain operations across borders. A robust approach to risk management in global supply chains must account for these complex international factors. Environmental risks: Natural disasters, climate change impacts, and resource scarcity pose increasing threats to global supply chains. Incorporating environmental considerations into risk management strategies for global supply chains is becoming increasingly important. Technological risks: Cybersecurity breaches, system failures, and obsolescence of technology can disrupt supply chain operations and compromise sensitive data. As supply chains become more digitized, addressing technological risks is a critical component of risk management in global supply chains. Risk Identification and Assessment Effective risk management in global supply chains begins with thorough identification and assessment of potential threats: Risk mapping techniques: Visual tools like heat maps and bow-tie diagrams help organizations identify and prioritize risks across their supply chains. These techniques are essential for comprehensive risk management in global supply chains. Quantitative and qualitative risk analysis: Combining data-driven assessments with expert judgments provides a comprehensive view of risk exposure. This balanced approach is key to effective risk management in global supply chains. Key risk indicators (KRIs): Establishing and monitoring KRIs enables early detection of emerging threats and trends. KRIs are a crucial tool for proactive risk management in global supply chains. Scenario planning and stress testing: These techniques help organizations prepare for various potential outcomes and assess their resilience to different risk scenarios. They are invaluable for developing robust risk management strategies in global supply chains. Risk Mitigation Strategies Once risks are identified and assessed, organizations can implement various strategies to mitigate them. Effective risk management in global supply chains often involves a combination of the following approaches: Diversification of suppliers and markets: Reducing dependence on single sources or regions can enhance supply chain resilience. This strategy is a fundamental aspect of risk management in global supply chains. Building flexibility and redundancy: Developing alternative supply routes, production facilities, and logistics options provides backup plans in case of disruptions. Flexibility is a key principle of effective risk management in global supply chains. Implementing robust inventory management: Balancing stock levels to buffer against shortages while avoiding excess inventory costs is crucial for risk management in global supply chains. Developing contingency plans: Creating detailed response plans for various risk scenarios ensures rapid and effective action when disruptions occur. Contingency planning is an essential component of risk management in global supply chains. Leveraging technology for risk monitoring: Advanced analytics, artificial intelligence, and IoT devices can provide real-time insights into supply chain risks and enable proactive management. Technology plays an increasingly important role in risk management for global supply chains. Supply Chain Visibility and Transparency Enhancing visibility across the entire supply chain is crucial for effective risk management in global supply chains: Importance of end-to-end visibility: Clear insight into all supply chain stages allows for better risk identification and faster response to disruptions. Improving visibility is a key objective of risk management in global supply chains. Technologies for enhancing transparency: Blockchain and IoT devices can provide secure, real-time tracking of goods and information throughout the supply chain. These technologies are revolutionizing risk management approaches in global supply chains. Data analytics for risk prediction and management: Advanced analytics tools can process vast amounts of data to identify patterns, predict potential risks, and suggest mitigation strategies. Data-driven decision-making is becoming central to risk management in global supply chains. Collaborative Risk Management Effective risk management in global supply chains often requires cooperation across the entire network: Strengthening supplier relationships: Building trust and open communication with suppliers can lead to better risk sharing and joint problem-solving. Strong relationships are a cornerstone of successful risk management in global supply chains. Information sharing across the supply chain: Transparent exchange of risk-related information can improve overall supply chain resilience. Information sharing is crucial for comprehensive risk management in global supply chains. Joint risk mitigation efforts with partners: Collaborating on risk management initiatives can lead to more comprehensive and effective strategies. Partnership is increasingly important in risk management for global supply chains. Regulatory Compliance and Risk Management Navigating the complex landscape of international regulations is a crucial aspect of risk management in global supply chains: Understanding global
Supply Chain Management Courses India
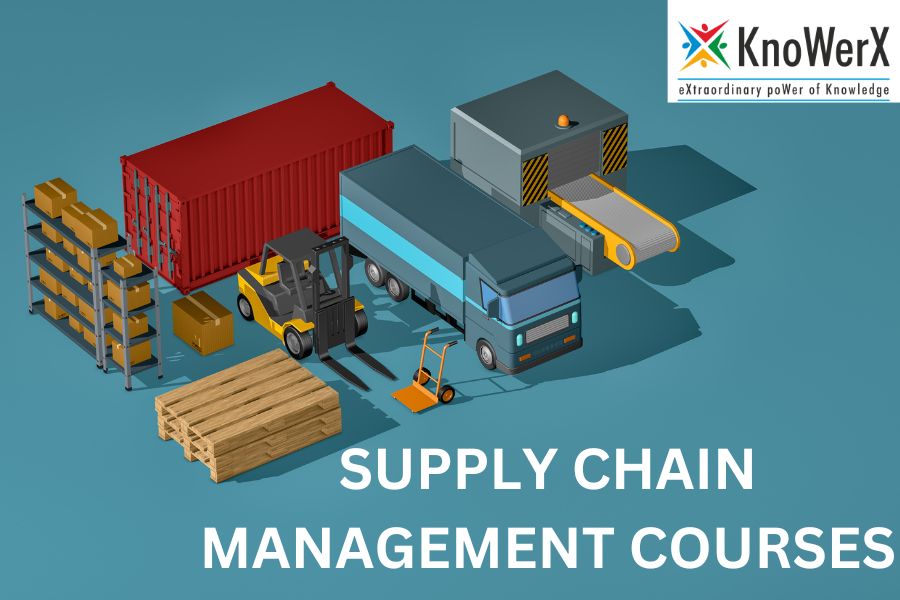
