The Shocking Impact of Bad Customer Relationships on Supply Chains
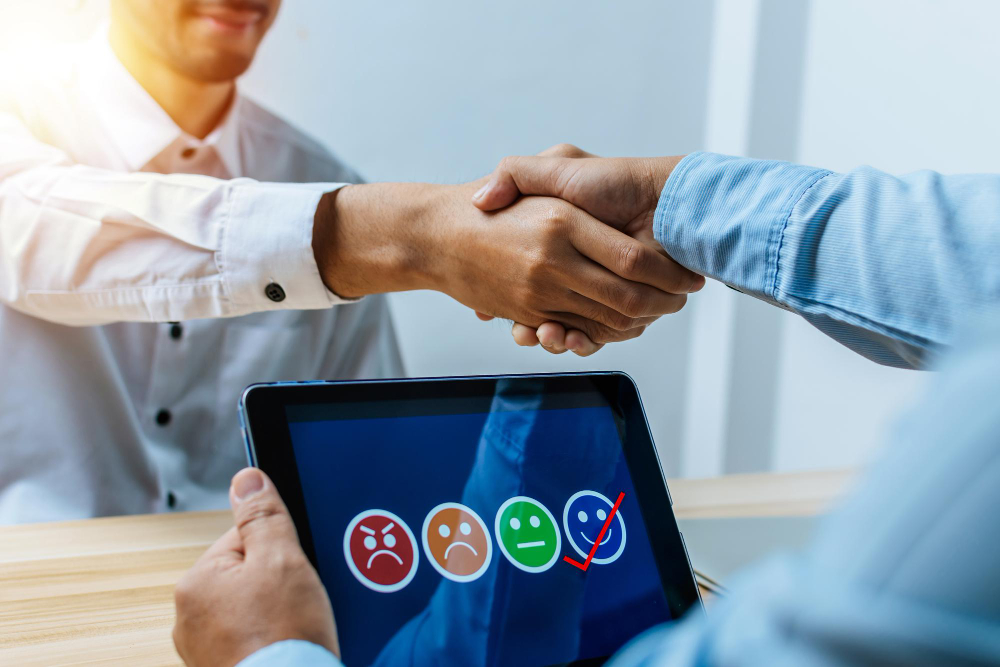
The Shocking Impact of Bad Customer Relationships on Supply Chains In the modern business landscape, customer relationships play a crucial role in the efficiency and success of supply chain management. Poor customer relationships can lead to operational inefficiencies, financial setbacks, and long-term damage to brand reputation. When businesses fail to maintain strong ties with their customers, they risk disruptions that can impact inventory management, delivery timelines, and overall profitability. Understanding the challenges of bad customer relationships and implementing strategies to strengthen them can significantly enhance supply chain performance. This article explores the negative consequences of weak customer relationships, provides strategies to improve them, and highlights the benefits of building long-term, trust-based connections with customers. The Negative Impact of Bad Customer Relationships on Supply Chains Reduced Trust and Reliability – Trust is the foundation of any successful customer relationship. When customers lose trust in suppliers due to inconsistent service or delayed responses, they may seek alternatives. This not only affects revenue but also complicates demand forecasting, leading to inventory mismanagement. Inefficient Inventory Management – Poor communication with customers results in unclear demand signals, causing either overstocking or stock shortages. Misalignment between suppliers and customers can also lead to delays in order fulfillment, impacting supply chain efficiency. Disruptions in the Supply Chain Flow – Late payments, disputes over product quality, and unresolved conflicts can create bottlenecks in the supply chain. These disruptions may lead to frequent order cancellations and delayed shipments, affecting overall business performance. Damage to Brand Reputation – Unhappy customers often share negative experiences, which can damage a company’s reputation. Losing valuable business partnerships due to poor customer relationships weakens market credibility and reduces future opportunities. Increased Operational Costs – Resolving customer complaints and disputes requires extra resources, increasing operational expenses. High return rates and frequent order modifications further drive up logistics and handling costs, reducing profit margins. Key Strategies to Improve Customer Relationships in SCM Enhance Communication & Transparency – Effective communication is essential for maintaining healthy customer relationships. Keeping customers informed about order status, shipment tracking, and potential delays fosters trust. Using Customer Relationship Management (CRM) systems can help streamline interactions and enhance transparency. Build Trust Through Consistency – Providing reliable and high-quality service ensures customer satisfaction. Consistency in product availability, delivery timelines, and service standards helps build long-term customer relationships. Improve Responsiveness & Support – Quickly addressing customer concerns shows commitment to their needs. Having a dedicated customer support team and implementing automated support tools for real-time updates can significantly improve customer relationships. Strengthen Collaboration & Engagement – Regular interactions with customers help align supply chain goals. Gathering feedback and implementing improvements based on customer insights fosters mutual trust and long-term partnerships. Leverage Technology for Better Customer Experience – Utilizing AI-driven forecasting tools helps align inventory levels with customer demand. Implementing cloud-based supply chain solutions ensures smoother operations and better service delivery, strengthening customer relationships. Benefits of Strong Customer Relationships in SCM Improved Demand Forecasting – Understanding customer preferences and needs allows businesses to optimize inventory levels and reduce waste, improving overall efficiency. By analysing purchasing trends and customer feedback, companies can anticipate demand fluctuations more accurately and make data-driven decisions. Greater Supply Chain Resilience – Strong customer relationships ensure better coordination during supply chain disruptions, allowing businesses to navigate challenges more effectively. With proactive communication and collaboration, companies can implement contingency plans swiftly, minimising operational downtime. Increased Customer Loyalty & Retention – Satisfied customers are more likely to continue business and recommend the company to others, creating a loyal customer base. Consistently delivering high-quality service and personalised experiences strengthens trust and encourages long-term engagement. Enhanced Financial Performance – Maintaining good customer relationships leads to steady revenue streams, reduced costs, and improved profitability. Loyal customers contribute to higher lifetime value, while efficient customer service reduces expenses associated with acquisition and churn. Stronger Competitive Advantage – Businesses with well-maintained customer relationships outperform competitors by offering superior service and customer satisfaction. By prioritising customer needs and feedback, companies can differentiate themselves in the market and build a strong brand reputation. Frequently Asked Questions Ending Notes Building and maintaining strong customer relationships is crucial for a seamless and efficient supply chain. Poor customer relationships lead to inefficiencies, disruptions, and financial setbacks, whereas effective relationship management fosters trust, reduces operational costs, and enhances long-term growth. At KnoWerX, we offer industry-leading training programs to help professionals master best practices in supply chain management. Strengthen your customer relationships today by leveraging the right strategies and tools. Image Reference: Freepik Disclaimer: All trademarks, logos, and brand names are the property of their respective owners. All company, product, and service names used in this website are for identification purposes only. Use of these names, trademarks, and brands does not imply endorsement.
