Why Supply Chain Visibility is a Must-Have in 2025
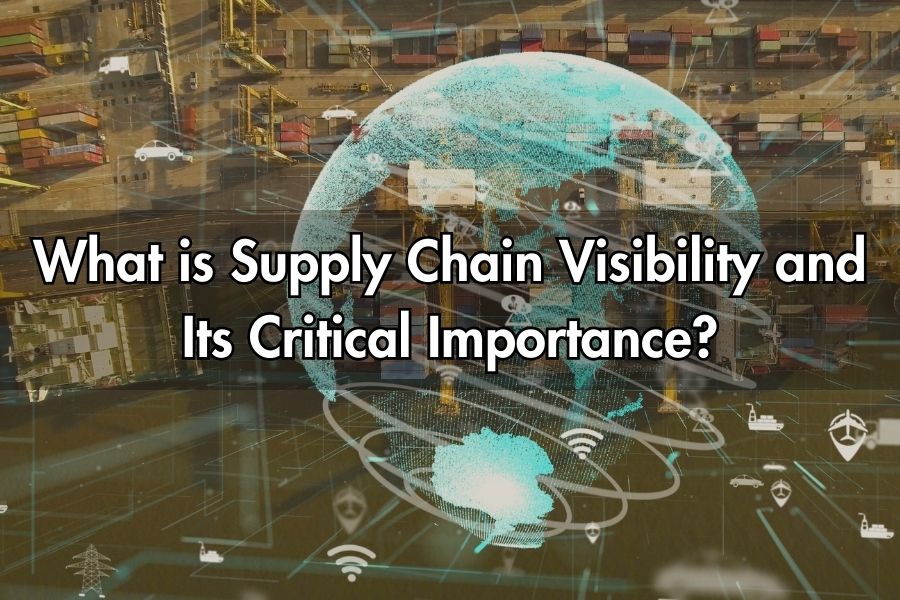
What is Supply Chain Visibility and Its Critical Importance? Supply chain management is a critical element of modern business operations, ensuring goods and services move seamlessly from production to consumption. Within this framework, supply chain visibility (SCV) has emerged as a game-changer, helping organizations stay agile and competitive in an ever-changing global market. It is no longer just about moving goods; it’s about gaining real-time insight into every part of the process to make data-driven decisions and respond proactively to challenges. The importance of SCV has grown significantly with the increasing complexity of global supply chains. Businesses today face challenges such as fluctuating demand, geopolitical uncertainties, and the need to adapt quickly to changing market dynamics. Supply chain visibility not only helps businesses address these challenges but also creates a competitive edge by improving efficiency, reducing risks, and enhancing customer satisfaction. What is Supply Chain Visibility? Supply chain visibility refers to the ability to track, monitor, and manage the movement of goods, data, and resources across the entire supply chain. It involves integrating various technologies, processes, and systems to provide real-time, end-to-end insights into supply chain activities. In practical terms, SCV ensures that companies know the location and status of their goods at every stage—whether they are in production, transit, or storage. This visibility is crucial for identifying potential issues, optimizing workflows, and maintaining transparency with stakeholders, including suppliers, logistics providers, and customers. SCV goes beyond physical tracking. It includes financial transactions, inventory levels, and supplier performance metrics. For example, a retailer might use SCV to check stock levels in a warehouse, track incoming shipments from suppliers, and forecast demand for the upcoming season—all in real-time. The rise of digital technologies, such as IoT devices, blockchain, and AI, has made achieving supply chain visibility easier than ever. However, it also comes with challenges, such as data integration and managing the complexity of global supply chains, which businesses must address to unlock SCV’s full potential. Goals of Supply Chain Visibility The objectives of Supply Chain Visibility extend beyond simply tracking goods; they aim to create a responsive, efficient, and risk-resilient supply chain. Below are the primary goals of supply chain visibility: 1. Enhancing Transparency Transparency is the cornerstone of effective supply chain management. SCV ensures that all stakeholders, including suppliers, manufacturers, logistics providers, and customers, have access to accurate, real-time information. This transparency reduces misunderstandings, fosters trust, and facilitates seamless collaboration across the supply chain. 2. Optimizing Operations Visibility into every stage of the supply chain allows businesses to identify inefficiencies, such as delays in production, inventory mismanagement, or logistical bottlenecks. By addressing these issues promptly, companies can reduce costs, minimize waste, and streamline their operations. 3. Mitigating Risks Global supply chains are exposed to numerous risks, including natural disasters, geopolitical tensions, supplier failures, and demand fluctuations. SCV helps companies proactively identify these risks and implement contingency plans, ensuring business continuity. 4. Improving Decision-Making Supply chain visibility provides actionable insights that support data-driven decision-making. Whether it’s choosing a reliable supplier, optimizing inventory levels, or responding to market trends, SCV enables businesses to make informed choices. 5. Enhancing Customer Satisfaction Customers today expect greater transparency in their transactions, including updates on the status and location of their orders. SCV ensures that businesses can meet these expectations, leading to improved customer trust and loyalty. What Are the Problems and Solutions in Supply Chain Visibility? Achieving full visibility in supply chain operations is challenging due to various factors. Below are some common problems and their potential solutions: Supply Chain Visibility Problems Data Silos Different departments within an organization often use disconnected systems that do not communicate effectively. This fragmentation creates data silos, preventing the seamless flow of information across the supply chain. Lack of Standardization Inconsistencies in data formats and reporting methods among different suppliers, logistics providers, and partners make it difficult to integrate and analyze information. Complex Global Operations Managing a global supply chain involves dealing with diverse regulations, languages, currencies, and time zones. This complexity adds layers of difficulty to achieving end-to-end visibility. Limited Technology Adoption Many businesses, especially small and medium-sized enterprises (SMEs), lack access to advanced technologies such as IoT, blockchain, and predictive analytics, which are essential for SCV. Data Overload With the increasing use of IoT devices, sensors, and automated systems, companies generate vast amounts of data. Without the right tools and expertise, managing and analyzing this data can be overwhelming. Supply Chain Visibility Solutions Integrating Advanced Technologies Adopting technologies such as the Internet of Things (IoT), artificial intelligence (AI), blockchain, and machine learning can provide real-time insights and enhance data accuracy. IoT sensors, for instance, can track shipments, monitor inventory, and provide real-time updates on transportation. Using Cloud-Based Platforms Cloud technology facilitates seamless data sharing and collaboration among stakeholders, regardless of their location. It also supports scalability and ensures data security. Implementing Standardized Processes Developing standardized protocols for data collection, reporting, and analysis ensures consistency and simplifies integration across the supply chain. Leveraging Data Analytics Advanced analytics tools can process large volumes of data to uncover patterns, predict disruptions, and provide actionable insights. Predictive analytics, for example, can forecast demand fluctuations and help businesses plan accordingly. Building Strong Partnerships Collaboration with suppliers, logistics providers, and other partners ensures alignment and improves data sharing. Establishing clear communication channels and mutual trust is crucial for achieving visibility. What Are the Types of Supply Chain Visibility? Supply chain visibility encompasses various aspects of the supply chain, each contributing to a comprehensive understanding of operations. 1. Inventory Visibility Inventory visibility ensures that businesses can track stock levels across all locations, including warehouses, retail outlets, and in-transit shipments. This helps prevent overstocking, stockouts, and excessive carrying costs. 2. Transportation Visibility Transportation visibility focuses on monitoring the movement of goods in real-time. By tracking shipments, businesses can optimize delivery routes, reduce delays, and provide accurate delivery timelines to customers. 3. Order Visibility Order visibility allows both businesses and customers to track the status of orders, from placement to delivery. This transparency builds customer