Navigating Supply Chain Management Courses in India: Opportunities, Careers, and Costs Over the past few years, businesses in India have seen big changes. This shift has been driven by things like companies going global, new technology, and what people want to buy. One big part of this change is Supply Chain Management (SCM). SCM is all about making sure things get from where they start, like raw materials, to where they’re needed, like the end customer. In this article, we’ll talk about why SCM is so important for businesses in India and look at the many courses available to help people learn the skills they need to work in this fast-changing field. These courses are known as Supply Chain Management Courses. What Is Supply Chain Management Course? Understanding Supply Chain Management Courses Supply Chain Management Courses cover a wide range of topics aimed at helping us understand, improve, and oversee the connected activities involved in getting products and services to customers. These courses typically cover areas like buying, shipping, keeping track of inventory, predicting demand, managing relationships with suppliers, and integrating sustainable practices into the supply chain. In India, there are many options for studying Supply Chain Management Courses. These courses are available at universities, colleges, specialized training centers, and online platforms. They cater to people at different points in their careers, whether they’re just starting out, already working, or executives looking to boost their skills in Supply Chain Management. Why Supply Chain Management Education Matters In today’s fiercely competitive business world, having a strong grasp of Supply Chain Management is crucial for companies to stay ahead, improve how they operate, and meet customer needs. As businesses work to make their supply chains more efficient, flexible, and resilient, there’s a growing need for professionals who have the specialized knowledge and skills in Supply Chain Management. Types Of Supply Chain Certifications Overview of Different Certifications: Certificate Programs: These are short-term courses designed to give you basic knowledge in Supply Chain Management (SCM). They cover important topics like procurement, keeping track of inventory, and managing logistics. Diploma Courses: These are more detailed than certificate programs. They dive deeper into SCM, giving you a better understanding and practical skills in different areas. Professional Certifications: These are like badges of expertise in SCM. Certifications like Certified Supply Chain Professional (CSCP) or Certified in Production and Inventory Management (CPIM) are recognized worldwide. They show you’ve got specialized knowledge in certain aspects of SCM. Postgraduate Degrees: These are advanced degrees like an MBA or PGDM, but with a focus on supply chain management. They not only teach you SCM concepts but also give you management skills to handle it effectively. Comparison of Certification Programs and Their Focus Areas: Curriculum: Each certification program might focus on different parts of SCM. Some might concentrate on procurement, others on logistics, demand forecasting, or even sustainability. Duration and Format: The length of these programs can vary a lot. Some might only take a few weeks, while others could last for months or even years. They might be offered online, in a classroom, or a mix of both. Accreditation and Recognition: It’s really important to pick certifications from respected institutions or professional bodies. That way, you know they’re recognized by industry leaders and employers. In short, when exploring Supply Chain Management Courses, consider what kind of certification suits your needs best, and make sure it’s recognized by the industry. Why Supply Chain Management Course? Benefits of Enrolling in a Supply Chain Management Course: Skill Improvement: Supply Chain Management Courses help individuals develop practical skills and knowledge essential for streamlining supply chain operations, cutting costs, and boosting effectiveness. Industry-Relevant Education: The curriculum of Supply Chain Management Courses stays updated with industry trends, ensuring learners acquire current knowledge and skills sought after by employers. Career Growth: Obtaining certification or a degree in Supply Chain Management opens up various job opportunities across industries like manufacturing, retail, e-commerce, and consulting, enhancing career prospects. Global Reach: As supply chains expand globally, professionals proficient in Supply Chain Management find opportunities for international career advancement and mobility. How Supply Chain Management Education Improves Career Opportunities and Industry Relevance: Specialized Knowledge: Supply Chain Management Courses delve into areas such as inventory management, procurement strategies, supply chain analytics, and sustainable practices, making graduates highly desirable to employers. Networking Possibilities: Enrolling in Supply Chain Management Courses offers chances to connect with industry experts, professionals, and alumni, facilitating networking and career advancement. Leadership Growth: Advanced Supply Chain Management programs emphasize leadership and strategic management skills, preparing individuals for managerial and leadership roles within supply chain organizations. Adaptability and Resilience: In today’s fast-paced business world, Supply Chain Management education equips professionals with the flexibility and resilience needed to navigate disruptions, manage risks, and foster innovation within supply chains. Why Supply Chain Management As A Career? Exploring the Rising Demand for Supply Chain Professionals in India: Rapid Economic Growth: India’s economy is booming, which means supply chains are getting more complicated. That’s where skilled professionals come in handy, making sure everything runs smoothly. Globalization: Indian companies are going global, and international firms are setting up shop in India. This expansion means there’s a big demand for experts who can handle the complexities of global supply chains. Technological Advancements: Fancy tech like AI, IoT, and blockchain are changing how supply chains work. To keep up, we need professionals who know their way around these tools. Discussing the Wide Range of Career Opportunities in SCM: Logistics Management: Think of it as the traffic controller of supply chains. You make sure everything gets from point A to point B on time, whether it’s by truck, train, or plane. Procurement: You’re the one who finds the best deals for the materials a company needs. It involves negotiating contracts and keeping good relationships with suppliers. Inventory Management: It’s all about finding that sweet spot between having enough stuff in stock and not having too much. You keep track of inventory levels to save costs while still meeting demand.