How Integrated Business Planning Drives Growth
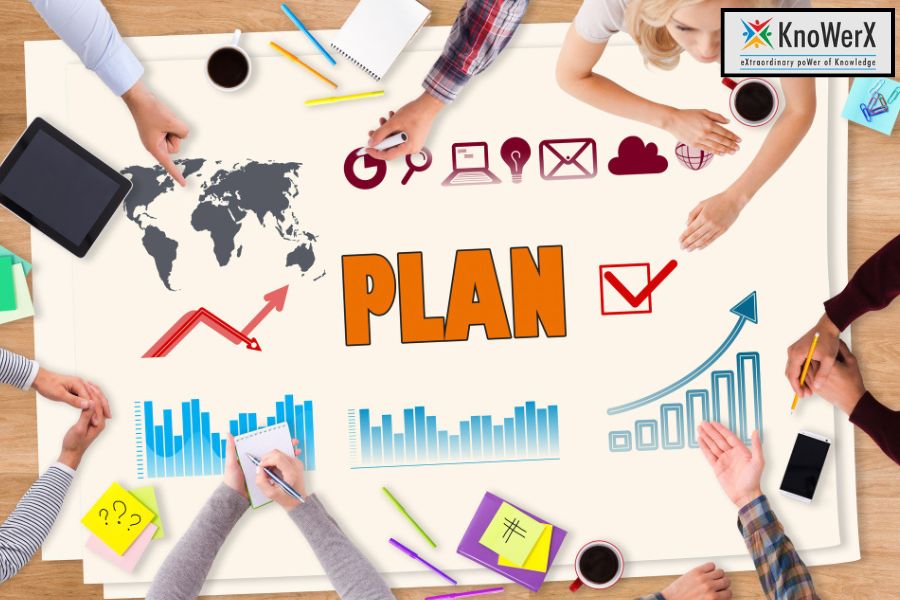
How Integrated Business Planning Drives Growth In today’s fast-paced business environment, Integrated Business Planning (IBP) has emerged as a critical strategy for driving growth, improving efficiency, and ensuring long-term success. At KnoWerX, we understand the transformative power of IBP, and through our industry-leading Supply Chain Management Training, we equip professionals with the tools and knowledge to harness its potential. Here are some actionable tips to help you leverage Integrated Business Planning for sustainable growth: 1. Align Organizational Goals with Operational Plans Integrated Business Planning ensures that all departments—sales, finance, operations, and supply chain—work in harmony toward common objectives. By aligning your organizational goals with operational plans, you can eliminate silos, improve collaboration, and drive growth. This alignment also helps in creating a unified vision, ensuring that every team member understands their role in achieving the company’s strategic goals. 2. Leverage Data-Driven Decision-Making One of the core principles of Integrated Business Planning is using accurate, real-time data to make informed decisions. Invest in advanced analytics tools and train your teams to interpret data effectively. This will help you anticipate market changes, optimize resources, and stay ahead of the competition. Additionally, data-driven insights enable proactive decision-making, reducing risks and enhancing overall business agility. 3. Focus on Demand Planning and Forecasting Accurate demand planning is a cornerstone of Integrated Business Planning. By understanding customer needs and market trends, you can optimize inventory levels, reduce waste, and improve customer satisfaction. KnoWerX’s Supply Chain Management Training programs emphasize the importance of demand planning in achieving business growth. Effective forecasting also minimizes overproduction and stockouts, ensuring a balanced supply chain. 4. Enhance Cross-Functional Collaboration Integrated Business Planning thrives on collaboration. Encourage open communication and shared accountability across departments. This not only improves efficiency but also fosters innovation, as diverse perspectives come together to solve challenges. Regular cross-functional meetings and shared performance metrics can further strengthen teamwork and alignment. 5. Adopt a Continuous Improvement Mindset Growth is an ongoing process, and Integrated Business Planning is no exception. Regularly review your plans, identify areas for improvement, and adapt to changing business conditions. KnoWerX’s training programs emphasize the importance of continuous learning and improvement in achieving excellence. By embracing a culture of continuous improvement, you can stay competitive and responsive to market dynamics. 6. Invest in Training and Skill Development To fully realize the benefits of Integrated Business Planning, your team needs the right skills and knowledge. KnoWerX offers Professional Training programs designed to empower professionals with the latest tools, techniques, and best practices in IBP and supply chain management. Upskilling your workforce ensures they are equipped to handle complex planning processes and drive organizational success. 7. Monitor Key Performance Indicators (KPIs) Track the right KPIs to measure the success of your Integrated Business Planning efforts. Metrics like inventory turnover, forecast accuracy, and customer satisfaction can provide valuable insights into your performance and highlight areas for improvement. Regularly analyzing these KPIs helps in making data-backed adjustments to your strategies, ensuring sustained growth. 8. Embrace Technology and Automation Modern IBP relies heavily on technology. Implement integrated software solutions that streamline planning processes, enhance visibility, and improve decision-making. KnoWerX’s training programs can help your team stay updated on the latest technological advancements in the field. Automation tools can also reduce manual errors, saving time and resources while improving accuracy. 9. Build a Resilient Supply Chain A robust supply chain is essential for effective Integrated Business Planning. Focus on building flexibility and resilience to handle disruptions and capitalize on opportunities. KnoWerX’s expertise in supply chain management can guide you in creating a supply chain that supports your growth objectives. A resilient supply chain ensures continuity, even in the face of unforeseen challenges. 10. Partner with Experts for Guidance Implementing Integrated Business Planning can be complex, but you don’t have to do it alone. Partner with industry leaders like KnoWerX to gain access to expert guidance, tailored training programs, and practical insights that drive results. Our experienced trainers and consultants can help you navigate the complexities of IBP, ensuring a smooth and successful implementation. Ending Notes At KnoWerX, we are committed to helping professionals like you achieve excellence through Integrated Business Planning and Supply Chain Management Training. With over 32 years of collective experience, we have trained and consulted for some of the largest companies in India and abroad. Let us empower you with the knowledge and skills to drive growth and success in your organization. Image Reference: Freepik Disclaimer: All trademarks, logos, and brand names are the property of their respective owners. All company, product, and service names used in this website are for identification purposes only. Use of these names, trademarks, and brands does not imply endorsement.
Certified in Inventory Management: Is It Worth It?
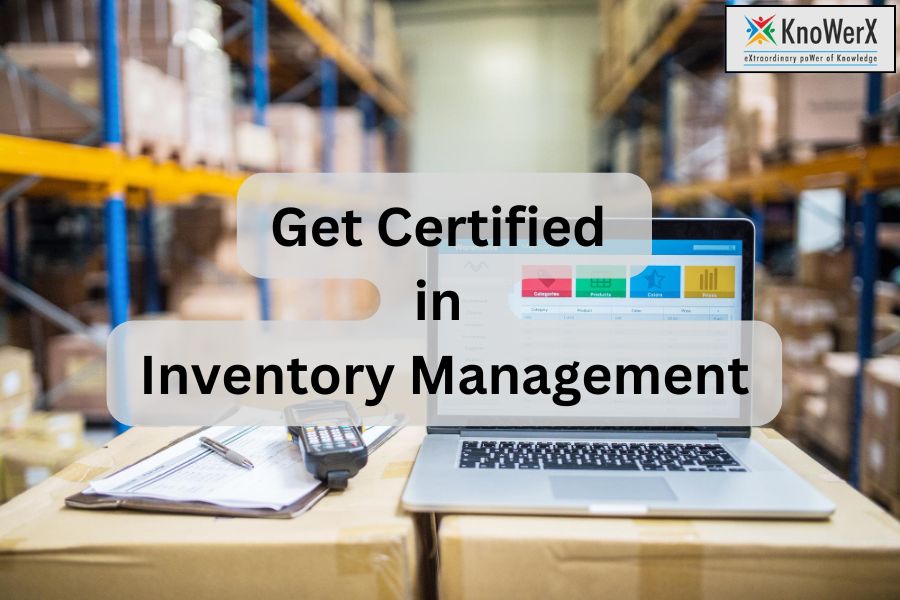
Certified in Inventory Management: Is It Worth It? Inventory management is a critical component of supply chain operations, and earning an Inventory Management Certification can significantly enhance your professional capabilities. At KnoWerX, we are committed to empowering professionals with the knowledge and skills needed to excel in this domain. Here are some compelling reasons why you should consider getting certified in inventory management: 1. Boost Your Career Prospects An Inventory Management Certification validates your expertise and makes you stand out in a competitive job market. Employers value certified professionals as they bring proven skills and knowledge to the table, ensuring efficient inventory control and cost savings. With certification, you can qualify for roles like Inventory Manager, Supply Chain Analyst, or Logistics Coordinator. It also demonstrates your commitment to continuous learning, making you a preferred candidate for promotions and leadership positions. 2. Gain In-Depth Knowledge Certification programs, like those offered by KnoWerX, provide comprehensive training on inventory management best practices, tools, and techniques. You’ll learn how to optimize stock levels, reduce waste, and improve supply chain efficiency. The curriculum covers essential topics such as demand forecasting, inventory valuation, and warehouse management. This knowledge equips you to handle real-world challenges with confidence and precision. 3. Enhance Your Problem-Solving Skills Inventory management involves tackling challenges like stockouts, overstocking, and demand forecasting. With an Inventory Management Certification, you’ll acquire the analytical and strategic skills needed to address these issues effectively. You’ll learn to use advanced tools and software to analyze data, identify trends, and make informed decisions. These skills are invaluable for minimizing risks and maximizing operational efficiency. 4. Stay Ahead of Industry Trends The supply chain industry is constantly evolving, and staying updated is crucial. KnoWerX’s certification programs are designed to keep you abreast of the latest trends, technologies, and methodologies in inventory management. From automation to AI-driven inventory systems, our courses ensure you’re well-versed in cutting-edge advancements. This knowledge helps you adapt to changes and maintain a competitive edge in your career. 5. Increase Your Earning Potential Certified professionals often command higher salaries due to their specialized skills. An Inventory Management Certification can open doors to better-paying roles and career advancement opportunities. Employers recognize the value of certified individuals in driving cost savings and operational efficiency, making them willing to offer competitive compensation packages. 6. Build Credibility and Trust Certification from a reputable institution like KnoWerX adds credibility to your profile. It demonstrates your commitment to professional growth and your ability to handle complex inventory management tasks. This trust extends to employers, colleagues, and stakeholders, who will rely on your expertise to make critical decisions. It also enhances your professional reputation in the industry. 