Alumni Community to Boost Education for Students in Supply Chain Management
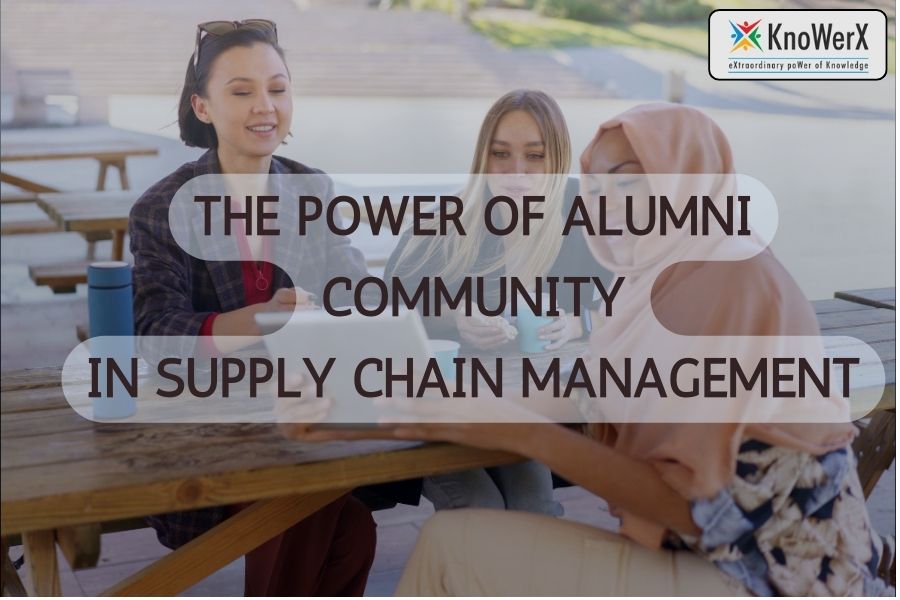
The Power of Alumni Community to Boost Education for Students in Supply Chain Management SCM is a comprehensive umbrella term that encompasses many different disciplines, including logistics, procurement, data analytics, and strategic planning. In contrast to SCM, where information is changing constantly and always adapting to the developments that occur in the market-place, SCM requires a broader range of skills, encompassing more than just the ‘black letter’ knowledge taught by textbooks. Alumni communities thus emerge as a valuable resource in SCM education that facilitates the transfer of knowledge acquired at the educational institutions to the real requirements of the industry. Alumni engagement thus would provide a channel through which institutions can create for students more value-added learning opportunities in conformity with industry needs. The role of alumni in enriching SCM Education Alumni are in a position to significantly impact SCM education due to their ability to share experience and knowledge. Knowledge Sharing: Alumni are the best sources of insight that one can get from the entire career, as they bring real-world experience in explaining how SCM theories are used in practice. Such knowledge sharing is very essential since it makes academic concepts more real and relevant to the understanding of SCM operations. Mentorship Opportunities: Alumni can act as mentors by offering advice on career paths, skill building, and trends in the industry. The mentorship from professionals experienced in the field will be instrumental in helping students make decisions regarding areas of specialization, skills needed, and certifications. Workshops and Guest Lectures: Alumni can also conduct workshops or guest lectures on specific topics of SCM. They can be invited as experts to give a talk on any SCM area, such as on inventory management, demand forecasting, logistics, or procurement, which will give rich insight to the students in the specific areas of SCM and how these segments really work together. Industry Relations through Alumni Network Alumni networks are a good source for creating professional relationships within the field. Often, these contacts become invaluable leads in the future for the student. Internship and Job Opportunities: Many graduates hold positions that allow them to offer internship placements or, better still, full-time job positions. Having such opportunities often gets students off to a good start in their SCM careers, as they have early opportunities to apply the learning and get practical experience by graduation. Alumni interaction with networking events and conferences presents the industry people before the students while keeping them updated with all the market SCM trends as well as the connections generated in the course of these conferences are fruitful. Collaborative Projects and Case Studies: Collaboration with alumni can also help provide students with real-life SCM problems in collaborative projects. Such projects offer a means through which theory-based knowledge is applied practically in order to solve practical problems. They enhance problem-solving and develop the insight of working requirements for SCM. Long-term Career Development and Alumni Support Alumni also support SCM students and graduates for long-term career development. Continuous Learning and Professional Development: Alumni can counsel students and fresh graduates about certifications, workshops, and advanced degrees relevant to SCM. Alumni guidance keeps the students updated and in the running by following relevant qualifications. Career Guidance and Goal Setting: Alumni can help students set achievable career goals and give them advice on job search strategies, industry expectations, and progression in SCM. Supportive SCM Community: A robust alumni network gives a supportive community to students where they can rely throughout their careers. It will inspire the alumni to stay in touch and give back to the institution, thus creating a cycle of mentorship and support towards future SCM professionals. Encouraging Innovation and Problem-Solving Skills The alumni facilitate bringing innovation and practical problem-solving skills among SCM students. It accesses real-world problem-solving because of the interesting innovative solutions to the challenges SCM-related, graduates are able to share and that helps in training students in thinking creatively with novel ideas toward problem-solving. Hackathons and Innovation Challenges. Some of the alumni can have hackathons or other competing events as their innovation challenge to the student participants while encouraging them to develop innovations in solving the different types of problems involving SCM. These innovation competitions foster concepts of SCM in critical ways and creativity. Expose students to emerging technologies: The alumnus exposes the students to the cutting-edge technologies, such as AI, blockchain, and IoT, which are changing the SCM world. This increases the awareness of the innovations and thus better prepares them for the technological future. Enhancing Institutional Reputation and Credibility It not only enhances the student experience but also the institutional reputation and credibility in industry circles. This also testifies to the quality of the institution and is an attractive magnet for the high-caliber students and faculty seeking a reputable SCM program. Elevated Profile in SCM Industry: Alumni engagement brings greater recognition of the institution in the SCM industry, which further leads to the creation of more opportunities for students through partnerships, collaborations, and increased visibility at conferences. Improving Institutional Rankings and Funding: Alumni support often manifests in the form of donations, grants, and collaborations that directly impact SCM education programs. Better resources would improve the quality of the curriculum, facilities, and support services, thus reflecting well on institutional rankings. Facilitating Global Perspectives and Cultural Competence SCM is a connected field worldwide, and alumni who have experience in international supply chains provide students with insights on global supply chains. International Networking and Opportunities: SCM students are exposed to different international practices and challenges, while the alumni working in international positions give them a well-rounded outlook of SCM beyond just some local contexts. Cross-cultural learning: Alumni from these diverse cultural settings foster a cross-cultural competence that could be developed among SCM students. This would, at least, enable SCM practitioners to navigate global supply chains and understand the complexities within international trade and logistics systems. Study Abroad and Exchange Programs: The alumni can help develop or support the exchange programs that allow the students to experience SCM education in other countries.