Certified Warehouse management professional (CWMP)
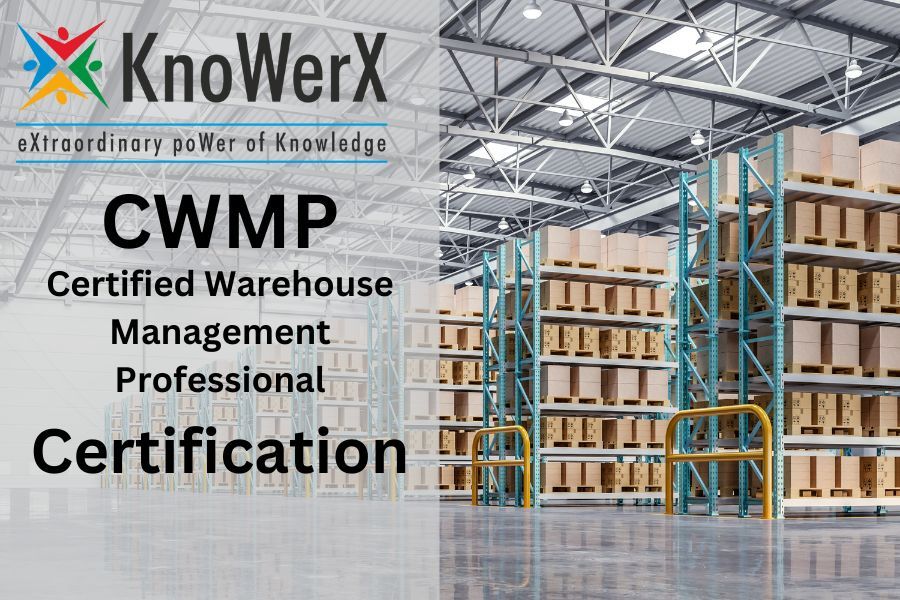
CWMP (Certified Warehouse Management Professional) Certification: A Pathway to Success in Warehouse Management In the world of logistics and supply chain operations, managing warehouses is crucial. Warehouses are dynamic places where efficiency is key, and it takes skilled professionals to keep things running smoothly. At KnoWerX, we understand just how important warehouse management is for keeping everything in order. That’s why we’ve created the Certified Warehouse Management Professional (CWMP) program. Let’s talk about what CWMP is all about and why it matters so much in our industry What is a Certified Warehouse Management Professional (CWMP)? The Certified Warehouse Management Professional (CWMP) program by KnoWerX equips individuals with vital skills and knowledge crucial for excelling in warehouse management roles. Covering a broad spectrum of topics such as inventory control, order fulfillment, warehouse layout optimization, transportation management, and risk mitigation strategies, our certification program ensures comprehensive preparation for effective warehouse operations. To get certified, you usually go through training or study materials that cover everything from how to keep track of inventory to organizing the layout of a warehouse efficiently. After that, you have to pass a tough exam given by official certifying bodies. Now, why bother getting CWMP certified? Well, here are some good reasons: Better Job Opportunities: Having CWMP certification opens up more doors for jobs in warehouse management. Employers often prefer hiring people who have proven they know what they’re doing. More Credibility: When you’re CWMP certified, it’s like having a stamp of approval on your resume. It shows that you’re serious about your job and that you’ve put in the effort to learn the ins and outs of warehouse management. Improved Performance: The skills and knowledge you gain from CWMP training help you do your job better. That means you’re more efficient, productive, and better at keeping customers happy. Networking: Being part of the CWMP community means you get to connect with other professionals in the field. This can lead to valuable collaborations, sharing of ideas, and even new career opportunities. Higher Salary Potential: With CWMP certification, you might find yourself earning more than those without it. Companies are willing to pay more for professionals who bring certified expertise to the table. So, if you’re working in warehouse management or aiming to get into the field, getting Certified Warehouse Management Professional (CWMP) certified could be a smart move for your career. How To Learn Warehouse Management System? Traditional Training Programs: These are like the classic classroom-style teachings you might be familiar with. Places like vocational schools or community colleges offer comprehensive courses covering everything from basic principles to advanced technologies. You’ll learn about managing inventory, keeping things safe in the warehouse, and how to operate equipment. Plus, some programs even give you hands-on practice in simulated warehouse setups, which is super helpful. Online Courses and Certifications: If you prefer learning at your own pace or from the comfort of your home, online courses are fantastic. Websites like Coursera, Udemy, and LinkedIn Learning have loads of options, from beginner stuff to more advanced topics. And if you’re looking for something more official, there are certifications like the Certified Warehouse Management Professional (CWMP) from KnoWerX institution. These certifications show you’re skilled in things like controlling inventory and running warehouse operations smoothly. Get Real-world Experience: Sometimes, nothing beats rolling up your sleeves and getting hands-on. Internships or entry-level jobs in warehouses can give you that practical knowledge you can’t get from books alone. You’ll see how things really work, get comfortable with the software and tech used in the industry, and pick up important skills like problem-solving and communication. Some companies even have special training programs or mentors to help you climb the ladder in warehouse management. What Is The Scope Of Warehouse Management? Warehouse management is super important in the big picture of how stuff gets from point A to point B in the business world. It’s like the backstage crew of a theater production – they make sure everything runs smoothly so the show can go on. Here’s what you need to know: Warehouse Management’s Role in the Supply Chain: Imagine a huge puzzle where each piece represents a step in getting products to customers. Warehouse management is one of those crucial puzzle pieces. It’s all about making sure things get to the right place at the right time. Warehouse managers keep an eye on what’s in stock, figure out the best way to store things, and work with other teams like shipping and manufacturing to make sure everything flows smoothly. Career Opportunities in Warehouse Management: If you’re thinking about diving into warehouse management, there’s a whole bunch of paths you can take. You might start out doing basic tasks like organizing inventory or moving stuff around. As you get more experience, you can climb the ladder to jobs like managing a whole warehouse or even overseeing the whole operation. There are also specialized roles if you’re really into stuff like tracking inventory or