7. Learn from Industry Experts With over 32 years of collective experience, KnoWerX’s trainers bring real-world insights and practical knowledge to the table. Our programs are designed by professionals who have consulted and trained large companies globally. You’ll gain insights from case studies, real-life scenarios, and hands-on exercises that prepare you for the challenges of inventory management. This practical approach ensures you’re job-ready from day one. 8. Access to a Global Network By enrolling in KnoWerX’s certification programs, you’ll join a community of like-minded professionals. This network can be invaluable for sharing knowledge, exploring opportunities, and staying connected with industry leaders. Networking with peers and experts can open doors to collaborations, mentorship, and career growth. It also keeps you informed about global trends and best practices. 9. Improve Organizational Efficiency Certified professionals are equipped to streamline inventory processes, reduce costs, and improve overall supply chain performance. This makes you an asset to any organization. By implementing efficient inventory management strategies, you can help your company achieve better customer satisfaction, reduced lead times, and increased profitability. 10. Affordable and High-Quality Education KnoWerX is committed to providing the best quality education at the most competitive prices in the industry. Our Inventory Management Certification programs are designed to offer maximum value for your investment. With flexible learning options and expert-led training, we ensure that you receive world-class education without breaking the bank. Our goal is to make professional growth accessible to everyone. Frequently Asked Questions Ending Notes Earning an Inventory Management Certification is a strategic move for any supply chain professional looking to enhance their skills, advance their career, and contribute to organizational success. At KnoWerX, we are dedicated to helping you achieve your goals through our industry-leading training programs. Take the first step toward professional excellence today with KnoWerX’s Inventory Management Certification and unlock new opportunities in the dynamic world of supply chain management! Image Reference: Freepik Disclaimer: All trademarks, logos, and brand names are the property of their respective owners. All company, product, and service names used in this website are for identification purposes only. Use of these names, trademarks, and brands does not imply endorsement.
The Key to Efficient Operations | Warehouse Management
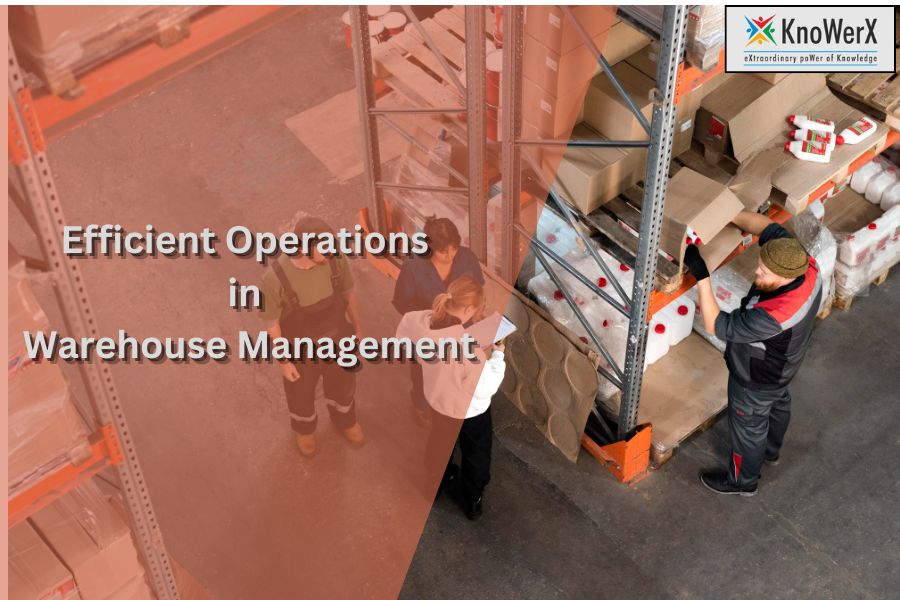
The Key to Efficient Operations: Warehouse Management Efficient warehouse management is the backbone of a successful supply chain. It ensures seamless operations, reduces costs, and enhances customer satisfaction. At KnoWerX, we understand the critical role of warehouse management in driving operational excellence. With over 33 years of collective experience in supply chain management training, certification and consultancy, we bring you actionable tips to optimize your warehouse operations. 1. Leverage Technology Invest in advanced Warehouse Management Systems (WMS) to automate processes, track inventory in real-time, and improve accuracy. Technology-driven warehouse management reduces human errors and enhances productivity. Integrate tools like RFID, IoT, and automation to streamline operations further. These technologies provide real-time visibility into inventory levels, helping you make data-driven decisions. By embracing digital transformation, you can future-proof your warehouse management processes and stay competitive in the industry. 2. Optimize Layout and Space Utilization A well-organized warehouse layout is key to efficient operations. Design your warehouse to minimize travel time, ensure easy access to high-demand items, and maximize storage capacity. Effective space utilization is a cornerstone of successful warehouse management. Use vertical space with mezzanines or taller racks to store more inventory without expanding your footprint. Regularly review and adjust your layout based on seasonal demand or changes in product lines. A dynamic layout ensures your warehouse management strategy remains agile and responsive to business needs. 3. Implement Inventory Control Measures Accurate inventory management is critical for warehouse efficiency. Use techniques like ABC analysis to prioritize high-value items and maintain optimal stock levels. Regular audits and cycle counting can further streamline warehouse management processes. Adopt just-in-time (JIT) inventory practices to reduce carrying costs and minimize waste. Implement barcode or QR code systems to track inventory movements accurately. These measures not only improve warehouse management but also enhance overall supply chain efficiency. 4. Train Your Workforce Your warehouse staff plays a vital role in operational success. Provide regular training on best practices, safety protocols, and the use of technology. At KnoWerX, we offer professional training programs to equip your team with the skills needed for effective warehouse management. Encourage cross-training to ensure flexibility and adaptability among your workforce. A well-trained team can handle peak seasons, unexpected challenges, and new technologies with ease. Investing in your employees is a key aspect of sustainable warehouse management. 5. Adopt Lean Principles Incorporate lean methodologies to eliminate waste, reduce downtime, and improve workflow. Lean warehouse management focuses on continuous improvement and operational efficiency. Identify and eliminate non-value-added activities, such as unnecessary movement or overproduction. Use tools like 5S (Sort, Set in Order, Shine, Standardize, Sustain) to maintain an organized and efficient workspace. Lean principles ensure your warehouse management processes are both cost-effective and productive. 6. Enhance Order Fulfilment Processes Streamline picking, packing, and shipping processes to ensure timely and accurate order fulfilment. Efficient management ensures customer satisfaction and builds brand loyalty. Use batch picking or zone picking strategies to reduce travel time and increase order processing speed. Implement automated sorting systems to handle high volumes during peak seasons. By optimizing order fulfilment, you can meet customer expectations and improve your bottom line. 7. Monitor Key Performance Indicators (KPIs) Track KPIs such as order accuracy, inventory turnover, and carrying costs to measure warehouse performance. Data-driven insights help identify areas for improvement in your warehouse management strategy. Set benchmarks and regularly review performance against these metrics. Use dashboards and reporting tools to visualize data and make informed decisions. Monitoring KPIs ensures your warehouse management processes are aligned with business goals and deliver measurable results. 8. Prioritize Safety and Compliance A safe warehouse is an efficient warehouse. Implement safety measures, conduct regular inspections, and ensure compliance with industry regulations. Safety is an integral part of effective warehouse management. Train employees on proper equipment handling and emergency procedures. Regularly inspect racks, forklifts, and other equipment to prevent accidents. A safe work environment not only boosts morale but also reduces downtime and liability risks, making safety a critical component of warehouse management. 9. Challenges in Warehouse Management Common Obstacles in Warehouse Management Warehouse management faces several challenges, including supply chain disruptions due to delays, global crises, or demand fluctuations. Additionally, labor shortages can affect operations, causing slower processes and errors, while equipment malfunctions or technology integration issues can halt productivity, further complicating management. Solutions to Overcome These Challenges and Stay Efficient To mitigate these obstacles, warehouses can invest in automation and real-time tracking to reduce reliance on manual labor, ensuring continuous operations even during shortages. Collaborating with multiple suppliers and implementing inventory buffer systems can help combat supply chain disruptions. Additionally, regular maintenance and updates to equipment and technology are crucial for smooth operations. Frequently Asked Questions Ending Notes Efficient management is not just about storing goods; it’s about creating a streamlined, cost-effective, and customer-centric operation. With KnoWerX’s expertise in supply chain management training, you can unlock the full potential of your warehouse operations. Join our professional training programs today and take the first step toward mastering warehouse management. Let KnoWerX be your partner in achieving operational excellence and professional growth! Image Reference: Freepik Disclaimer: All trademarks, logos, and brand names are the property of their respective owners. All company, product, and service names used in this website are for identification purposes only. Use of these names, trademarks, and brands does not imply endorsement.