Mastering Demand Forecasting in Supply Chain

Mastering Demand Forecasting in Supply Chain: Top Importance, Techniques, and Benefits Definition of Demand Forecasting: Demand forecasting involves the process of estimating future customer demand using historical data, market research, and statistical methods. This helps businesses make informed decisions regarding production, inventory, and supply chain activities. Effective forecasting is essential to avoid unexpected stockouts or overproduction, ensuring balanced operations. Importance of Demand Forecasting in Supply Chain Management (SCM): In SCM, demand forecasting plays a crucial role by driving key supply chain functions, from procurement to distribution. It helps businesses plan better, reduce uncertainty, and align resources efficiently. Without accurate forecasting, companies risk misalignment between supply and demand, leading to wasted resources or missed sales opportunities. How accurate forecasting influences business efficiency and customer satisfaction: Accurate demand forecasting enables businesses to streamline operations, reduce operational costs, and ensure timely delivery of products. It also allows for proactive management of supply chain disruptions. By anticipating customer needs, companies can enhance satisfaction by meeting expectations with minimal delays or stockouts. The Role of Demand Forecasting in Supply Chain 2.1 Optimizing Inventory Management: Demand forecasting helps businesses maintain optimal inventory levels by anticipating future needs. It prevents both stockouts, which can lead to lost sales, and overstock situations, which tie up capital and increase storage costs. This balance reduces waste and ensures that inventory moves efficiently, minimizing holding costs. 2.2 Enhancing Supplier and Manufacturer Relationships: Accurate forecasts allow companies to synchronize their production schedules with suppliers, ensuring timely procurement of raw materials and production inputs. This fosters a collaborative relationship between suppliers and manufacturers, leading to improved communication, trust, and fewer disruptions in the supply chain. 2.3 Improving Order Fulfillment: Demand forecasting directly impacts the ability to fulfill customer orders on time, enhancing customer satisfaction. By predicting demand accurately, businesses can reduce lead times, optimize delivery schedules, and minimize the risk of stockouts or late deliveries. This results in smoother order processing and better customer service. Types of Demand Forecasting in Supply Chain 3.1 Qualitative Forecasting: Qualitative forecasting relies on expert opinions, surveys, and market research to predict demand, especially for new products or markets without historical data. It is particularly useful in situations where quantitative methods are not viable. This method incorporates insights from market trends and industry knowledge to provide a more intuitive forecast. 3.2 Quantitative Forecasting: Quantitative forecasting uses statistical methods such as time-series analysis, regression models, and machine learning algorithms to predict demand based on historical data. These methods provide objective and data-driven insights, making them highly reliable for established products and markets. They can also be scaled to analyze large datasets for more precise forecasting. 3.3 Collaborative Forecasting: Collaborative forecasting involves input from multiple departments—such as sales, marketing, and operations—to create a more accurate forecast. Through a process like Sales and Operations Planning (S&OP), businesses can align their forecasts with cross-functional objectives, improving the overall accuracy of demand predictions and fostering interdepartmental cooperation. Techniques for Demand Forecasting 4.1 Moving Averages: Moving averages calculate the average demand over a set time period to smooth out fluctuations and provide a stable forecast. This technique is simple and effective for identifying general trends, especially in markets with consistent demand patterns. It can help businesses avoid reacting to short-term demand spikes or drops that could skew production planning. 4.2 Exponential Smoothing: Exponential smoothing is a forecasting technique that assigns greater importance to more recent demand data. This makes it more responsive to current market conditions or emerging trends. It is especially effective in dynamic markets where demand patterns shift frequently, allowing businesses to adjust forecasts quickly to reflect these changes. 4.3 Seasonal Indexes: Seasonal indexing adjusts demand forecasts based on seasonal variations, such as increased sales during holidays or slow periods in off-seasons. By recognizing these predictable fluctuations, businesses can better plan for peak and low-demand periods. This technique is vital for industries where demand is cyclical, like retail or tourism. 4.4 Machine Learning and AI: Advanced techniques like machine learning and artificial intelligence enable companies to identify complex patterns and trends in large datasets. These technologies can automatically adjust forecasts based on real-time data and emerging trends. This capability makes machine learning models highly adaptive, offering significant advantages in fast-paced or highly volatile markets. Challenges in Demand Forecasting 5.1 Data Inaccuracy: Forecasting relies heavily on accurate and reliable data. When data is incomplete, outdated, or incorrect, the forecast can lead to poor decision-making. Businesses need to ensure data quality by implementing robust data collection and management systems to minimize errors and improve forecasting precision. 5.2 Market Volatility: External factors such as economic shifts, consumer behavior changes, political instability, and global events (e.g., pandemics) can create volatility in demand, making it difficult to predict. Companies must be agile in their forecasting approach to account for these unpredictable changes and adjust their strategies accordingly. 5.3 Lead Time Variability: Variations in lead times—how long it takes for goods to be delivered—pose challenges for accurate forecasting. Unexpected delays in production or shipping can disrupt the supply chain and cause discrepancies between forecasted and actual demand. Reducing lead time variability requires closer collaboration with suppliers and improved logistics management. 5.4 Over-reliance on Technology: While advanced technologies can improve forecasting accuracy, over-reliance on them without human oversight may lead to errors. Human judgment remains important, especially in interpreting results and accounting for unique market conditions that algorithms may overlook. A balance between automation and human input is key to successful forecasting. Best Practices for Effective Demand Forecasting 6.1 Utilizing Real-Time Data: Real-time data allows businesses to make timely adjustments to their forecasts as new information becomes available. It enables companies to respond more quickly to shifts in demand, minimizing the impact of forecast errors. Incorporating real-time data also helps align forecasts with current market trends and customer behavior. 6.2 Implementing Cross-Functional Collaboration: Effective demand forecasting requires input from multiple departments such as sales, marketing, and finance. Collaboration ensures that all aspects of the business are considered in the forecast, resulting in more accurate and actionable predictions. Cross-functional
Alumni Community for Students Career- Start Your Career
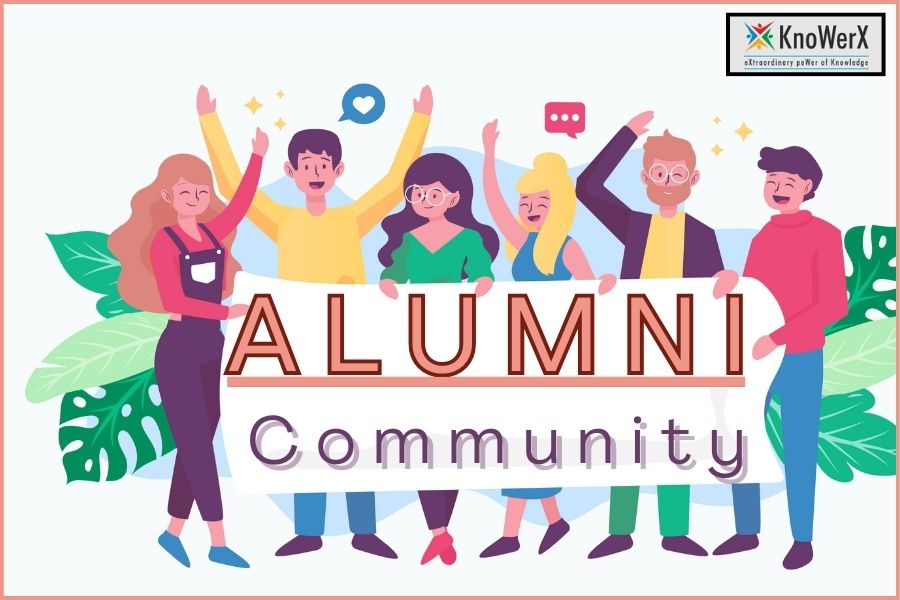
Alumni Community for Students Career – Start Your Career: Join KnoWerX Today! In today’s fast-paced professional landscape, staying connected and informed is more crucial than ever. That’s why we’re excited to introduce the KnoWerX Alumni Community—a vibrant space designed specifically for our alumni professionals. Here, you can explore the latest industry trends, gain valuable insights, and share your remarkable stories and achievements. Recently, KnoWerX has been awarded as the No. 1 ASCM Partner in the world. As KnoWerX is a Premier Elite Partner of ASCM. With over 32 years of experience in education and consultancy, our team has trained and consulted for major companies both in India, middle east, and internationally. Why the KnoWerX Alumni Community? The KnoWerX Alumni Community isn’t just a networking platform; it’s a hub for growth and collaboration. Here’s what makes it special: Stay Updated on Trends The supply chain management field is evolving rapidly. Our community will keep you informed about the latest trends, technologies, and best practices so you can stay ahead of the curve. Valuable Insights and Learning Opportunities Participate in discussions, webinars, talk shows, and trainings led by industry experts. Gain insights that can elevate your career and help you tackle new challenges. Networking and Relationship Building Effortlessly manage alumni relationships with our automation and digitization tools. Connect with former classmates and industry peers to build a supportive network that can guide you through your career journey. Job Opportunities The KnoWerX Alumni Community will provide access to a wide range of job opportunities in the supply chain management sector. Whether you’re seeking a new role or looking to hire, our platform will help you find the perfect match. Mentorship Programs Discuss any formal or informal mentorship opportunities within the KnoWerX Alumni Community. This section could emphasize how seasoned professionals can mentor fresh graduates, or mid-career professionals can connect with industry veterans to seek guidance on challenges they face. One-on-One Mentoring: Provide personalized mentorship opportunities for members. Peer-to-Peer Learning: Introduce peer mentorship programs where professionals at similar career stages can share best practices and support each other. Interactive Alumni Forums and Groups Discuss how the community platform features various forums, subgroups, or interest-based groups (e.g., procurement professionals, logistics experts, or young leaders) where alumni can have focused discussions on specific topics. Alumni Roundtables: Regularly scheduled virtual roundtable discussions on pressing industry challenges. Interest-Based Groups: Create focused groups for alumni based on shared interests like logistics, manufacturing, or technology. Career Opportunities in Supply Chain Management With the recognition of KnoWerX as the No. 1 ASCM Partner and over 32 years of experience in education and consultancy, the KnoWerX Alumni Community can provide valuable connections and resources for those seeking careers in SCM. Potential job roles include: Supply Chain Analyst: Analysing supply chain data to identify trends and areas for improvement. Logistics Coordinator: Managing the flow of goods and ensuring timely delivery. Procurement Manager: Overseeing sourcing strategies and supplier negotiations. Operations Director: Leading overall supply chain operations and strategy. Inventory Planner: Developing inventory strategies to meet customer needs while minimizing costs. The supply chain management sector is a dynamic field with a wealth of career opportunities. With the backing of KnoWerX and its extensive experience, members of the KnoWerX Alumni Community can leverage their connections and resources to excel in this crucial industry. Whether you are looking to advance your career or find top talent, our platform is designed to facilitate meaningful connections in the supply chain ecosystem. Share Your Achievements We believe in celebrating success! Share your stories and achievements within the community. Your journey can inspire others and create a culture of support and motivation. Getting Started Joining the KnoWerX Alumni Community is simple! Sign up today and start engaging with fellow alumni. Whether you’re looking for mentorship, collaboration, or job opportunities, our community is here to support you. Register yourselves on KnoWerX exclusive alumni’s community by signing up https://community.knowerx.com/start Frequently Asked Questions End Notes The KnoWerX Alumni Community is more than just a network; it’s a place to learn, grow, and connect with like-minded professionals. As a part of the elite group, you open up very rich insight access, career opportunities, and relations that will propel one to reach the pinnacle of career success. If you are looking for a gateway to knowledge, building your professional network, or taking your career in a new direction, KnoWerX Alumni Community gives you it. Don’t wait and sign up today and take the chance to be part of such a dynamic community. Unlock this potential and reach new heights by being united with industry leaders and peers. Join us today and take the next step in your professional journey! Image Reference : Freepik Disclaimer: All trademarks, logos, and brand names are the property of their respective owners. All company, product, and service names used in this website are for identification purposes only. Use of these names, trademarks, and brands does not imply endorsement.