planning logistics. Demand for Warehouse Managers: Think of it like this – as more and more businesses grow and sell stuff online, they need individuals who can keep their warehouses running like well-oiled machines. That means there’s a growing demand for people who know their way around warehouse management. Whether it’s retail, manufacturing, or shipping, there are plenty of places looking for skilled warehouse managers. What Qualifications Do I Need To Be A Warehouse Manager? Educational Requirements: While formal education requirements may vary depending on the employer and specific job roles, a bachelor’s degree in logistics, supply chain management, business administration, or a related field is often preferred. Employers also consider candidates with relevant associate degrees or Certifications in warehouse management. Skills and Abilities: Leadership: You’ll need to lead and motivate teams, delegate tasks, and create a positive work environment. Organization: Being able to arrange the layout of the warehouse, manage inventory systems, and streamline workflow is crucial. Analysis: Understanding data and trends helps in making decisions to improve warehouse operations. Communication: You’ll
Inventory Management Certification
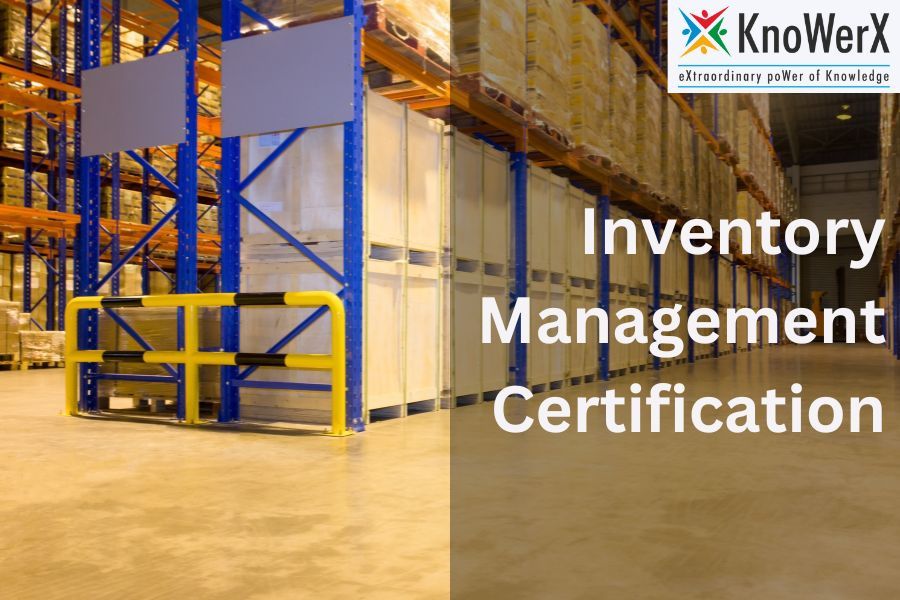
Inventory Management Certification in the Supply Chain Industry Inventory management plays a critical role in the efficiency and success of supply chain operations. It involves the strategic handling of goods and materials, ensuring the right products are available in the right quantities at the right time. This article explores the significance of inventory management within the supply chain industry and the importance of obtaining certification in this field. What Is Inventory Management? Inventory management is all about keeping track of, controlling, and making the most out of the stuff a company has and needs. It involves a bunch of tasks like figuring out how much stuff to have, guessing what the company will need later on, buying new things, storing them, and getting them to where they’re supposed to be. When done right, it helps companies have just enough stuff to meet what customers want, while also not having too much extra stuff that costs a lot. The main goal of inventory management is to find the right balance between how much stuff is available and how much is needed. By figuring out what customers will want and having the right amount of stuff, companies can avoid running out of things, spend less on storing stuff, and work more smoothly overall. Especially in today’s fast-moving business world, where what customers want changes a lot, having good inventory management is super important for staying competitive and keeping customers happy. What Is The Scope Of Inventory Management? Inventory management is all about making sure a company handles its goods smoothly and effectively. Here’s what it covers: Demand Forecasting: Predicting future demand for products based on historical data, market trends, and other relevant factors. Accurate demand forecasting is essential for ensuring that sufficient inventory is available to meet customer needs without excess or stockouts. Stock Control: Implementing strategies to regulate the quantity and movement of inventory within warehouses or distribution centers. This involves setting reorder points, safety stock levels, and implementing inventory tracking systems to monitor stock levels in real-time. Inventory Optimization: Inventory Optimization is all about making inventory work better for your business. It’s about finding ways to spend less money on storing inventory, making sure you don’t run out of stock, and getting items moving faster. We do this by using smart techniques like figuring out which items are most important (ABC analysis), calculating the best order quantities (EOQ), and using systems that deliver items just when we need them (JIT). These tricks help us save money, keep shelves stocked, and keep things flowing smoothly. What Is Required For Inventory Management? Achieving success in inventory management roles requires a combination of skills, qualifications, and personal attributes. Key requirements include: Analyzing Stuff: Inventory managers need to be good at looking at data, figuring out patterns, and using that info to decide how much stuff we need to keep, buy, or move around. Tech Savvy: They should be comfortable using computer programs made for inventory, like those fancy systems big companies use to keep track of everything they’ve got. Knowing How Things Flow: They need to understand how things move through a business, from buying stuff to getting it to customers. It’s like knowing how pieces fit together in a puzzle. Talking and Listening: They need to be able to talk to different people, like suppliers who bring in stuff or folks in the warehouse moving things around. Good communication helps make sure everyone knows what’s going on. Paying Close Attention: Details matter! They should be eagle-eyed when it comes to checking how much stuff is there and noticing if something’s not quite right. Fixing Problems: When things go wrong, they need to be like detectives, figuring out why and finding solutions, whether it’s running out of stuff or having too much. Getting Certified: Obtaining certification such as the CIMO (Certified Inventory Management Officer) offered by KnoWerX can significantly enhance one’s expertise in inventory management. While not obligatory, this certification