Know Importance of Relationships in the Supply Chain
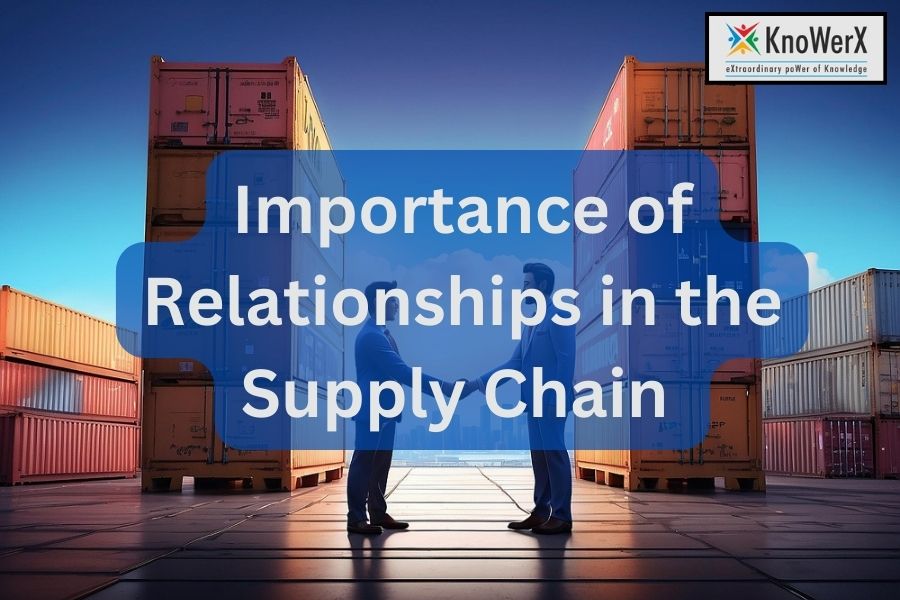
Know Importance of Relationships in the Supply Chain Strong supply chain relationships are the backbone of efficient logistics, cost savings, and business success. A well-connected network of suppliers, vendors, and distributors ensures smooth operations, minimises risks, and enhances overall efficiency. Here are some key tips to build and maintain effective relationships in your supply chain: 1. Prioritise Communication & Transparency Clear, open communication fosters trust and ensures smooth collaboration between suppliers, manufacturers, and distributors. Regular updates and honest feedback can help prevent disruptions and improve overall efficiency. Using digital communication tools, such as supplier portals and real-time tracking systems, enhances visibility across the supply chain. Businesses that prioritise transparent reporting and data sharing build stronger, more resilient supply chain relationships. 2. Foster Long-Term Partnerships Rather than focusing solely on short-term gains, investing in long-term supplier and vendor relationships leads to better negotiations, improved service levels, and shared growth opportunities. A committed partnership encourages suppliers to provide better pricing, innovation, and quality improvements. Consistently working with trusted partners reduces risks, strengthens market position, and enhances supply chain stability. 3. Leverage Technology for Better Collaboration Using digital platforms, such as cloud-based supply chain management systems, improves visibility, coordination, and real-time data sharing. Technology enables automated order tracking, predictive analytics, and demand forecasting, reducing inefficiencies. Companies that embrace digital transformation in supply chain relationships gain a competitive edge by improving speed, accuracy, and cost-effectiveness. 4. Establish Mutual Goals & Expectations Aligning objectives between partners ensures that all stakeholders work towards common business goals. Clearly defined key performance indicators (KPIs) and service level agreements (SLAs) help maintain accountability and track progress. Regular performance reviews and joint strategy meetings can further enhance coordination, ensuring all parties contribute to shared success. 5. Invest in Supplier & Vendor Development Training and development initiatives for suppliers and vendors create a stronger, more reliable supply chain. Providing access to best practices, industry certifications, and process improvements can help partners enhance their efficiency and capabilities. A well-trained supplier base improves product quality, reduces defects, and enhances overall customer satisfaction, strengthening long-term supply chain relationships. 6. Manage Risks Collaboratively Uncertainties like market fluctuations, geopolitical factors, and natural disasters impact supply chains. A proactive approach to risk management, including joint contingency planning with partners, ensures minimal disruptions. Developing alternative sourcing strategies, maintaining buffer stocks, and sharing risk mitigation plans with stakeholders strengthen overall supply chain resilience. 7. Encourage Ethical & Sustainable Practices Ethical sourcing, fair trade, and sustainability initiatives contribute to long-lasting supply chain relationships. Businesses that prioritise social responsibility build a positive brand reputation and attract environmentally conscious consumers. Implementing sustainable packaging, reducing carbon footprints, and ensuring ethical labour practices help foster trust and long-term partnerships. Frequently Asked Questions Ending Notes Building strong supply chain relationships is crucial for operational efficiency, cost optimisation, and long-term business success. Companies that focus on communication, collaboration, and innovation create a more resilient and competitive supply chain. At KnoWerX, we equip professionals with the expertise to master supply chain relationships through our industry-leading training programs and certifications. Strengthen your knowledge with us and drive your supply chain success! Image Reference: Freepik Disclaimer: All trademarks, logos, and brand names are the property of their respective owners. All company, product, and service names used in this website are for identification purposes only. Use of these names, trademarks, and brands does not imply endorsement.