How Supplier Relationship Management Can Boost Your Business

Mastering Supplier Relationship Management: Key Strategies & Challenges Supplier Relationship Management (SRM) is a strategic discipline that has evolved into an essential business function. It moves beyond simple procurement to encompass a broader, more collaborative approach with suppliers. Effective SRM helps organizations build long-term, mutually beneficial relationships that enable businesses to achieve sustainable success. In this detailed article, we will explore the meaning, importance, processes, types, benefits, challenges, and roles of SRM in business, and highlight how Supplier Relationship Management courses can help supply chain professionals develop their expertise. What is Supplier Relationship Management (SRM)? Supplier Relationship Management (SRM) refers to the comprehensive approach businesses use to manage their interactions with suppliers. It includes evaluating suppliers, segmenting them based on importance, and building long-term relationships that benefit both parties. The aim is to maximize the value delivered by suppliers while minimizing the risks associated with supply chain disruptions. SRM is not a transactional or short-term view of supplier interactions. Instead, it emphasizes collaboration, innovation, and partnership. By focusing on these areas, companies can secure a more resilient supply chain that supports overall business objectives, including cost reduction, faster time-to-market, and enhanced product quality. For companies that rely heavily on external suppliers for key components or services, SRM becomes a crucial pillar of their operational strategy. Historically, supplier management was often an afterthought for many businesses. Procurement teams focused on sourcing goods at the lowest possible cost, sometimes at the expense of long-term quality or relationship stability. However, with the increasing complexity of global supply chains and heightened competition, businesses are now shifting toward SRM as a way to gain competitive advantage and drive innovation. Why is Supplier Relationship Management Important? Supplier Relationship Management is crucial for a variety of reasons. As businesses increasingly depend on external suppliers for raw materials, components, and services, the quality and reliability of these suppliers directly impact the company’s success. A poor relationship with suppliers can lead to missed deadlines, poor-quality products, and increased costs, all of which can damage a business’s reputation and profitability. Here are several key reasons why SRM is important: Cost Reduction: SRM allows companies to negotiate better terms with suppliers and achieve cost efficiencies. Long-term relationships enable companies to reduce transaction costs, negotiate bulk discounts, and secure more favourable contract terms. Quality Assurance: SRM ensures that suppliers understand and adhere to quality expectations. Businesses that invest in SRM are better positioned to receive high-quality products consistently, as suppliers work more closely with the company to meet quality standards. Supply Chain Stability: A robust SRM strategy ensures that suppliers are reliable and able to deliver goods on time. This reduces the risk of disruptions in the supply chain, which can be costly and lead to production delays. Innovation and Collaboration: Suppliers are often a valuable source of innovation. Businesses that foster strong relationships with suppliers are more likely to benefit from their technological advancements and new ideas. Collaborative innovation can lead to the development of new products or processes that improve competitiveness. Risk Management: SRM helps businesses identify potential risks early and develop mitigation strategies. By working closely with suppliers, companies can anticipate and respond to issues like shortages, delays, or quality problems before they escalate into bigger problems. Competitive Advantage: Companies with strong supplier relationships are more agile and responsive to market changes. This flexibility allows them to adapt more quickly to new trends, customer demands, or economic shifts. In summary, SRM plays a critical role in ensuring a company’s operational efficiency and long-term success. Without an effective SRM strategy, businesses may struggle with inefficiencies, higher costs, and greater supply chain risks. What is the Supplier Relationship Management Process? Supplier Relationship Management is a continuous, structured process that requires careful planning and execution. The SRM process consists of several key steps designed to optimize supplier relationships and ensure both parties benefit. Here’s a breakdown of the SRM process: Supplier Segmentation: Not all suppliers require the same level of attention. The first step in SRM is to segment suppliers based on their importance to the business. Suppliers can be categorized as strategic, critical, or transactional. Strategic suppliers are those that provide essential goods or services critical to the company’s success, while transactional suppliers offer more routine products. Segmenting suppliers helps businesses allocate resources more efficiently, focusing more attention on key suppliers who offer the most value. Supplier Evaluation and Selection: Before entering into a long-term relationship, suppliers need to be evaluated based on their capabilities, reliability, financial stability, and ability to meet the company’s standards. This step involves assessing suppliers against key performance indicators (KPIs) such as delivery timelines, quality, and cost. A thorough evaluation ensures that only the most suitable suppliers are selected, which reduces the likelihood of future issues. Collaboration and Communication: Building a strong, long-term relationship requires clear, transparent, and ongoing communication. Companies should maintain regular dialogue with their suppliers to set expectations, resolve issues, and explore opportunities for collaboration. This open communication ensures that both parties are aligned in terms of goals and objectives. Performance Monitoring: Monitoring supplier performance is an ongoing process that involves tracking key metrics such as delivery times, product quality, and cost efficiency. Performance reviews help businesses identify areas for improvement and work with suppliers to address any issues Tools like scorecards and performance dashboards can be used to measure supplier performance against agreed-upon KPIs. Continuous Improvement: The final step in the SRM process is continuous improvement. Companies should work with their suppliers to identify opportunities for cost reduction, efficiency gains, and product or process innovations. By fostering a culture of continuous improvement, both the company and its suppliers can benefit from long-term success and competitive advantage. The SRM process is dynamic and should evolve as the business grows and market conditions change. By following a structured process, companies can ensure that their supplier relationships remain strong and productive. What are the Types of Supplier Relationship Management? Supplier relationships can vary based on the level of collaboration and importance to the business.