demonstrates a deep understanding of inventory management principles and techniques, potentially broadening job prospects for individuals in the field So, by learning these skills, understanding how things move in a business, and maybe getting some extra training, folks can set themselves up for success in inventory management. It’s all about keeping things organized and running smoothly in the ever-changing world of supply chains. How To Become An Inventory Manager Educational Background: Start by getting a degree in something like supply chain management, logistics, business administration, or a similar field. This lays down the groundwork for understanding inventory management. Relevant Experience: It’s important to get hands-on experience. Look for internships or entry-level jobs in areas like inventory control, procurement, or logistics. This helps you learn the ins and outs of managing inventory. Keep Learning: Take additional courses or attend workshops focused on inventory management. This shows that you’re committed to learning and improving your skills. Get Certified: Consider getting certified in inventory management. There are certifications like CIMO (Certified Inventory Management Officer) that show you’ve mastered the practices of inventory management. Network: Build connections within the supply chain industry. This can open doors to mentorship opportunities and job openings in inventory. By following these steps, you can work your way towards becoming a successful inventory manager! Inventory Management Vs Warehouse Management Inventory management and warehouse management are both crucial parts of making sure things run smoothly in supply chains, but they handle different jobs. Inventory Management: This is about finding the right balance of stuff you have in stock. You want enough to satisfy customers without having too much and wasting money on storage or risking running out. It involves figuring out how much you’ll need, when you’ll need it, and making sure you have just the right amount at the right time. Warehouse Management: This one deals with the physical side of things – where you actually keep all that stuff. It’s about making sure everything is organized in the warehouse so you can find it easily, moving things around efficiently, and
Supply Chain Planning Certificate

Navigating the Supply Chain Planning Certificate Program Supply chain management is all about making sure things move smoothly from the makers to the buyers. And planning is a big part of making that happen well. So, if you’re interested in being great at this, getting certified in supply chain planning with KnoWerX can be a smart move. This article covers everything you need to know about it, like what it is, how to get it, what kind of jobs you can get, how much it costs, and some final thoughts to consider. What Is Supply Chain Planning? Supply chain planning is all about making sure things move smoothly from one point to another in a business’s supply chain. This includes figuring out how much stuff is needed, when it’s needed, and how to get it where it needs to go efficiently. It involves predicting what customers will want, managing how much stuff is kept in storage, scheduling when things are made, and figuring out the best ways to transport everything. Good supply chain planning helps companies meet customer needs without wasting resources or money. It’s important because it helps businesses match what they make and buy with what customers want, and with what they can do. By knowing what customers are likely to want and keeping just enough stuff on hand, companies can avoid running out of products or having too much leftover. This keeps customers happy and saves money. Also, supply chain planning helps companies make smarter decisions by giving them information about how to best use their resources, when to make things, and how to move them around efficiently. What Is A Supply Chain Planning System? A supply chain planning system is like a computer program that helps companies plan and manage their supply chain activities. It pulls together information from different places to help predict things like how much demand there will be for products, how much inventory to keep, and how to make decisions about production and transportation. These systems have special features that help with things like predicting demand, figuring out the best way to manage inventory, planning production schedules, and managing transportation. Using a supply chain planning system helps companies work more efficiently. They can use fancy math and analysis to make smarter decisions, cut down on the time it takes to get products to customers, and adapt quickly when things change in the market. These systems also make it easier for different teams within a company, as well as outside partners, to work together and stay on the same page. Supply Chain Planning Process The process of planning your supply chain usually has a few steps that are all connected: Forecasting Demand: This means trying to predict how much of your product or service people will want in the future. You look at things like past sales, what’s happening in the market, and other important info. Planning Inventory: Figuring out how much stuff you should have in stock to meet demand without having too much or too little. You want to avoid running out of stock and also don’t want to be stuck with too much stuff that you can’t sell. Organizing Production: Making a schedule for when you’ll