Grow Your Business: Align Supply and Demand Effectively
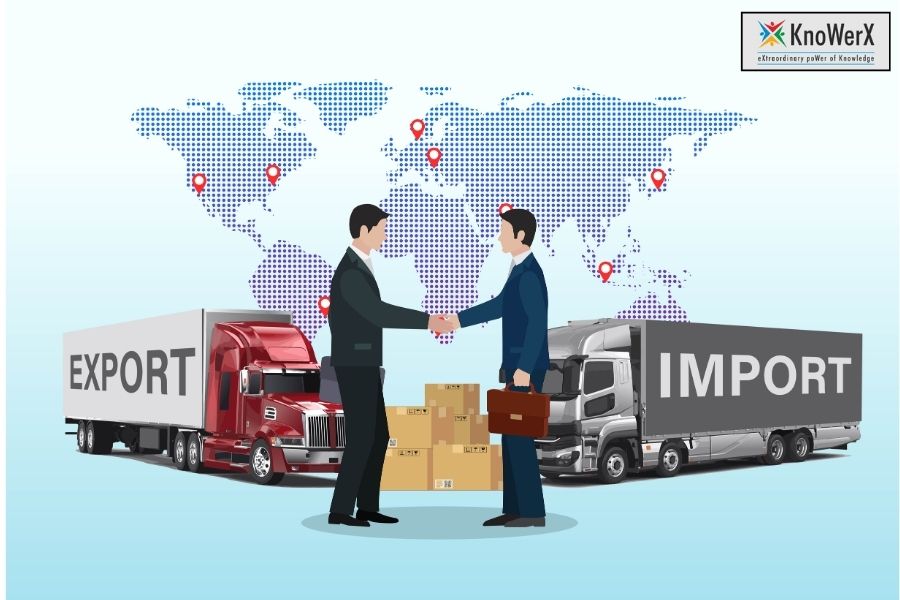
Grow Your Business: Align Supply and Demand Effectively In today’s dynamic business environment, achieving supply and demand alignment is critical for sustainable growth. As an industry leader in Supply Chain Management Training, KnoWerX brings you actionable strategies to help professionals and organizations optimize their operations and drive success. Here are some expert tips to master supply and demand alignment: Leverage Data Analytics for Accurate Forecasting Accurate demand forecasting is the cornerstone of supply and demand alignment. Utilize advanced data analytics tools to analyze historical data, market trends, and customer behavior. This will help you predict demand more precisely and align your supply chain accordingly. Importance: Data-driven insights reduce guesswork and improve decision-making. Actionable Tip: Invest in predictive analytics software to stay ahead of demand fluctuations. Adopt Agile Supply Chain Practices Agility is key to responding to fluctuations in demand. Implement flexible supply chain processes that allow you to scale up or down quickly. This ensures that your supply chain remains aligned with changing market demands. Importance: Agile practices minimize disruptions and improve responsiveness. Actionable Tip: Use real-time monitoring tools to adapt to sudden changes in demand. Enhance Collaboration Across Departments Supply and demand alignment requires seamless collaboration between sales, marketing, procurement, and operations teams. Foster open communication and shared goals to ensure everyone is working toward the same objectives. Importance: Cross-functional collaboration eliminates silos and improves efficiency. Actionable Tip: Conduct regular inter-departmental meetings to align strategies. Invest in Technology and Automation Modern supply chain technologies, such as AI and IoT, can significantly improve supply and demand alignment. Automate repetitive tasks, monitor inventory in real-time, and optimize logistics to reduce inefficiencies and meet demand effectively. Importance: Automation enhances accuracy and reduces operational costs. Actionable Tip: Implement AI-powered tools for demand forecasting and inventory management. Focus on Inventory Optimization Maintaining the right balance of inventory is crucial. Overstocking leads to increased costs, while understocking results in lost sales. Use inventory management tools to ensure optimal stock levels and align them with demand patterns. Importance: Optimized inventory reduces waste and improves profitability. Actionable Tip: Adopt a just-in-time (JIT) inventory system to minimize excess stock. Build Strong Supplier Relationships A reliable supplier network is essential for supply and demand alignment. Develop strong partnerships with suppliers to ensure timely deliveries, negotiate better terms, and mitigate risks associated with supply chain disruptions. Importance: Strong supplier relationships enhance reliability and reduce risks. Actionable Tip: Establish long-term contracts with key suppliers for better collaboration. Monitor Market Trends and Customer Preferences Stay ahead of the curve by keeping a close eye on market trends and evolving customer preferences. This proactive approach will help you anticipate changes in demand and adjust your supply chain strategies accordingly. Importance: Market awareness ensures you remain competitive and relevant. Actionable Tip: Use social media and customer feedback to track emerging trends. Implement Continuous Improvement Practices Regularly review and refine your supply chain processes. Conduct performance audits, gather feedback, and identify areas for improvement to ensure sustained supply and demand alignment. Importance: Continuous improvement drives long-term efficiency and growth. Actionable Tip: Use KPIs to measure and improve supply chain performance. Train Your Workforce Empower your team with the right skills and knowledge. KnoWerX’s Professional Training programs in Supply Chain Management equip professionals with the expertise needed to achieve supply and demand alignment and drive organizational growth. Importance: A skilled workforce ensures effective implementation of strategies. Actionable Tip: Enroll your team in specialized training programs to stay updated on best practices. Adopt a Customer-Centric Approach Align your supply chain with customer needs by focusing on delivering value. Understand their pain points, preferences, and expectations to ensure your supply chain meets their demands effectively. Importance: Customer-centricity boosts satisfaction and loyalty. Actionable Tip: Use CRM tools to gather and analyze customer data for better alignment. Frequently Asked Questions Ending Notes By implementing these strategies, businesses can achieve supply and demand alignment, reduce costs, improve customer satisfaction, and drive growth. At KnoWerX, we are committed to helping professionals and organizations excel in supply chain management through our high-quality training programs and expert guidance. Join KnoWerX today and take the first step toward mastering supply and demand alignment for a successful and sustainable future! Image Reference: Freepik Disclaimer: All trademarks, logos, and brand names are the property of their respective owners. All company, product, and service names used in this website are for identification purposes only. Use of these names, trademarks, and brands does not imply endorsement.