Asia’s Leading ASCM Partner: Driving Supply Chain Innovation
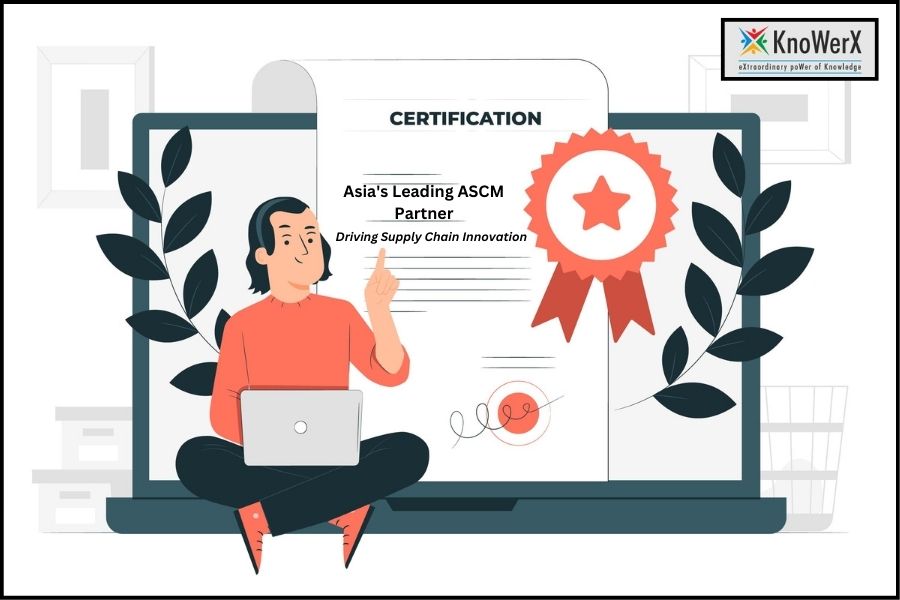
Asia’s Leading ASCM Partner: Driving Supply Chain Innovation The recent recognition of a top educational provider as the No. 1 partner in the Asia region and Worldwide by the Association for Supply Chain Management (ASCM) highlights a steadfast dedication to excellence in supply chain education. This achievement is a result of delivering comprehensive, high-quality training programs that meet the growing demands of supply chain professionals across Asia. With a focus on fostering innovation, this provider has consistently adapted its offerings to keep pace with the rapid changes in the industry. Their commitment to staying ahead of global trends has equipped learners with the skills and knowledge necessary to navigate the complexities of supply chain management, ensuring professionals are well-prepared for current and future challenges. How do You Achieve Your Goals? Dedicated to helping individuals for their SCM Goals A leading provider in supply chain management education is dedicated to helping individuals and organizations achieve their supply chain goals through tailored solutions and expert guidance. Here’s how they can support your success: Customised Training Programs: KnoWerX offers specialised courses and certifications designed to meet your specific career or organisational needs. Whether you’re looking to advance your skills or upskill your team, our programmes are tailored to deliver targeted knowledge and practical insights. Expert Guidance and Support: With a team of seasoned professionals and industry experts, KnoWerX provides mentorship and support throughout your learning journey. Flexible Learning Options: Understanding that schedules and learning preferences vary, KnoWerX provides both in-person and online training options. How Did the Leading ASCM Partner Achieve the No. 1 Recognition in the Asia Region? KnoWerX’s recent recognition as the No. 1 ASCM Partner in the Asia region reflects its dedication to offering world-class supply chain education. Through tailored programs, innovative learning techniques, and an understanding of regional market needs, we’ve empowered supply chain professionals to thrive in a competitive landscape. This award highlights our leadership in providing strategic learning that meets the demands of Asia’s growing supply chain industry. Tailored Programs: Customised training solutions designed to address specific regional needs, ensuring relevance and effectiveness. Innovative Techniques: Utilisation of modern learning methods and technologies to enhance engagement and learning outcomes. Regional Expertise: Deep understanding of Asia’s supply chain challenges and opportunities, allowing for targeted and impactful solutions. What Contributed to Becoming the World’s Top ASCM Partner? Our global recognition as the World’s Top Partner is due to several factors: The global recognition as the World’s Top Partner of ASCM is a testament to a commitment to excellence in supply chain education. With a global presence, diverse course offerings, and innovative learning models, this organization has become the preferred choice for professionals and businesses around the world. By consistently delivering impactful education and tailored solutions, they have solidified their position as a leader in supply chain management training on a global scale. Diverse Course Offerings: Comprehensive programs that cater to various levels and specialisations, providing broad learning opportunities. Global Reach: Extensive network and influence in the supply chain industry, fostering international collaborations and knowledge sharing. High Impact Solutions: Proven success in delivering transformative training and solutions worldwide, making a significant difference in global supply chains What Are the Key Factors Behind Success? The success of KnoWerX can be attributed to: Our success is built on three pillars: innovation, dedication, and partnership. KnoWerX has consistently pushed the boundaries of supply chain education by introducing cutting-edge technologies, personalized learning experiences, and a learner-first approach. Our strong partnerships with global leaders like ASCM have also allowed us to continually evolve and stay ahead of the curve in this dynamic industry. Innovation: Introduction of cutting-edge technologies and learning models, keeping our offerings at the forefront of the industry. Dedication: Commitment to delivering high-quality educational experiences, ensuring continuous improvement and client satisfaction. Partnerships: Strong collaborations with industry leaders like ASCM, enhancing our credibility and resources. How Does KnoWerX Tailor Its Programs for the Supply Chain Industry? KnoWerX customises its programs to fit industry needs by: Continuously evolving the needs of the industry, KnoWerX develops its supply chain programs to meet those requirements. Specialized certifications, training modules, and workshops tailored to every level of professional from entry-level training to advanced executive education are found in our programs. They are designed to enhance theoretical knowledge and practical skills so our learners are prepared to take on the challenges of the real world. Specialised Certifications: Offering courses that address specific supply chain roles and skills, ensuring targeted professional development. Flexible Learning Options: Providing both in-person and online training to accommodate diverse needs and learning preferences. Real-World Application: Ensuring that programs are relevant to current industry challenges, bridging the gap between theory and practice. What Role Has Innovation Played in Global Recognition? Innovation has been crucial in our global success, evident through: Innovation is at the heart of everything we do at KnoWerX. By adopting the latest technologies, offering flexible learning options, and continuously improving our curriculum, we’ve maintained our position as a leader in supply chain education. Our focus on digital transformation and integrating AI-driven solutions into our courses has set us apart from other providers, making us the go-to partner for forward-thinking supply chain professionals. Advanced Technologies: Incorporation of AI and digital tools in our training modules, enhancing learning efficiency and effectiveness. Flexible Learning Formats: Online platforms and interactive content to enhance engagement, making education accessible to a wider audience. Curriculum Updates: Regularly updating courses to include the latest industry trends and practices, keeping our offerings relevant and impactful. Long-Lasting Partnerships with Clients? Maintaining strong relationships is key to our success, achieved through: The success KnoWerX enjoys today would not be possible without the support of our clients, partners, and stakeholders. By fostering long-lasting relationships, we ensure that we deliver solutions that are not only educational but transformative. Our focus on collaboration, feedback, and continuous improvement has allowed us to maintain trust and loyalty among our clients and the industry. Collaborative Approach: Working closely with clients to tailor solutions to their needs. Feedback Integration: Continuously improving
Differences Between Demand Planning and Supply Planning
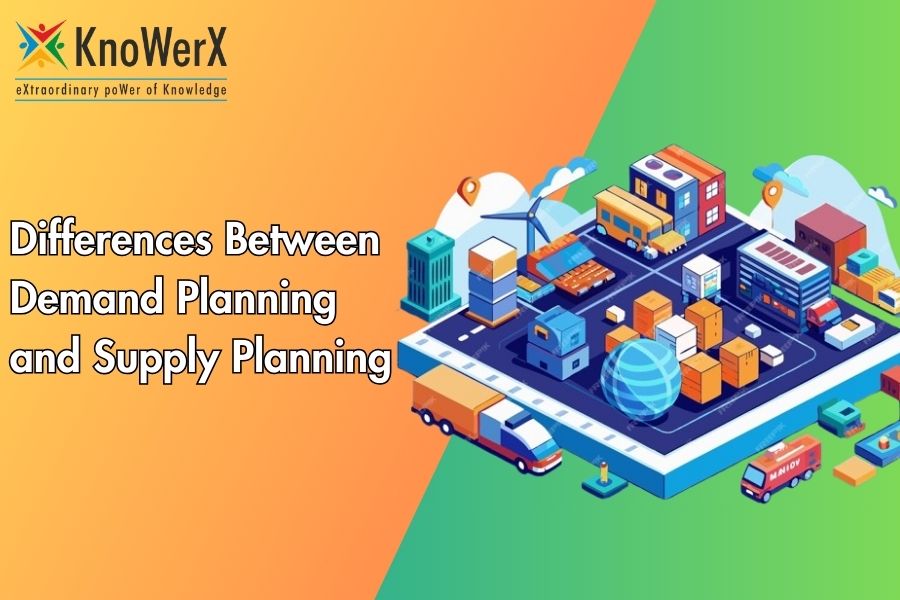
What Are the Differences Between Demand Planning and Supply Planning? Demand planning and supply planning are two fundamental processes in any supply chain management system, ensuring the successful performance of a business. Although these terms are often used interchangeably, they refer to distinct functions that complement each other. Demand planning focuses on predicting what customers will need, or what future demand might be, while supply planning ensures that products and resources are available to meet that forecasted demand. Understanding the differences between these two processes is crucial for optimizing inventory management and improving the efficiency of a company’s supply chain optimization. This article explores the core differences between demand planning and supply planning, their roles in supply chain management, and how they work together. Additionally, we will highlight the benefits of each process and explore why both are vital for businesses today. What Is Demand Planning? Demand planning refers to the process of forecasting customer demand for products or services over a specific period. It is one of the most essential corporate functions for businesses that aim to avoid costly issues such as overproduction or stockouts. Accurate customer demand forecasts allow companies to make more informed decisions about how much inventory they should maintain and when it should be replenished. Demand planning relies heavily on historical data, sales trends, and market research. Key Components of Demand Planning: Demand Forecasting: This involves predicting future customer needs using various models and techniques. Historical sales data, seasonal patterns, and external factors like economic conditions or consumer behaviour are considered in this process. Time Series Analysis: Historical sales data plays a crucial role in demand planning. By understanding past sales patterns, businesses can prepare for periods of high