produce your goods. This schedule should match up with what you expect people will want to buy and what resources you have available. Sorting out Distribution: Deciding the best way to move your products from where they’re made to where they’re sold. This involves getting things to distribution centers and then to customers efficiently. Working Together in the Supply Chain: This is about collaborating with everyone involved in making and selling your product. That means talking with suppliers, manufacturers, distributors, and others to make sure everyone is on the same page and things run smoothly. Supply Chain Planning Examples There are many examples of smart supply chain planning strategies used in different industries: Just-in-Time (JIT) Manufacturing: Toyota came up with this idea. Instead of making a lot of stuff and keeping it in a warehouse, they only make things when they’re needed. This saves money on storing things for a long time. Cross-Docking: Big stores like Walmart do this. They have special places called cross-docking facilities. These places help to move things from the suppliers to the stores quickly. It means they don’t have to keep stuff in the warehouse for too long. Vendor-Managed Inventory (VMI): In VMI, suppliers keep an eye on how much stuff is in the stores and fill it up when it’s running low. This helps make sure there’s always enough stuff in the store without wasting too much. It’s like having someone take care of your shopping list for you. Supply Chain Planning Jobs Professionals who specialize in supply chain planning have a variety of career options available to them, such as: Supply Chain Analyst: This role involves examining data, forecasting future trends, and finding ways to improve the efficiency of supply chain processes. Demand Planner: Demand planners predict how much of a product will be needed, manage inventory levels, and work closely with different teams to make sure products are available when customers want them. Supply Chain Manager: In this position, individuals are responsible for overseeing the entire supply chain process, from start to finish. They implement long-term strategies, make sure everything runs smoothly, and allocate resources effectively. How To Get a Supply Chain Planning Certificate? To Get a Supply Chain Planning Certificate, you’ll typically follow these steps: Choosing the Right Certificate: First things first, you want to find a Certificate program that’s well-respected in the field. Look into popular choices like the APICS Supply Chain Planning Certificate. This Certificate is highly valued and trusted by professionals. Also, check out what KnoWerX has to offer—they provide courses for supply chain planning certificates too. Meet Eligibility Requirements: Each program will have its own set of requirements. These might include having a certain level of education, relevant work experience, or completing specific training courses. Make sure you meet these
APICS CLTD Certification : Complete Guide
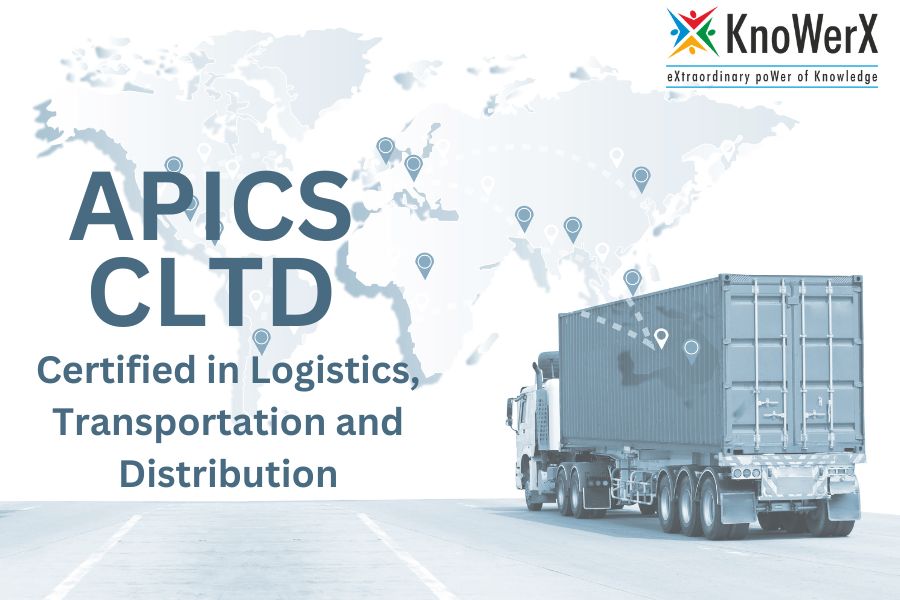
Apics CLTD (Certified in Logistics, Transportation, and Distribution) In the world of moving goods around, whether it’s by truck, plane, or other means, ensuring efficient transportation is crucial for the global supply chain. Professionals in this field are always seeking ways to showcase their expertise, and one way to do so is by obtaining the APICS CLTD (Certified in Logistics, Transportation, and Distribution) Certification. This article aims to delve deeper into the significance of the APICS CLTD Certification, exploring what it entails, how one can attain it, and why it holds such value for career advancement. By understanding the ins and outs of this certification, individuals can better grasp its importance in the logistics and transportation industry, paving the way for enhanced career opportunities and professional growth. What Is CLTD Method? The APICS CLTD Certification is all about a method that goes beyond the usual ways of doing logistics. It’s like a big-picture strategy for managing how things move and get to where they need to be in the supply chain. This method looks at transportation, distribution, and planning in a detailed way. Moving items isn’t only about going from A to B; it’s about doing it smartly, effectively, and sustainably, with modern tech. When people dive into this method, they learn a set of skills that match what the industry needs. It’s like becoming an expert in navigating the complicated world of logistics. But the CLTD method isn’t just theory – it’s a practical toolkit. It gives professionals the tools they need to tackle real problems in logistics. By thinking strategically and taking a big-picture approach, professionals can make operations smoother, save money, and make the supply chain stronger. The focus on efficiency and sustainability is all about keeping up with the current trend of responsible logistics management. This makes the CLTD method not just a thing for today but something that’s ready for the future. It’s a framework that can adapt to changes and help professionals make a real impact in the field. How Do I Get A CLTD Certificate? Getting a CLTD certificate involves a thoughtful and organized approach that requires dedication. Before diving into the certification process, candidates need to meet certain educational and professional requirements. This sets the foundation for a thorough evaluation of their skills. The certification process itself is challenging, with