Six Sigma Goals: Boost Quality, Cut Waste
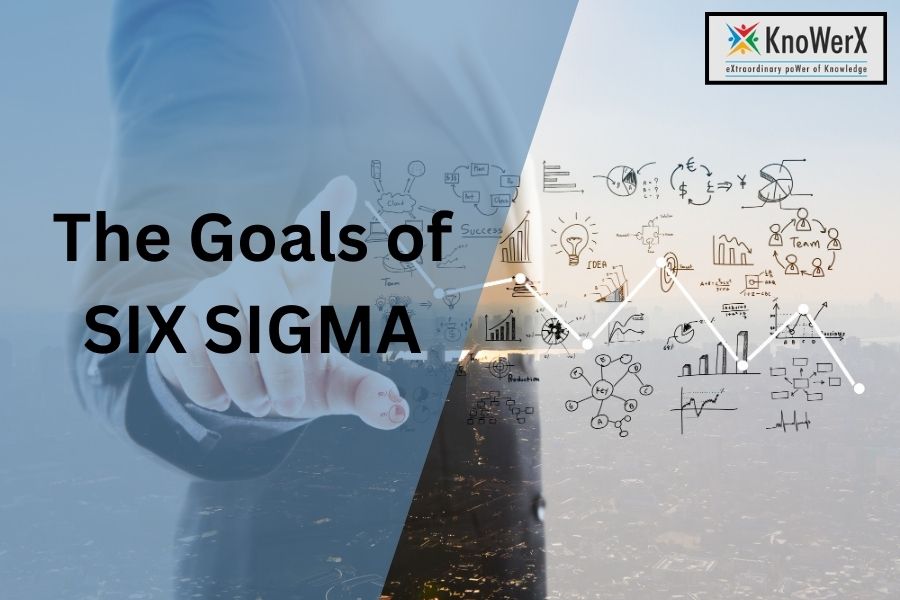
Six Sigma Goals: Boost Quality, Cut Waste At KnoWerX, we understand the importance of Six Sigma in transforming businesses by driving quality and reducing waste. As an industry leader in Supply Chain Management Training, we empower professionals with the knowledge and skills to achieve operational excellence. Here are some actionable tips to help you align with the goals of Six Sigma and maximize its benefits: 1. Focus on Customer Satisfaction One of the primary goals of Six Sigma is to enhance customer satisfaction by delivering high-quality products and services. Identify customer needs through surveys, feedback, and market research to understand their expectations. Measure performance metrics like defect rates and delivery times to pinpoint areas for improvement. Continuously refine processes to ensure your offerings not only meet but exceed customer expectations, fostering loyalty and long-term relationships. 2. Reduce Process Variability Variability in processes leads to defects, inefficiencies, and inconsistent outcomes. Use Six Sigma methodologies like DMAIC (Define, Measure, Analyze, Improve, Control) to identify the root causes of variability. Implement statistical tools such as control charts and process mapping to monitor and stabilize processes. By minimizing variations, you can ensure consistent quality, reduce rework, and enhance overall process reliability. 3. Eliminate Waste Six Sigma aims to reduce waste in all forms, including time, resources, and materials. Streamline processes by identifying and eliminating non-value-added activities, such as unnecessary steps or redundant tasks. Optimize resource utilization by reallocating efforts to high-impact areas. This not only improves efficiency but also contributes to cost savings and environmental sustainability, making your operations leaner and more effective. 4. Enhance Operational Efficiency By setting clear goals of Six Sigma, organizations can significantly improve operational efficiency. Train your team to identify bottlenecks and inefficiencies in workflows. Use data-driven solutions to address these issues and implement robust monitoring systems to track progress. Regularly review and refine processes to ensure they remain aligned with organizational objectives, driving sustained improvements over time. 5. Drive Data-Driven Decision Making Six Sigma emphasizes the use of data and statistical tools to make informed decisions. Equip your team with the skills to analyze data effectively, using techniques like regression analysis and hypothesis testing. Identify root causes of problems and implement targeted solutions to address them. By fostering a data-driven culture, you can ensure that decisions are based on facts rather than assumptions, leading to better outcomes and reduced risks. 6. Foster a Culture of Continuous Improvement The goals of Six Sigma are not just about achieving short-term results but fostering a culture of continuous improvement. Encourage employees to embrace change, innovate, and take ownership of their processes. Provide regular training and development opportunities to keep your team updated on the latest Six Sigma tools and techniques. Celebrate successes and learn from failures to create an environment where excellence is the norm. 7. Achieve Cost Savings By reducing defects and waste, Six Sigma helps organizations achieve significant cost savings. Focus on improving process efficiency and quality to lower operational costs, such as rework, scrap, and downtime. Invest in preventive measures to avoid costly errors and delays. These savings can be reinvested into growth initiatives, giving your organization a competitive edge in the market. 8. Align with Organizational Objectives Ensure that your Six Sigma initiatives align with your organization’s broader objectives. Set measurable goals that are specific, achievable, and time-bound. Track progress using key performance indicators (KPIs) and regularly communicate results to stakeholders. Celebrate milestones and successes to keep your team motivated and focused on achieving long-term strategic goals. Frequently Asked Questions Ending Notes At KnoWerX, we are committed to helping professionals like you achieve the goals of Six Sigma through our industry-leading training programs. With over 32 years of collective experience, we provide the best quality education at the most competitive prices in the industry. Join us to learn the best practices, gain domain knowledge, and earn relevant certifications for your professional growth. Let KnoWerX be your partner in driving quality, reducing waste, and achieving operational excellence with Six Sigma! Image Reference: Freepik Disclaimer: All trademarks, logos, and brand names are the property of their respective owners. All company, product, and service names used in this website are for identification purposes only. Use of these names, trademarks, and brands does not imply endorsement.
Improving Warehouse Efficiency: Your 2025 Blueprint
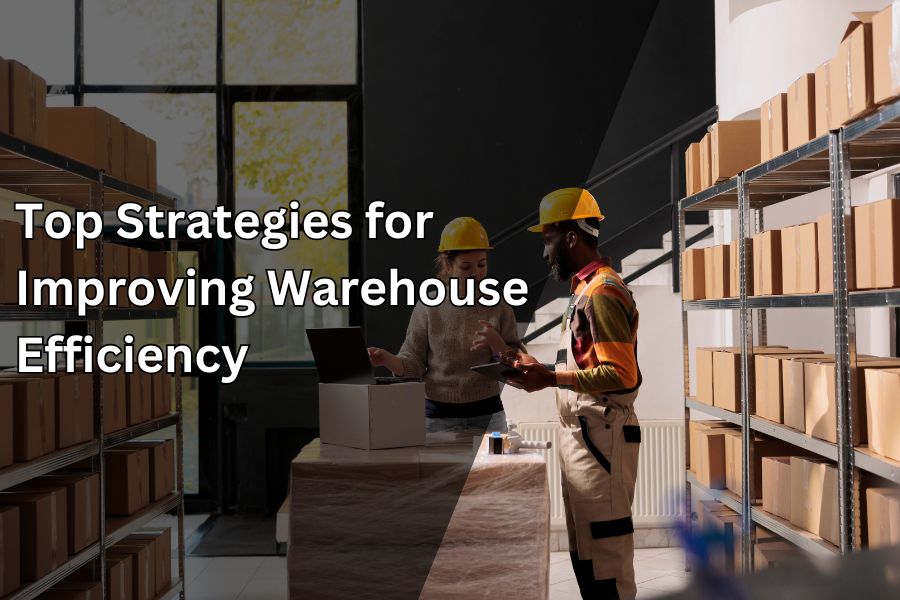
Top Strategies for Improving Warehouse Efficiency Efficient warehouse operations are essential for businesses to maintain a competitive edge in the supply chain. A well-organized warehouse not only reduces costs but also enhances customer satisfaction by ensuring timely deliveries. Below are some top strategies for improving warehouse efficiency, including the use of innovative techniques like cross-docking and lean logistics. Optimize Warehouse Layout The layout of your warehouse plays a crucial role in enhancing efficiency. A poorly designed warehouse can lead to wasted time and energy, which directly affects productivity and operational costs. Consider these tips: Reduce travel time: Arrange inventory to minimize the distance workers need to travel. For example, frequently picked items should be located near packing and shipping areas. Categorize inventory: Place high-demand items in easily accessible locations while storing seasonal or slow-moving inventory in less prominent areas. Implement slotting: Regularly analyze item movement and sales trends to ensure that products are stored in locations that maximize picking efficiency. Design clear pathways: Ensure that aisles are wide enough to accommodate equipment like forklifts and are free from obstructions to facilitate smooth movement. By optimizing the warehouse layout, businesses can enhance operational flow and reduce unnecessary delays, thereby improving warehouse efficiency. Embrace Technology Technology plays a pivotal role in modernizing warehouses and improving efficiency. Automating manual processes can significantly reduce errors and speed up operations. Here are some tools and systems to consider: Warehouse Management Systems (WMS): A WMS helps automate inventory tracking, order picking, and shipping processes. It provides real-time data on stock levels, which aids in better decision-making. Barcode Scanning & RFID Technology: These tools accelerate the identification and tracking of items, reducing manual errors and improving inventory accuracy. Automated Guided Vehicles (AGVs): AGVs and robotics can handle material movement efficiently, allowing employees to focus on more complex tasks. Predictive Analytics: Use data analytics to forecast demand, optimize inventory levels, and plan resource allocation effectively. By embracing these technologies, warehouses can become smarter and more agile, further improving warehouse efficiency. Leverage Cross-Docking Cross-docking is a strategy that eliminates the need for long-term storage by transferring incoming goods directly to outbound transportation. It’s an efficient approach to handling inventory and can greatly reduce operational costs. Here’s why cross-docking is beneficial: Reduced storage costs: Goods don’t sit idle in the warehouse, minimizing storage requirements. Faster order fulfillment: By bypassing traditional storage processes, products can reach customers more quickly. Improved inventory turnover: Regular movement of goods ensures better stock rotation and reduces the risk of obsolescence. To implement cross-docking effectively, businesses need to: Collaborate closely with suppliers to ensure timely deliveries. Utilize advanced scheduling software to align inbound and outbound shipments. Train employees to handle goods swiftly and accurately during the transfer process. Cross-docking is particularly useful for perishable goods, high-demand items, and products with a short shelf life. It’s a proven method for improving warehouse efficiency Adopt Lean Logistics Lean logistics focuses on minimizing waste and optimizing processes throughout the supply chain. By adopting lean principles, businesses can achieve greater efficiency and cost savings. Key elements include: Just-in-time (JIT) Inventory: Order stock based on demand forecasts to avoid overstocking and reduce carrying costs. This approach ensures that inventory arrives just when it’s needed. Continuous Improvement (Kaizen): Encourage employees to identify inefficiencies and suggest process enhancements. A culture of continuous improvement fosters innovation and teamwork. Streamlined Workflows: Analyze repetitive tasks and identify bottlenecks to streamline operations. Use tools like value stream mapping to visualize and improve processes. By focusing on lean logistics, warehouses can reduce waste, improve productivity, and enhance overall operational efficiency. This is a vital step in improving warehouse efficiency across all operations. Improve Picking and Packing Processes Efficient picking and packing are critical for timely order fulfillment and customer satisfaction. Here are some strategies to enhance these processes: Use Picking Methods: Choose the right picking method based on order volume and warehouse layout. Popular methods include: Zone Picking: Assign specific zones to workers, reducing travel time within the warehouse. Batch Picking: Pick multiple orders simultaneously to minimize trips. Wave Picking: Schedule picking waves based on shipping deadlines or order priorities. Leverage Technology: Equip workers with handheld devices or voice-picking systems to improve accuracy and speed. Ergonomic Tools: Provide tools such as adjustable workstations and carts to reduce physical strain and enhance productivity. Regularly reviewing and optimizing picking and packing processes can significantly boost performance, contributing to improving warehouse efficiency. Enhance Inventory Management Effective inventory management is the backbone of warehouse efficiency. Poor inventory practices can lead to stockouts, overstocking, and increased operational costs. Consider the following techniques: Cycle Counting: Conduct regular cycle counts instead of annual inventory checks to ensure ongoing accuracy. ABC Analysis: Categorize inventory into three groups (A, B, and C) based on value and frequency of use. Focus more resources on high-value (A) items. Real-Time Monitoring: Use software to track inventory levels in real-time, enabling quick responses to changes in demand. Enhanced inventory management ensures that the right products are available at the right time, reducing delays and improving warehouse efficiency. Focus on Employee Training and Safety A skilled and motivated workforce is crucial for efficient warehouse operations. Providing employees with the right training and tools ensures they can perform their tasks effectively. Focus on: Comprehensive Training: Offer training programs on equipment handling, safety protocols, and efficient workflow practices. Safety Measures: Invest in safety equipment, conduct regular inspections, and enforce strict safety guidelines to reduce workplace accidents. Employee Engagement: Recognize and reward employee contributions to boost morale and productivity. By prioritizing training and safety, businesses can create a healthier and more productive work environment, further improving warehouse efficiency. Monitor Key Performance Indicators (KPIs) Tracking KPIs is essential for identifying strengths and areas for improvement in warehouse operations. Some key metrics to monitor include: Order Accuracy Rate: Measure the percentage of orders shipped without errors. Dock-to-Stock Cycle Time: Track the time taken to move goods from the receiving dock to storage. Inventory Turnover: Calculate how often inventory is sold and replaced over a period. Regularly
Why CLTD Qualification is Essential for Supply Chain Experts
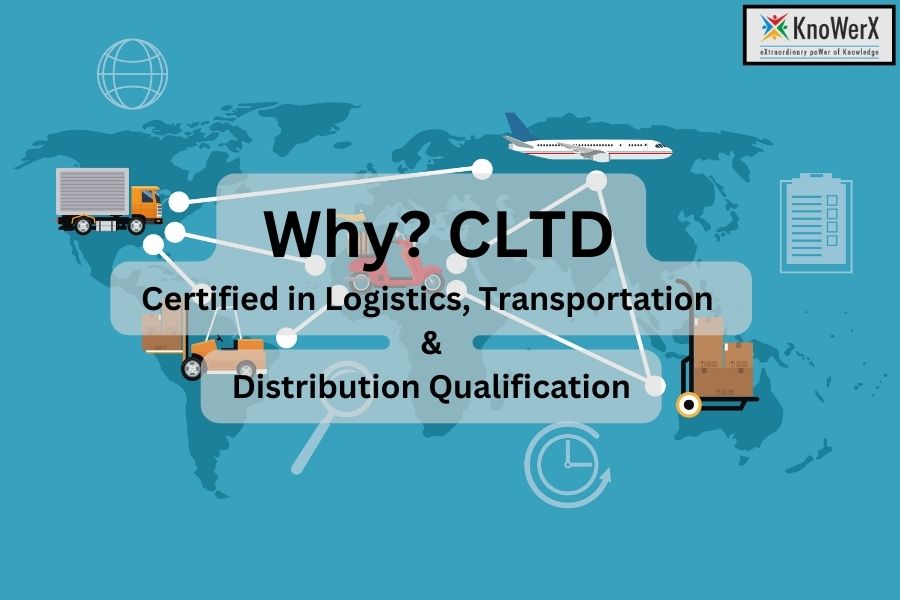
Why CLTD Qualification is Essential for Supply Chain Experts The CLTD qualification is an important certification for any professional in the supply chain and logistics industry. If you’re looking to advance your career in logistics, transportation, and distribution, here’s how the CLTD qualification can benefit you. At KnoWerX, we believe in empowering professionals with the skills and certifications they need to excel. Knowledge in Logistics and Distribution The CLTD qualification provides comprehensive knowledge of logistics, transportation, and distribution processes. It enables professionals to gain expertise in managing the entire logistics process, from procurement to delivery. With KnoWerX’s professional training programs, you will be equipped to handle complex logistical challenges in real-world scenarios. Improved Career Opportunities It has various career opportunities after achieving the CLTD qualification. With the increase in the growth of logistics in various parts of the world, companies have begun to seek certified professionals who can handle their supply chain operations. With this qualification, you will be able to showcase your advanced skills and experience, thus making you an attractive candidate for senior roles in logistics and transportation. Higher Earning Potential Professionals in the supply chain industry are paid higher than those who are not certified. The CLTD qualification puts you on the pedestal as an expert in logistics and distribution, thus making you eligible for better pay and promotions. KnoWerX’s extensive courses and industry insights ensure that you are well-equipped to command a competitive salary. International Recognition CLTD is an international certification; therefore, your certification will be respected by employers globally. This will open doors to international assignments and career growth in other geographic locations. In this regard, you become aligned with a global standard of logistics and distribution through this KnoWerX certification. The logistics and supply chain sectors are continuously evolving with new technologies, regulations, and best practices that emerge regularly. CLTD qualification ensures you stay abreast of the trends and keep you ahead of them all. KnoWerX ensures that you receive training up-to-date with the latest developments in logistics and distribution management. Develop Confidence for Leadership Roles The CLTD qualification does not only improve your technical skills but also builds up your leadership capabilities. Once you know how logistics management works, you can easily assume a leadership position in your organization and manage teams or even influence the efficiency of supply chain processes. KnoWerX’s training builds both your strategic and operational leadership skills. Networking Opportunities KnoWerX offers a platform to network with like-minded professionals and experts in the field of supply chain management. Gaining your CLTD qualification opens doors to a broader professional network, providing valuable contacts and career opportunities that can propel your career forward. Effective Problem-Solving Skills You will develop critical problem-solving through the CLTD program because, by learning through qualification, you will be able to estimate, plan, and implement effective strategies in logistics transportation, and distribution management for you to be ready to present at KnoWerX that equips you with ample confidence and competence to practice for real-world problems to overcome. Improved Organizational Efficiency CLTD certified professionals are qualified with best practices in logistically smoothing the distribution. This means that an organization can get on its feet more efficiently, cut costs, and be profitable. With the acquisition of this qualification, one stands as a gem to the organization as it is better positioned to influence improvements on their operations. A step forward towards more specialization The CLTD qualification provides an excellent base for further specialization in the logistics and supply chain field. If you intend to expand your expertise into areas such as Demand Driven Leader Professional (DDLP) or other advanced certifications, the CLTD serves as a stepping stone, building a strong base of knowledge for continued professional development. Frequently Asked Questions Ending Notes All in all, the CLTD qualification is a very important resource that anyone in the logistics and transportation business needs. At KnoWerX, we can provide you with an expert-led training program for sure. Whether you are new or in the senior management stage, the CLTD qualification is sure to take you higher in your professional career. Additionally, pursuing certifications such as the Demand Driven Leader Professional can further enhance your strategic impact and leadership capabilities. Image Reference : Freepik Disclaimer: All trademarks, logos, and brand names are the property of their respective owners. All company, product, and service names used in this website are for identification purposes only. Use of these names, trademarks, and brands does not imply endorsement.