demand or adjust inventory levels during slower seasons. Sales Trends and Market Research: Demand planners also consider changing consumer preferences, market trends, and competitive activity to ensure they stay ahead of shifting demand. The main goal of demand planning is to ensure that businesses have the right products in stock to meet customer demand while avoiding overstocking. This reduces the risk of running out of products (stockouts) or holding excess inventory, which can lead to higher storage costs and waste. What Is Supply Planning? While demand planning predicts what customers will need in the future, supply planning ensures that businesses have the resources available to satisfy that demand. Supply planning involves the management of production schedules, procurement, and distribution of goods, and it works in conjunction with demand forecasts. Supply planners align production and operations with the forecasts developed by demand planners. Key Components of Supply Planning: Production and Procurement Management: Supply planners collaborate with production teams to ensure manufacturing processes align with demand forecasts. They also liaise with suppliers to ensure that raw materials or finished products are available as needed. Aligning Supply with Demand Forecasts: Supply planning is based on the forecasts created by demand planners. For example, if a forecast predicts higher demand for a product, supply planners ensure that resources (such as materials, labour, and equipment) are available to meet that demand without delays. Resource Optimization: Supply planners focus on efficiently utilizing resources such as labour, raw materials, and production capacity to meet demand and minimize costs. This minimizes waste and improves overall supply chain efficiency. Supply planning plays a critical role in product availability, cost minimization, and risk management within the supply chain, helping businesses reduce the disruptions associated with unforeseen demand shifts or supply chain interruptions. Differences between Demand Planning and Supply Planning Although demand planning and supply planning are interconnected, they serve different purposes within the supply chain. Understanding these differences ensures that they can be combined effectively to optimize business performance. Focus Areas: Demand Planning: Predicts future customer needs, helping businesses anticipate demand and plan accordingly. Supply Planning: Ensures that the company can meet forecasted demand through efficient production, procurement, and distribution processes. Time Horizons: Demand Planning: Typically covers longer time horizons, ranging from months to years, to predict future sales and customer behavior. Supply Planning: Operates on much shorter time horizons, typically planning weeks or months in advance, to ensure that production and inventory can keep pace with demand. Objectives: Demand Planning: Focuses on optimizing sales forecasts and maintaining stock levels that meet customer demand. Supply Planning: Focuses on producing and supplying products efficiently, minimizing costs while ensuring on-time delivery. Methodologies and Tools: Demand Planning: Demand planners use statistical forecasting models, sales data analysis, and market research to predict future demand. Supply Planning: Supply planners use tools such as production scheduling software, inventory control systems, and procurement management systems to allocate resources effectively. Benefit of Demand Planning Effective demand forecasting offers several key benefits, which contribute to business success: Improved Forecast Accuracy: Accurate demand forecasts help businesses avoid the risks of overstocking or stockouts, resulting in more efficient inventory management. Enhanced Customer Satisfaction: By anticipating customer demand, businesses can be well-prepared to meet it, leading to higher customer satisfaction and fewer missed sales opportunities. Cost Savings: Accurate forecasting helps avoid overproduction and excess inventory, reducing storage costs and minimizing waste. Effective Resource Utilization: Demand planning enables better purchasing decisions, production scheduling, and stock management, ensuring resources are used efficiently. Benefits of Supply Planning Supply planning also offers several unique benefits that contribute to operational efficiency: Minimizes Stockouts and Surplus: Supply planning reduces the risk of stockouts (which can lead to lost sales) and excess inventory (which ties up valuable resources) by aligning supply with demand. Cost Efficiency: Aligning production with demand forecasts helps businesses reduce waste, minimize labour costs, and lower material and storage expenses. Smooth Operations: Supply planning facilitates smooth operations with fewer disruptions and delays by synchronizing production schedules with demand. Risk Management: Supply planners can anticipate potential supply chain disruptions, such as raw material delays or unexpected demand spikes, and take steps to mitigate risks, ensuring business continuity. How do Demand and Supply Planning Work Together? While demand planning and supply planning differ in their objectives, they are deeply interconnected. Demand planning generates
Material Planner Role Explained: Key Duties & Required Skills
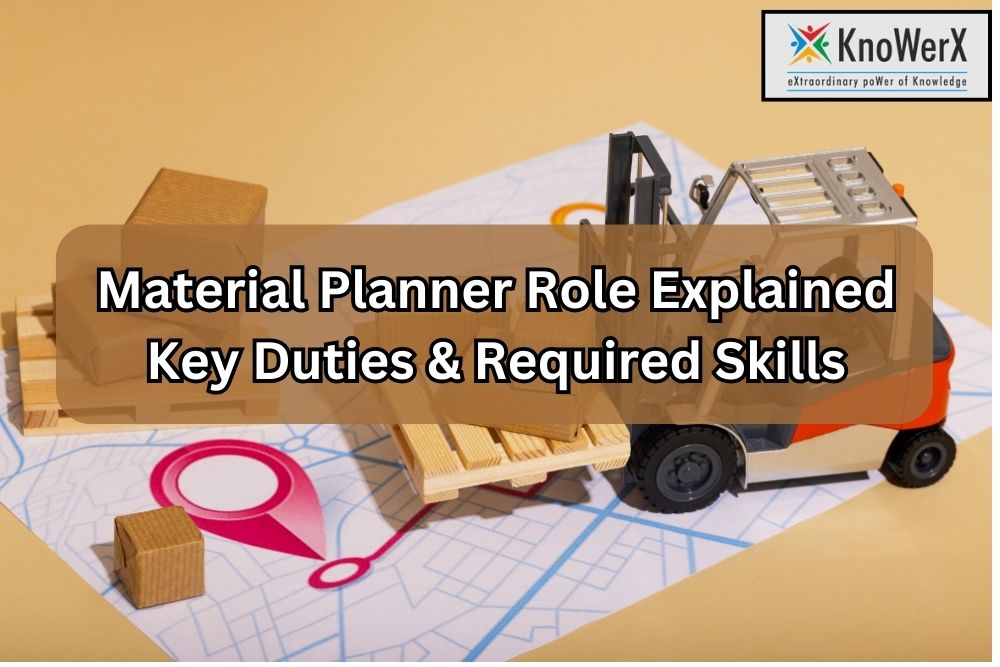
Understanding the Material Planner Role: Key Responsibilities and Skills The Material Planner Role is a vital component in the success of any manufacturing or production-oriented business. A Material Planner is responsible for ensuring that the necessary materials are available at the right time and in the right quantities to meet production demands. This role involves analysing demand forecasts, managing inventory levels, and coordinating with suppliers to prevent any disruptions in the supply chain. The Material Planner Role is crucial in supply chain management, as it directly influences production efficiency, cost management, and overall business success. Industries such as automotive, electronics, aerospace, and pharmaceuticals heavily rely on the expertise of Material Planners to maintain a smooth flow of operations, making this role indispensable across various sectors Brief Overview of the Material Planner Role: The Material Planner Role is crucial in managing the supply of materials required for production processes. By forecasting demand and coordinating with suppliers, a Material Planner ensures that materials are available when needed, preventing delays and optimizing efficiency. Importance of the Material Planner Role in Supply Chain Management: In supply chain management, the Material Planner Role is vital for balancing inventory levels and production needs. Effective material planning helps reduce costs, streamline operations, and ensure customer satisfaction. Overview of Industries Where the Material Planner Role is Essential: The Material Planner Role is essential in various industries, such as manufacturing, automotive, and electronics, where continuous production depends on a steady flow of materials. Key Responsibilities of a Material Planner Forecasting and Inventory Management: Analysing Demand Forecasts: In the Material Planner Role, analysing demand forecasts is key to maintaining optimal inventory levels. This involves ensuring materials are available without overstocking. Coordinating with Suppliers: The Material Planner Role includes coordinating with suppliers to ensure timely delivery, adjusting orders based on production schedules. Production Scheduling: Aligning Material Availability with Production Schedules: Aligning material availability with production schedules is a crucial aspect of the Material Planner Role, minimizing downtime and ensuring efficiency. Collaborating with Production Teams: Collaboration with production teams is a key part of the Material Planner Role to avoid delays and address potential material shortages. Supplier Relationship Management: Building and Maintaining Relationships: In the Material Planner Role, building and maintaining strong supplier relationships is essential for securing reliable supply chains. Strong relationships foster trust and collaboration, enabling smoother negotiations and quicker resolution of issues. These partnerships also provide leverage in times of crisis, ensuring that the supply chain remains resilient under pressure. Negotiating Contracts and Managing Supplier Performance: The Material Planner Role involves negotiating contracts and managing supplier performance to meet quality, cost, and delivery standards. Effective contract negotiation ensures favourable terms that benefit the company, while ongoing supplier management helps maintain consistency in material quality and delivery timelines. This proactive approach helps mitigate risks and enhance overall supply chain efficiency. Data Analysis and Reporting Tracking Material Usage and Predicting Future Needs: A critical part of the Material Planner Role is using data to track material usage and predict future needs, refining forecasts for better inventory management. By analysing past trends and current consumption patterns, Material Planners can anticipate potential shortages and adjust orders accordingly. This data-driven approach not only reduces waste but also optimizes inventory levels, contributing to cost savings and