exams covering important aspects of logistics, transportation, and distribution. To tackle this, Apics provides various resources like study materials, practice exams, and specialized training courses. Engaging with these resources helps candidates not only gain the knowledge necessary for the exams but also practical insights crucial for their professional growth. Obtaining the CLTD certification goes beyond just academics; it’s a transformative experience that sharpens practical skills and problem-solving abilities. The structured nature of the process ensures that certified professionals are well-prepared to handle the diverse challenges in logistics and supply chain management. It’s not just about theoretical knowledge; the certification process emphasizes applying concepts in real-world situations, fostering a mindset focused not only on passing exams but also on creating tangible value in the professional field. Is CLTD Certification Worth It Should you consider getting the CLTD Certification? Well, it’s more than just a fancy title on your resume. This certification is like a badge of honor for folks in the logistics field. It shows you’re serious about doing your job well. Getting certified isn’t just a one-time thing. It’s an investment that keeps paying off. It can open doors to better job opportunities and even fatter paychecks. Plus, it puts you in the spotlight as someone who knows their stuff in the competitive logistics world. And it’s not just about you. When you get CLTD certified, it’s like sending a ripple through the whole industry. Employers love having certified folks on their teams. It’s a sign that they’ve got someone who really understands the ins and outs of logistics. In a world where every detail matters, having CLTD Certification is like a stamp of approval. It tells everyone around that you’ve got the skills to handle the challenges of modern logistics. So, if you’re thinking long-term and want to make a mark in the logistics world, getting CLTD certified is a smart move. What Is The Difference Between CPIM And CLTD? Certainly! Let’s dive deeper into the distinctions between CPIM (Certified in Production and Inventory Management) and CLTD (Certified in Logistics, Transportation, and Distribution) certifications within the realm of supply chain management. CPIM is all about what’s happening within a company’s supply chain. It hones in on the internal aspects, particularly focusing on how production processes are managed and how inventory is handled within the company. Individuals pursuing CPIM are often those deeply involved in the intricacies of production and ensuring efficient inventory management to keep things running smoothly inside the organization. On the other hand, CLTD broadens the scope significantly. It looks beyond the internal workings of a company and delves into the external factors of the supply chain. CLTD covers areas like transportation, distribution, and logistics planning. Professionals aiming for CLTD are those whose responsibilities extend beyond the company’s walls. They are concerned with how goods are transported, distributed, and the overall strategic planning involved in the larger logistics landscape. These differences go beyond just the logistics of a supply chain; they reflect diverse career paths within the broader domain of supply chain management. CPIM is tailored for those primarily engaged in production and inventory management within a company, ensuring the internal processes run efficiently. In contrast, Apics CLTD is designed for individuals whose responsibilities involve the external aspects of the supply chain, encompassing transportation, distribution, and logistics planning. Recognizing these distinctions is crucial for professionals as they strategically align their career goals with the certification that best suits their aspirations. This understanding empowers individuals to make informed decisions about their certification choices, aligning them with their specific career objectives within the multifaceted world of supply chain management. Who Is Eligible For CLTD Exam? To start your CLTD certification
Certified Integrated Business Planner (CIBP) Certification
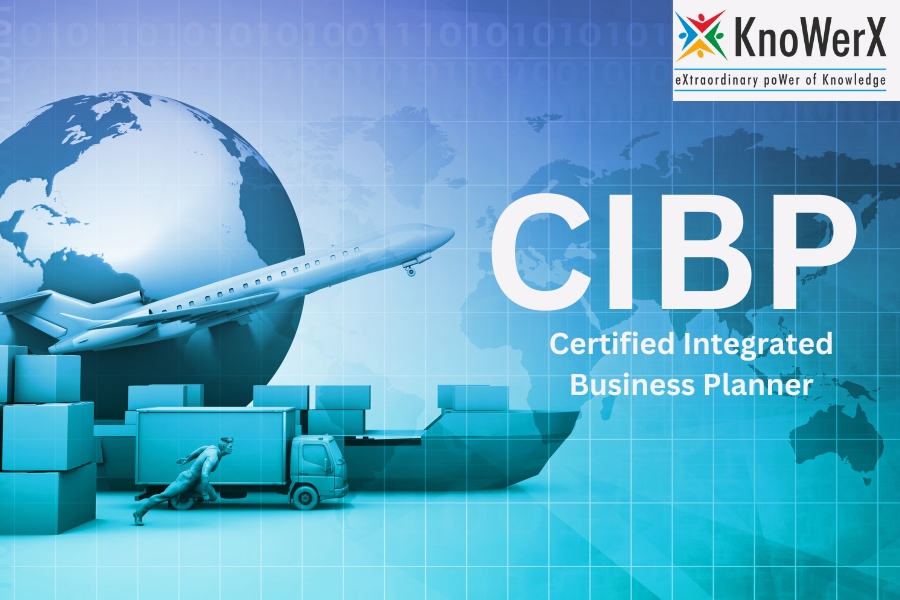
Unlocking Business Potential: The Certified Integrated Business Planner (CIBP) Certification Explained In today’s fast-paced business world, companies need skilled professionals who can tackle challenges head-on and steer business strategies in the right direction. That’s where the Certified Integrated Business Planner (CIBP) certification comes in. It’s like a stamp of approval, showing that someone has expertise in strategic planning, forecasting, supply chain management, and financial know-how. Importance in Business Planning Effective business planning is like building a sturdy house on a solid foundation. The Certified Integrated Business Planner (CIBP) certification emphasizes just how crucial it is to align big-picture goals with day-to-day operations. It’s about making sure businesses can roll with the punches of the market, make the most of resources, and make smart decisions. With this certification, professionals are armed with the skills to guide businesses through changes and keep them growing strong, even when the business landscape gets rocky. What is Certified Integrated Business Planner (CIBP) Certification? Definition and Overview Certified Integrated Business Planner (CIBP) Certification is like a badge of honor for people who know their