Top 10 Supply Chain KPIs for Operational Excellence
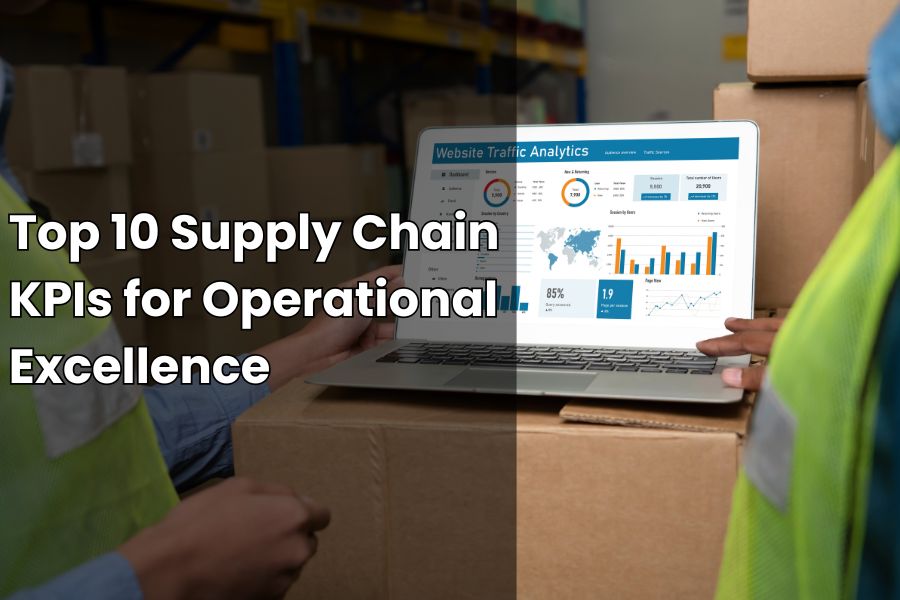
10 Key Performance Indicators (KPIs) for Supply Chain Success Ever wondered what sets a successful supply chain apart from the rest? It’s not just about moving products efficiently—it’s about measuring every step to ensure optimal performance. Key Performance Indicators (KPIs): the metrics that hold the key to unlocking supply chain excellence. From streamlining inventory management to enhancing customer satisfaction, the right Supply Chain KPI can transform your operations and drive growth. This guide dives into 10 essential KPIs you need to track for supply chain success. Whether you’re a business owner, manager, or logistics expert, this information will empower you to stay ahead in today’s competitive landscape. Why Are Supply Chain KPIs Important? Supply Chain KPIs serve as a roadmap to achieving operational excellence. They allow businesses to: Identify inefficiencies: Pinpoint areas that need improvement. Monitor progress: Track advancements toward strategic goals. Improve decision-making: Provide actionable insights for better management. Enhance customer satisfaction: Ensure timely deliveries and accurate orders. By selecting and monitoring the right Supply Chain KPIs, companies can gain a competitive edge in today’s market. 10 Supply Chain KPIs to Monitor 1. Cash-to-Cash Cycle Time This KPI measures the time taken to convert investments in inventory into cash from sales. A shorter cycle indicates better efficiency in cash flow management. The formula for calculating this KPI is: Cash-to-Cash Cycle Time = Days of Inventory (DOI) + Days Sales Outstanding (DSO) – Days Payables Outstanding (DPO). Tracking this KPI ensures that businesses have healthy liquidity and effective inventory management. 2. Perfect Order Rate The perfect order rate reflects the percentage of orders delivered without any issues, such as delays, damage, or incorrect documentation. A high perfect order rate means the supply chain is operating effectively and meeting customer expectations. Perfect Order Rate = (% Delivered On-Time) × (% Complete) × (% Undamaged) × (% Accurate Documentation). This Supply Chain KPI directly correlates with customer satisfaction levels. 3. Order Fill Rate This KPI indicates the percentage of customer orders that are fulfilled entirely from available stock without backorders. A higher order fill rate reflects effective inventory planning and stocking strategies. Order Fill Rate = (Total Orders Shipped Complete / Total Orders Placed) × 100. Monitoring this Supply Chain KPI helps businesses minimize stockouts and improve reliability. 4. Customer Order Cycle Time The customer order cycle time measures the average time taken from receiving a customer order to delivering the product. Shorter cycle times indicate better efficiency in order processing and logistics. Customer Order Cycle Time = (Delivery Date – Order Date) / Total Number of Orders Shipped. This Supply Chain KPI ensures that businesses meet delivery commitments efficiently. 5. Inventory Turnover Rate This KPI shows how often inventory is sold and replaced over a specific period. A high inventory turnover rate reflects strong demand and efficient inventory management. Inventory Turnover Rate = Cost of Goods Sold (COGS) / Average Inventory. Using this Supply Chain KPI, companies can avoid overstocking or understocking scenarios. 6. Days Inventory Outstanding (DIO) DIO measures the average number of days a company holds inventory before selling it. Lower DIO values signify efficient inventory management and faster turnover. Days Inventory Outstanding = (Average Inventory / Cost of Goods Sold) × Number of Days in Period. This Supply Chain KPI is vital for evaluating inventory performance. 7. Supply Chain Costs This KPI encompasses all expenses related to the supply chain, including production, warehousing, transportation, and distribution costs. By monitoring these costs, businesses can identify areas for cost savings and improve overall efficiency. Tracking Supply Chain Costs KPI ensures a balance between service levels and cost efficiency. 8. On-Time Delivery (OTD) On-time delivery measures the percentage of orders delivered on or before the promised date. High OTD rates indicate a reliable and efficient supply chain. On-Time Delivery = (Number of On-Time Deliveries / Total Deliveries) × 100. This Supply Chain KPI is essential for maintaining customer trust and loyalty. 9. Freight Cost per Unit This KPI calculates the average transportation cost per unit shipped. Monitoring this metric helps in managing and optimizing shipping expenses. Freight Cost per Unit = Total Freight Costs / Number of Units Shipped. Reducing freight costs is a key goal of any effective Supply Chain KPI strategy. 10. Supplier On-Time Delivery Rate This KPI measures the percentage of orders that suppliers deliver on time. High rates signify reliable suppliers and a strong procurement process. Supplier On-Time Delivery Rate = (Number of On-Time Supplier Deliveries / Total Supplier Deliveries) × 100. This Supply Chain KPI ensures smooth operations and prevents delays. FAQs: Frequently Asked Questions End Notes KnoWerX is committed to helping supply chain professionals and organizations thrive by providing world-class training and certifications. By understanding and leveraging the right Supply Chain KPIs, you can unlock new opportunities, streamline operations, and deliver exceptional value to your business. Whether you’re aiming to enhance efficiency, reduce costs, or improve customer satisfaction, tracking these KPIs is essential for sustained success in this dynamic field. Join KnoWerX to elevate your career prospects with APICS certifications and specialized supply chain management courses. With the right skills, knowledge, and a focus on critical KPIs, you can become a leader in the ever-growing supply chain industry. Image Reference: Freepik Disclaimer: All trademarks, logos, and brand names are the property of their respective owners. All company, product, and service names used in this website are for identification purposes only. Use of these names, trademarks, and brands does not imply endorsement.