improved operational efficiency. Preparing Reports: The Material Planner Role includes preparing detailed reports on inventory levels, supplier performance, and production efficiency. These reports are crucial for decision-making, helping management understand current conditions and identify areas for improvement. By providing accurate and timely data, Material Planners play a key role in optimizing supply chain operations and ensuring that production targets are met efficiently. Skills and Qualifications for a Material Planner Technical Skills Proficiency in Inventory Management Software and ERP Systems: Proficiency in inventory management software is crucial in the Material Planner Role, as these tools are essential for tracking materials, managing orders, and ensuring that production schedules are met. Familiarity with ERP systems enhances the ability to integrate various supply chain functions, leading to more streamlined operations and better decision-making. Strong Analytical and Problem-Solving Skills: Analytical skills are necessary in the Material Planner Role for interpreting data and addressing supply chain challenges. A Material Planner must be able to analyze complex data sets, identify trends, and develop strategies to optimize inventory levels and prevent disruptions in production. Soft Skills Excellent Communication and Negotiation Skills: The Material Planner Role requires strong communication and negotiation skills to work effectively with suppliers, production teams, and other stakeholders. Clear communication ensures that all parties are aligned, while negotiation skills are key to securing favorable terms and resolving conflicts that may arise in the supply chain. Ability to Work Under Pressure: The ability to work under pressure is important in the Material Planner Role, where meeting tight deadlines is often necessary. Material Planners must stay focused and make quick, informed decisions in fast-paced environments, ensuring that production continues smoothly despite any challenges. Educational Background Preferred Qualifications: Preferred qualifications for the Material Planner Role include a background in supply chain management, logistics, or a related field. A solid educational foundation provides the knowledge needed to understand complex supply chain dynamics and effectively manage material flow. Certifications: Certifications like Knowerx Certified, Direct Material Planner [CDMP] add value to the Material Planner Role, demonstrating expertise in production and inventory management. These credentials not only enhance a planner’s skill set but also increase their credibility and career prospects within the industry. Challenges Faced by Material Planners Managing Supply Chain Disruptions: The Material Planner Role involves managing supply chain disruptions, such as delays and shortages, to maintain smooth operations. This requires quick decision-making and contingency planning to address unexpected issues without halting production. Proactive communication with suppliers and internal teams is essential to mitigate the impact of these disruptions. Balancing Inventory Costs with Production Needs: A significant challenge in the Material Planner Role is balancing the need to minimize inventory costs while ensuring sufficient materials for production. This requires a deep understanding of production cycles and cost management strategies
How to Improve Supply Chain Efficiency?
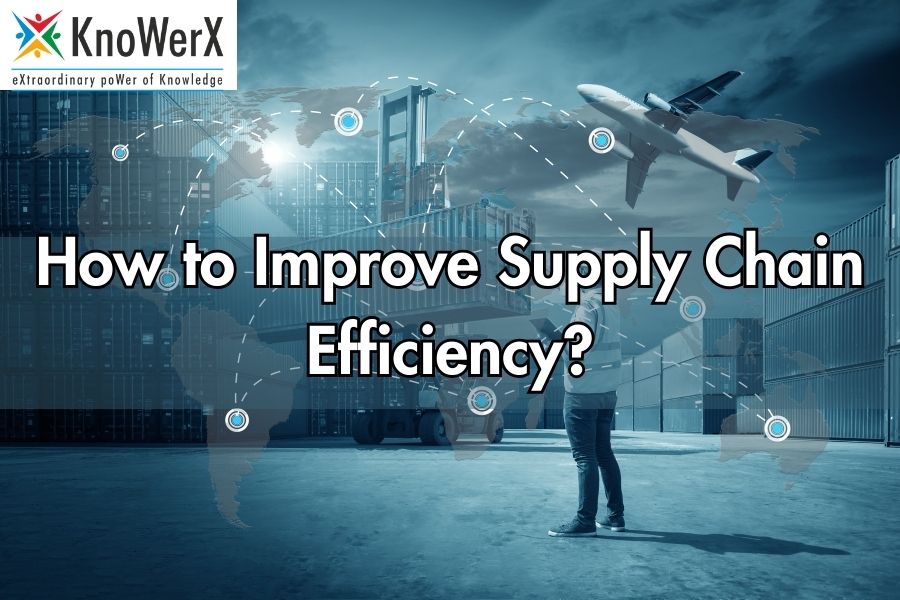
Enhance Your Supply Chain Efficiency: Effective Tips & Solutions Supply chain efficiency refers to the effectiveness with which a company manages its supply chain processes, including procurement, production, transportation, and delivery, to minimise costs and maximise productivity. At KnoWerX, we emphasise teaching the seamless integration of these processes, ensuring the timely and optimal delivery of products to customers. Efficiency in the supply chain is not solely about speed; it involves crafting a streamlined, reliable, and cost-effective system that boosts overall business performance. Importance in Today’s Business Landscape In today’s highly competitive business environment, supply chain efficiency is crucial. It directly impacts a company’s bottom line by reducing operational costs, improving customer satisfaction, and increasing overall profitability. Companies with efficient supply chains can respond more quickly to market changes, manage risks better, and maintain a competitive edge. As global markets continue to evolve, the importance of supply chain efficiency cannot be overstated. It is a key differentiator that can make or break a business. Assess Current Supply Chain Performance Key Performance Indicators (KPIs) To improve supply chain efficiency, it is essential first to assess the current performance. This can be done by tracking key performance indicators (KPIs) such as order accuracy, delivery times, inventory turnover, and supply chain costs. These metrics provide a clear picture of where the supply chain stands and highlight areas needing improvement. Common KPIs include: Order Fulfillment Cycle Time: The total time taken from receiving an order to delivering the product to the customer. Perfect Order Rate: The percentage of orders delivered without any issues, such as delays, inaccuracies, or damage. Inventory Turnover Ratio: The number of times inventory is sold and replaced over a specific period. Supply Chain Cost per Unit: The total cost incurred in the supply chain process is divided by the number of units handled. Identifying Bottlenecks and Inefficiencies Once KPIs are measured, the next step is identifying bottlenecks and inefficiencies. These can occur at various points in the supply chain, such as production delays, transportation issues, or inventory mismanagement. Identifying these problem areas is crucial for developing targeted improvement strategies. By using techniques such as process mapping and root cause analysis, businesses can uncover hidden inefficiencies and develop actionable plans to address them, thereby boosting supply chain efficiency. Implement Advanced Technology Supply Chain Management Software Advanced technology plays a significant role in enhancing supply chain efficiency. Supply chain management (SCM) software helps streamline operations by providing real-time data, improving communication, and automating various processes. This software can manage everything from procurement to delivery, ensuring a smooth flow of goods and information. Features of SCM software include: Real-Time Inventory Tracking: Monitoring inventory levels across multiple locations in real-time. Order Processing Automation: Automating order processing to reduce manual errors and speed up order fulfillment. Supplier Management: Managing supplier relationships and performance through a centralized platform. Internet of Things (IoT) and Real-Time Tracking The Internet of Things (IoT) allows for real-time tracking of products and assets throughout the supply chain. IoT devices can monitor conditions such as temperature and humidity, ensuring that goods are handled correctly. Real-time tracking also provides visibility into the movement of products, helping to prevent delays and losses. Applications of IoT in supply chain efficiency include: Asset Tracking: Using IoT sensors to monitor the location and condition of assets such as vehicles, containers, and equipment. Environmental Monitoring: Ensuring that perishable goods are stored and transported under optimal conditions. Predictive Maintenance: Using data from IoT devices to predict and prevent equipment failures before they occur. Artificial Intelligence and Predictive Analytics Artificial Intelligence (AI) and predictive analytics can analyze vast amounts of data to forecast demand, optimize inventory levels, and identify potential disruptions before they occur. These technologies enable companies to make data-driven decisions, enhancing efficiency and reducing costs. Examples of AI applications in supply chain efficiency include: Demand Forecasting: Using machine learning algorithms to predict future demand based on historical data and market trends. Inventory Optimization: Automatically adjusting inventory levels based on predicted demand and current stock levels. Risk Management: Identifying potential risks and disruptions in the supply chain and developing mitigation strategies. Optimize Inventory Management Just-in-Time (JIT) Inventory Just-in-time (JIT) inventory management reduces waste and storage costs by receiving goods only as they are needed in the production process. This approach minimizes inventory holding costs and reduces the risk of overstocking or stockouts. Implementing JIT requires close coordination with suppliers and a deep understanding of demand patterns. When done correctly, JIT can significantly enhance supply chain efficiency by aligning inventory levels with actual consumption. Demand Forecasting Techniques Accurate demand forecasting is crucial for maintaining optimal inventory levels. By using historical data, market trends, and predictive analytics, companies can anticipate customer demand more accurately, ensuring that they have the right products in the right quantities at the right time. Effective demand forecasting reduces the likelihood of stockouts and overstock situations, contributing