stuff regarding integrated business planning. It shows they’ve got a solid grasp on balancing demand and supply, crunching numbers, managing risks, and making smart decisions involving different parts of a company working together. Accrediting Body and Standards This certification isn’t just handed out to anyone. It’s overseen by respected organizations that make sure the standards are super high. They work closely with industry experts to keep the certification program up-to-date with the latest ideas and technologies in business planning. They also regularly check in to make sure the program stays relevant as things change in the business world. Eligibility Criteria To achieve Certified Integrated Business Planner (CIBP) Certification, participants need to meet certain standards. This usually means they should have a basic grasp of how businesses are managed and how processes work, especially in the planning part. It might also require having some experience in things like managing supply chains or handling finances. What Does Certified Integrated Business Planning Do? Role and Responsibilities of Certified Integrated Business Planner (CIBP) Professionals: Certified Integrated Business Planners have a crucial job within companies. They’re like the conductors of an orchestra, making sure all the different parts – like finance, sales, operations, and supply chain management – work together smoothly. Using their skills in analyzing data, making predictions, and planning strategically, Certified Integrated Business Planner (CIBP) professionals ensure that every department is working towards the same big goals. Importance in Business Strategy: Integrated business planning isn’t just about short-term fixes; it’s a big part of long-term strategy for businesses today. Certified Integrated Business Planner (CIBP) professionals play a key role in shaping and carrying out these strategies. They dive deep into data analysis and planning for different scenarios to provide valuable insights. Their input ensures that strategies aren’t just good ideas but also practical for how the company works daily. Integration with Organizational Functions: Integrated business planning looks at the whole picture of how a company runs. Certified Integrated Business Planner (CIBP) professionals are like the glue that holds different parts of the company together. They encourage teamwork between departments, breaking down barriers and making sure everyone’s on the same page. By smoothing out processes across the board, they make communication, resource management, and decision-making easier. This helps the company stay nimble and responsive in a fast-paced business world. Certified Integrated Business Planner (CIBP) Benefits Better Business Performance: When businesses adopt integrated planning led by Certified Integrated Business Planner (CIBP) experts, they tend to perform better in various aspects. Companies can use their resources more wisely, cut down on waste, and grab hold of growth opportunities more effectively by making sure that their big-picture goals match up with day-to-day activities. Smarter Decision Making: Making smart choices is crucial in today’s complicated business world. Certified Integrated Business Planner (CIBP) professionals give companies the tools and knowledge they need to make decisions based on data. By bringing together different pieces of information and exploring different scenarios, they give decision-makers a clear picture of what could happen with each choice. Smoother Operations: The key to any organization’s success is having smooth operations. Getting certified in CIBP helps a lot with this. Certified Integrated Business Planner (CIBP) experts know how to make processes work better and measure how well things are going. They help get rid of things that slow things down and make everything run more efficiently. More Efficiency and Productivity: Certified Integrated Business Planner (CIBP) professionals are great at bringing different parts of a company together and making sure everyone is working well together. By finding ways to do things better, cutting out things that aren’t needed, and finding areas to improve, they help companies keep getting better and better at what they do. Certified Integrated Business Planning Example Real-Life Case Study: How a Big Company Improved with Better Planning Imagine a big company that sells all sorts of everyday items worldwide. They’re in a tough market with lots of competition. To keep their lead, they decided to try something new: a Certified Integrated Business Planner (CIBP). This means they’re bringing together their sales, marketing, finance, and supply chain teams to work more closely. They want to use data and teamwork to predict what customers will want, manage their stock better, and run their business smoothly. How They Made It Happen and What Changed First, everyone from different parts of the company started talking more. They set clear goals and figured out the important numbers to watch. They also used fancy tools to guess what customers might buy next. Then, in meetings, they made plans together. This way, everyone knew what to do to make the most of good chances and avoid problems. After using Certified Integrated Business Planner (CIBP), the company noticed some great changes. They could deliver things quicker, didn’t have too much stock lying around, and customers seemed happier. Plus, they started making more money. By always looking for ways to do better and