to supply chain efficiency by optimizing inventory turnover and reducing holding costs. Supplier Relationship Management Building strong relationships with suppliers is essential for efficient inventory management. Reliable suppliers can provide high-quality materials on time, reducing production delays and ensuring a steady supply of goods. Effective supplier relationship management involves regular communication, performance reviews, and collaborative planning. By fostering strong partnerships with suppliers, companies can improve supply chain efficiency through better coordination, reliability, and responsiveness. Streamline Transportation and Logistics Route Optimization Efficient transportation is a key component of a streamlined supply chain. Route optimization software can analyse various factors such as traffic, delivery schedules, and fuel costs to determine the most efficient routes. This reduces transportation time and costs while ensuring timely deliveries. Route optimization enhances supply chain efficiency by minimizing delays and maximizing resource utilization, ultimately leading to faster and more reliable delivery of goods. Carrier Selection and Management Selecting the right carriers and managing relationships with them is critical for effective logistics. Companies should evaluate carriers based on their reliability, cost, and service quality. Regular performance assessments and maintaining open communication with carriers can help ensure consistent and efficient
Importance of Integrated Business Planning in Operations

Recognizing the Importance of Integrated Business Planning in Operations Integrated Business Planning (IBP) is a strategic management process that aligns business functions and departments to collaboratively plan and execute operational activities. The importance of Integrated Business Planning lies in its primary goal of integrating financial planning with operational planning across an organization, ensuring alignment of resources, priorities, and goals. IBP enhances decision-making by providing a holistic view of the business, enabling better forecasting, resource allocation, and risk management. It helps businesses achieve greater agility, responsiveness to market changes, and overall performance improvement. Alignment of Business Goals Integrated Business Planning (IBP) ensures alignment of strategic objectives with operational plans by coordinating activities across departments to achieve unified goals. The importance of Integrated Business Planning lies in its ability to synchronize diverse functions, such as finance, marketing, sales, operations, and supply chain, to work collaboratively towards common business objectives. Here’s how it achieves this: Strategic Alignment: IBP integrates strategic objectives into operational plans by linking long-term goals with short-term actions. This alignment ensures that day-to-day activities contribute directly to achieving broader organizational objectives. Collaborative Planning: IBP fosters collaboration across departments. It involves key stakeholders from finance, sales, marketing, supply chain, and other functions in the planning process. This collaboration ensures that everyone is working towards common objectives and understands how their activities impact overall performance. Resource Optimization: By coordinating activities and aligning goals, IBP helps optimize resource allocation. It ensures that resources such as finances, personnel, and materials are deployed efficiently to support strategic priorities. Enhanced Decision-Making Importance of Integrated Business Planning (IBP) enhances decision-making by leveraging real-time data and improving forecasting accuracy and risk management in the following ways. Real-Time Data Utilization: IBP integrates real-time data from various sources across the organization, such as sales figures, inventory levels, and market trends. This allows decision-makers to have up-to-date information to base their decisions on, rather than relying on outdated or incomplete data. Improved Forecasting: IBP incorporates advanced forecasting techniques and algorithms to predict future demand, sales trends, and resource needs more accurately. By analysing historical data and market insights in real-time, IBP helps organizations anticipate changes and make proactive decisions to meet customer demands effectively. Risk Management: IBP enhances risk management by identifying potential risks early and developing strategies to mitigate them. It allows organizations to assess the impact of various scenarios on their operations and financial performance, thereby improving resilience and preparedness against uncertainties. Optimized Resource Allocation Integrated Business Planning (IBP) optimizes resource allocation by ensuring efficient use of financial, human, and material resources, thereby reducing wastage and enhancing productivity. Here’s how IBP achieves this: Financial Resource Allocation: IBP aligns financial planning with operational goals, ensuring that budgets are allocated strategically to support priority initiatives. By integrating financial forecasts with operational plans, IBP helps organizations allocate funds where they are most needed, avoiding overspending or underspending in different areas. Human Resource Optimization: IBP involves workforce planning based on anticipated demand and business priorities. It ensures that the right talent is deployed in the right roles at the right time, optimizing employee productivity and satisfaction. Additionally, IBP facilitates workforce development initiatives aligned with organizational goals, enhancing skills and capabilities where necessary. Material Resource Management: IBP improves inventory management and procurement processes by aligning them with demand forecasts and production schedules. It helps organizations maintain optimal inventory levels to meet customer demand while minimizing carrying costs and stockouts. By integrating supply chain planning with sales and operations, IBP reduces inefficiencies in material handling and logistics. Enhanced Productivity: By optimizing resource allocation across financial, human, and material dimensions, IBP enhances overall productivity. It ensures that resources are used efficiently to achieve maximum output and deliver value to customers and stakeholders. Moreover, IBP fosters a culture of continuous improvement and accountability, where resources are managed responsibly to drive sustainable growth and profitability. Improved Collaboration The Importance of Integrated Business Planning (IBP) lies in its ability to improve collaboration by promoting cross-functional communication and breaking down silos between departments, fostering integrated workflows across the organization. Here’s how IBP enhances collaboration. Cross-Functional Communication: IBP involves key stakeholders from various departments, including finance, sales, marketing, supply chain, and operations, in the planning and decision-making processes. This cross-functional collaboration ensures that different perspectives are considered, fostering a more comprehensive understanding of business needs and objectives. Shared Goals and Objectives: IBP aligns all departments towards common goals and objectives. By integrating strategic and operational planning, IBP ensures that everyone understands their role in achieving organizational success. This shared understanding promotes teamwork and collective accountability across the organization. Information Sharing: IBP facilitates the sharing of information and data across departments in real-time. This transparency enables teams to access relevant insights and collaborate more effectively on projects and initiatives. It reduces the likelihood of misunderstandings or conflicting priorities, promoting smoother workflows and faster decision-making. Agility and Responsiveness The importance of Integrated Business Planning (IBP) lies in its ability to enhance agility and responsiveness within organizations. IBP enables organizations to adapt swiftly to market changes and disruptions, facilitating quick responses to customer demands and market shifts. Here’s how IBP achieves this. Real-Time Data and Insights: IBP leverages real-time data from various sources, providing organizations with up-to-date insights into market conditions, customer behaviour, and internal operations. This timely information allows businesses to quickly identify emerging trends and make informed decisions to stay ahead of the competition. Scenario Planning and Analysis: IBP supports scenario planning, allowing organizations to model different potential outcomes based on various assumptions and variables. By simulating different scenarios, businesses can prepare for potential market shifts and disruptions, developing contingency plans to mitigate risks and capitalize on opportunities. Flexible Planning Processes: Importance of Integrated Business Planning (IBP) promotes flexible and iterative planning processes that can be adjusted as needed. This flexibility enables organizations to pivot quickly in response to changing market conditions, ensuring that plans remain relevant and effective even in dynamic environments. Aligned and Collaborative Teams: With IBP, cross-functional teams are aligned and work collaboratively towards shared goals. This alignment